A new paradigm in airframe construction?
MTorres, a major supplier of automated manufacturing equipment for composites, has revealed a new way to manufacture airframe structure using composites.
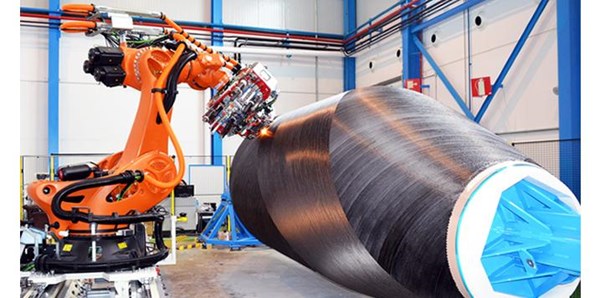
An MTorres head lays dry carbon fiber on the company's new fuselage concept.
I heard the news, through CW colleague Ginger Gardiner and composites industry and aviation researcher and professor Dr. David Pritchard, that Spanish industrial group MTorres (Torres de Elorz, Navarra, Spain), a major supplier of automated manufacturing equipment for composites, had revealed an entirely new and radically different way to manufacture airframe structure using composites. When I had spoken with the company in March at JEC World in Paris, they said that an announcement would be coming at the upcoming Paris Air Show, but gave no hint of its magnitude.
The company did speak on May 26th with journalists from Madrid’s largest newspaper El Pais during an event at MTorres’ facility in Fuente Alamo, Spain, and unveiled the new technology, which consists of a one-piece, monocoque fuselage that it says requires no rivets or fasteners, nor molds. Developed over the past 6 months by a team of 30 people, including company founder Manuel Torres, project head Sebastián Díaz was quoted in the El Pais article as saying the new fuselage technology “changes the current manufacturing paradigm" of aircraft.
I’ve submitted questions to MTorres, and am waiting for more specifics. But, as we reported in our News item (http://www.compositesworld.com/news/revolutionary-fuselage-concept-unveiled-by-mtorres ), the concept apparently may involve producing C-frames or ring frames in a separate process, with frames held together to create an outer mold line (OML) surface, over which the fuselage skin is fiber placed using MTorres’ fiber placement head and dry carbon fiber tape. The frames are reportedly integrated into the fuselage. The structure is then infused, says MTorres, and oven cured. The company says that the "final phase" of the material used in production, possibly the dry tape itself, is made by MTorres (more information on all materials is coming), which could reduce raw material cost by up to 50%, according to the El Pais story. By eliminating rivets, fuselage weight can be reduced by 10% to 30%, said MTorres at the May 26 event, and tooling costs as well as labor costs would be significantly reduced. Spanish press reports quote MTorres as saying that 6,000 hours of work were saved with this new fabrication concept, compared to existing methods. While the prototype presented is a fuselage, MTorres is reportedly also adapting the technology to wings, as well.
An MTorres spokesperson told CW “So far we have seen huge interest. This concept is the result of a 360º analysis, trying to cut costs on material, on tooling, on processes, on cycle time, while increasing quality using the latest technology available.” If you’re attending the Paris Air Show, from June 19-25, a prototype-scale fuselage made using this technology will be displayed at the MTorres booth, Hall 1 Stand G318. Here's a link to the MTorres press release about the Paris Air Show and the new technology: http://www.mtorres.es/en/communication/news/latest-technological-developments-mtorres-le-bourget-2017.
For his help, CW thanks Pritchard, who is Associate Professor/Aviation Researcher at State University of New York-Empire State College (Saratoga Springs, NY, US) and author of “Aerospace 4.0: Implications to the New Manufacturing Ecosystem”, a paper presented at the Civil Aircraft Industry International Forum (May 10-11, 2017, Shanghai, China).
We will get more information and keep you posted on this, and if you have more information about this concept, please contact me.
Related Content
Materials & Processes: Composites fibers and resins
Compared to legacy materials like steel, aluminum, iron and titanium, composites are still coming of age, and only just now are being better understood by design and manufacturing engineers. However, composites’ physical properties — combined with unbeatable light weight — make them undeniably attractive.
Read MorePrice, performance, protection: EV battery enclosures, Part 1
Composite technologies are growing in use as suppliers continue efforts to meet more demanding requirements for EV battery enclosures.
Read MoreMaterials & Processes: Fibers for composites
The structural properties of composite materials are derived primarily from the fiber reinforcement. Fiber types, their manufacture, their uses and the end-market applications in which they find most use are described.
Read MoreThe making of carbon fiber
A look at the process by which precursor becomes carbon fiber through a careful (and mostly proprietary) manipulation of temperature and tension.
Read MoreRead Next
From the CW Archives: The tale of the thermoplastic cryotank
In 2006, guest columnist Bob Hartunian related the story of his efforts two decades prior, while at McDonnell Douglas, to develop a thermoplastic composite crytank for hydrogen storage. He learned a lot of lessons.
Read MoreCW’s 2024 Top Shops survey offers new approach to benchmarking
Respondents that complete the survey by April 30, 2024, have the chance to be recognized as an honoree.
Read MoreComposites end markets: Energy (2024)
Composites are used widely in oil/gas, wind and other renewable energy applications. Despite market challenges, growth potential and innovation for composites continue.
Read More