CAMX 2022 exhibit preview: Bally Ribbon Mills
Bally Ribbon Mills’ highlights its capabilities in design and manufacture of woven structural shapes for hybrid composite structures used in aerospace applications.
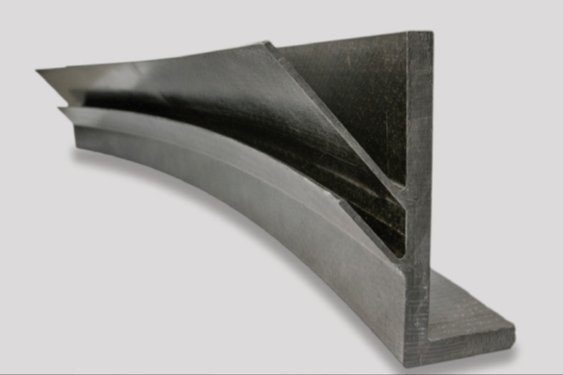
Photo Credit: Bally Ribbon Mills
Bally Ribbon Mills’ (BRM, Bally, Pa., U.S.) Advanced Product Group designs and produces woven structural shapes for hybrid composite structures used in aerospace applications, bridge structures, sporting gears and medical equipments. The lightweight, integrated design of Bally’s distinct woven structures affords higher levels of strength and opportunities for new design applications previously unattainable with build-up or weld-reinforcement areas, Bally says.
BRM’s Advanced Product Group is a team of seasoned engineers, technicians and manufacturing personnel dedicated to the development of solutions to challenging woven material needs. Given the customer’s product constraints, desired mechanical properties, cost of product, operating temperature and operating environment, BRM says it is capable of handling every stage of preform development — from the initial design and prototype development to final product design and fabrication.
Bally says its Advanced Products Group devotes effort and experience to the design and manufacture of complex shapes using difficult-to-weave fibers while minimizing yarn damage and controlling costs. The group combines more than 70 years of first-hand experience in weaving, including 2D woven shapes; 3D Orthogonal and angle interlock multi-layer woven materials; 3D complex shapes; high-performance tapes and webbing; braids, spiral and polar weaves; unidirectional (UD) woven narrow fabrics; tubular webbing and woven materials; and hybrids.
The Advanced Product Group markets a wide selection of woven materials that can be combined with virtually any available resin system, according to the company. These products are suitable for a variety of prepreg, wet lay-up and resin transfer operations. They can also be supplied as a dry preform or greige fabric in “B” stage prepreg — or as a resin transfer mold (RTM) finished part.
Bally Ribbon Mills’ products are constructed from a wide variety of reinforcing fibers and textile forms. Carbon/Graphite, Nicalon, quartz, Kevlar, glass, metal, hybrids and other fibers can be used in the construction of its 2D and 3D woven preforms.
BRM reports its 3D woven composites are particularly successful in aviation heat shield applications such as multifunctional thermal protection systems. These systems are mission-critical components, particularly in space exploration vehicles, and 3D woven composites reduce weight and cost while maintaining good performance in TPS systems. The ability to vary yarn types, density, thickness, width and resin type enables BRM to create customizable TPS to fit each specific mission or application’s needs, the company says.
BRM uses the film infusion process to infuse a variety of resins to these complex 3D woven shapes. This ability enables BRM to ship its 3D woven joints or structures as premade assemblies, saving customers from processing steps that may require time, work and specialized machinery. BRM’s film infusion capability also enables control of more steps during the 3D woven assembly manufacturing process, promoting consistent quality control.
Related Content
-
A new era for ceramic matrix composites
CMC is expanding, with new fiber production in Europe, faster processes and higher temperature materials enabling applications for industry, hypersonics and New Space.
-
Carbon fiber in pressure vessels for hydrogen
The emerging H2 economy drives tank development for aircraft, ships and gas transport.
-
Infinite Composites: Type V tanks for space, hydrogen, automotive and more
After a decade of proving its linerless, weight-saving composite tanks with NASA and more than 30 aerospace companies, this CryoSphere pioneer is scaling for growth in commercial space and sustainable transportation on Earth.