VectorFusion™ Reinforcements Utilized with CCP Composites’ OptiPLUS® Resin for Infused Tooling Applications
With recent advances in CCP Composites’ OptiPLUS® infusion grade, low viscosity, shrink-controlled polyester resin, and the proper selection of Vectorply reinforcements, mold building can be greatly reduced from weeks to only a day or two.
Share
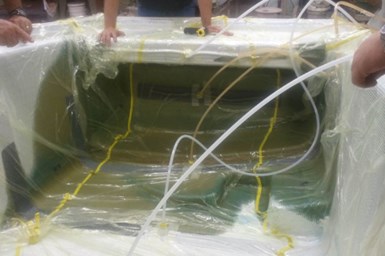
C-BX material is manufactured on a LIBA MAX 5 machine.
Traditionally, FRP mold building has been a laborious process that can take up to two weeks, or longer to properly complete. Each layer must be applied and allowed to cure to minimize excessive heat and shrinkage. This is done to avoid fiber print-through and/or warping. With recent advances in CCP Composites’ OptiPLUS® infusion grade, low viscosity, shrink-controlled polyester resin, and the proper selection of Vectorply reinforcements, this timetable can be greatly reduced from weeks to only a day or two.
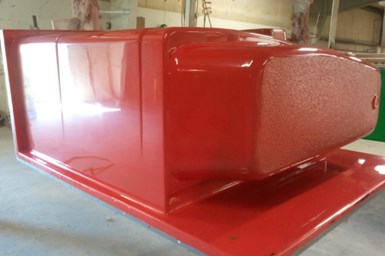
After going through the stitch head, C-BX material is put into roll form.
For large scale projects, typical chopped glass fiber reinforcements can not provide the stiffness and strength required to create a robust tool. Continuous fiber layers must be introduced in order to make a tool that is structurally sound, and yet light enough for transporting around the shop floor. Since the vacuum infusion process is employed it is also beneficial to use reinforcements with “built in” permeability, so that use of consumable items such as flow media can be drastically reduced. Core placement and fiber wet-out are significantly enhanced when done under a vacuum enhanced process.
VectorFusion™ reinforcements such as E-BXM 1715-6VC and E-TLYA 3612 provide a great combination of stiffness/strength, drapeability, and low profile (for good cosmetics). Reinforcements such as E-3LTi 10800 provide rapid thickness build up for monolithic laminates, while others such as E-LTi 3600 can be employed with sandwich (cored) laminates for reduced exotherm. Recommended, OptiPLUS® resins are: 040-8079 (fast gel time) or 040-8091 (slow gel time).
Typical Tooling Laminate Conversion
To replace a generic, general purpose hand laminated all chopped fiber mat laminate of approximately 0.325 in thickness, the following OptiPLUS® infused laminate is recommended (not including tooling gelcoat or barrier coats):
- Alcan D7760 Finishmat® – Tool Surface
- Vectorply E-BXM 1715-6VC
- Vectorply E-TLYA 3612
- Vectorply E-3LTi 10800 – Tool Backside
The 7760 Finishmat® is an acrylic fiber veil, which provides a resin-rich surface layer behind the gelcoat and/or barrier coat for extremely low profile while the following reinforcement fabrics provide increasingly higher mechanical properties and thickness. This laminate schedule is approximately 19% thinner, 18% lower in weight, and 30% stiffer compared to the generic 7 layer all chopped fiber tool (see below):
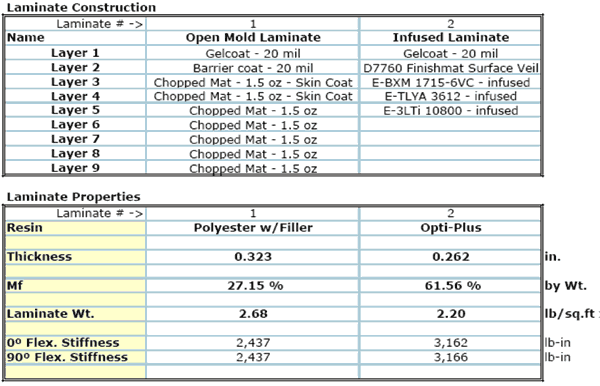
Please refer to the CCP website www.ccpcompositesus.com for additional laminate recommendations, as well as options for tooling gel coats, barrier coats and peroxide choices. Infused OptiPLUS® and VectorFusion™ molds can be used in the traditional FRP marketplace or in higher temperature thermoforming and pre-preg processing markets.
VectorFusion™ Products for OptiPLUS® Infused Tooling
Product Code | Total Weight | 0° | 90° | ±45°/+65° | CSM | Veil/Core | ||||
Longitudinal | Transverse | Double Bias | Weight | Weight | ||||||
oz/yd2 | g/m2 | oz/yd2 | g/m2 | oz/yd2 | g/m2 | oz/yd2 | g/m2 | oz/yd2 | oz/yd2 | |
E-BXM 1715-6VC | 36.95 | 1253 | n/a | n/a | n/a | n/a | 18.14 | 615 | 13.50 | 5.31 |
E-TLYA 3612 | 37.64 | 1276 | 12.80 | 434 | n/a | n/a | 23.64 | 802 | n/a | 1.20 |
E-TLYM 3615-6VC | 55.25 | 1873 | 12.80 | 434 | n/a | n/a | 23.64 | 802 | 13.50 | 5.31 |
E-LTi 3600 | 35.76 | 1212 | 17.84 | 605 | 17.92 | 608 | n/a | n/a | n/a | n/a |
E-2LTi 3600 | 35.84 | 1215 | 17.92 | 608 | 17.92 | 608 | n/a | n/a | n/a | n/a |
E-3LTi 10800 | 107.28 | 3637 | 53.52 | 1815 | 53.76 | 1823 | n/a | n/a | n/a | n/a |
For a complete listing of Vectorply standard products, please reference the standard product booklet or the Vectorply website at www.vectorply.com.
Find out more about Vectorly
Read Next
CW’s 2024 Top Shops survey offers new approach to benchmarking
Respondents that complete the survey by April 30, 2024, have the chance to be recognized as an honoree.
Read MoreComposites end markets: Energy (2024)
Composites are used widely in oil/gas, wind and other renewable energy applications. Despite market challenges, growth potential and innovation for composites continue.
Read MoreFrom the CW Archives: The tale of the thermoplastic cryotank
In 2006, guest columnist Bob Hartunian related the story of his efforts two decades prior, while at McDonnell Douglas, to develop a thermoplastic composite crytank for hydrogen storage. He learned a lot of lessons.
Read More