SMC is on the upswing (and check out this design competition)
There’s a lot going on with sheet molding compound (SMC) right now, including a design competition for best SMC design, with the winner announced at Composites Europe.
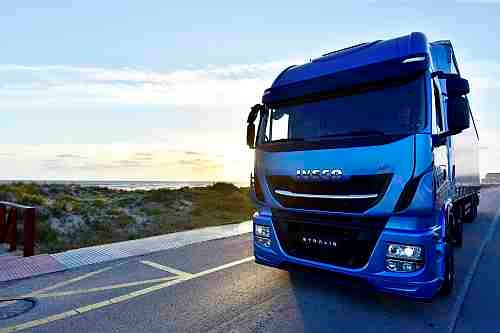
GSI molds components of this Iveco truck cab using sheet molding compound (SMC).
There’s a lot going on with sheet molding compound (SMC) right now. While it’s a well-known legacy material, first developed in the 1960s, the chopped glass/resin/filler mix in easily-handled continuous sheet form is on a growth trajectory. Improvements in SMC formulations and lower density have heightened its appeal to automotive OEMs. CW has written several recent articles about improvements in SMC: http://www.compositesworld.com/articles/low-density-smc-better-living-through-chemistry; http://www.compositesworld.com/blog/post/ashland-unveils-low-density-high-performance-smc.
And, no fewer than four market reports within the last months predict robust growth. SMC and bulk molding compounds (BMC) are expected to grow at a CAGR of more than 6.5% from 2016 to 2021, with a value of $3.5 billion USD, says a report from Market Research Future (Pune, India). Market research firm Lucintel (Irving, TX, US) said this month that the future of the global SMC market looks good, with the global SMC market expected to reach an estimated $3.2 billion by 2021 with growth at a CAGR of 4.3% from 2016 to 2021. They cite increasing penetration of carbon fiber-based-SMC, increasing focus of the major players towards low density SMC, and introduction of Direct-SMC (a relatively new process in which SMC is formulated and molded immediately, eliminating the need for the several-day maturation period required with conventional SMC; here’s a CW story on Direct-SMC: http://www.compositesworld.com/articles/formulation-flexibility-direct-smc ).
Which brings me to Global Systems International SpA (GSI, Milan, Italy), a company I was not previously acquainted with. GSI, with plants in Europe, the US, China and Brazil, is well known (at least, to most of you) for making parts with SMC, as well as Direct Long Fiber Thermoplastic (D-LFT), Low Weight Reinforced Thermoplastic (LWRT) and Glass Mat Thermoplastic (GMT), for an array of automotive, truck and equipment manufacturers. In a press release from resin supplier Aliancys AG (Schaffhausen, Switzerland, formerly DSM Composite Resins), GSI talks SMC and its design process for making parts.
According to the company, SMC can be molded at much faster rates than resin transfer molding (RTM), and it offers dimensional accuracy close to metal, while allowing part performance consistency to be more easily controlled. Compared to metal technologies, SMC is in most cases more cost-effective at production runs of 500 to 200,000 parts per year, and brings the additional benefit of lightweighting, says Matteo Cortesi, group technical director at GSI. “Many of the OEMs and end-customers that we are dealing with know very well the benefits of SMC. They approach us with clear ideas on part design, and invite us early in the process to discuss how to scale up their designs to real-life manufacturing, to ensure that the final production can run in a smooth manner, making parts with consistent quality and predictable shape.”
After receiving initial information from the customer, a GSI team will evaluate 3D models and exchange technical data on the design, and discuss the practicalities of high volume manufacturing (including available technical solutions, rough process lay-out, anticipated challenges and risks). Says Cortesi, “Based on our knowledge of materials we propose the appropriate SMC material system. We also define the investments required for tooling and process automation, and then calculate anticipated part cost based on the quality requirements of the customer, anticipated cycle times, and basic assumptions on waste and components finishing. Meanwhile we define a detailed project plan for design fine-tuning and pre-production activities, taking into account product and process design uncertainties and risks.”
“After the customer accepts our proposal, we form a joint team that will be responsible for scale-up”, comments Erica Murello, marketing and communication coordinator at GSI. “In line with key project milestones, we finalize detailed part design, order tooling and equipment, and define the full supply chain (purchasing of raw materials, parts processing and finishing, logistics, quality management procedures). Also in this phase we make prototypes with the customer and ensure critical tests are performed prior to production.”
GSI reportedly has a great track record of manufacturing quality transportation parts in SMC. The company serves Automobili Lamborghini, Ferrari, Audi, Claas, Caterpillar, CNHi (maker of IVECO trucks) and ABB Sace (electrical equipment), among others.
GSI is a member of the European Alliance of SMC BMC (Brussels, Belgium), and that group is inviting students and young designers to participate in the SMC BMC Design Award 2017. This design competition promotes the use of SMC BMC material systems to demonstrate the positive contributions they bring to end-users and the environment. A substantial prize of 10,000 € will be handed to the winning design team at a special award ceremony during the upcoming Composites Europe show in Stuttgart (19-21 September 2017). More information about the design competition can be found at http://smcbmc-europe.org/award.php.
Related Content
The making of carbon fiber
A look at the process by which precursor becomes carbon fiber through a careful (and mostly proprietary) manipulation of temperature and tension.
Read MoreMaterials & Processes: Fibers for composites
The structural properties of composite materials are derived primarily from the fiber reinforcement. Fiber types, their manufacture, their uses and the end-market applications in which they find most use are described.
Read MoreComposite rebar for future infrastructure
GFRP eliminates risk of corrosion and increases durability fourfold for reinforced concrete that meets future demands as traffic, urbanization and extreme weather increase.
Read MoreThe state of recycled carbon fiber
As the need for carbon fiber rises, can recycling fill the gap?
Read MoreRead Next
From the CW Archives: The tale of the thermoplastic cryotank
In 2006, guest columnist Bob Hartunian related the story of his efforts two decades prior, while at McDonnell Douglas, to develop a thermoplastic composite crytank for hydrogen storage. He learned a lot of lessons.
Read MoreComposites end markets: Energy (2024)
Composites are used widely in oil/gas, wind and other renewable energy applications. Despite market challenges, growth potential and innovation for composites continue.
Read MoreCW’s 2024 Top Shops survey offers new approach to benchmarking
Respondents that complete the survey by April 30, 2024, have the chance to be recognized as an honoree.
Read More