Composites end markets: Batteries and fuel cells (2024)
As the number of battery and fuel cell electric vehicles (EVs) grows, so do the opportunities for composites in battery enclosures and components for fuel cells.
Source | (Top left, clockwise) Ceylon Graphene and The Graphene Council, Bramble Energy, Kautex Textron and EKPO fuel cells.
Batteries
Global electric car stock 2010-2022 (million units). Source | “IEA Global EV Outlook 2023”
According to the “IEA Global EV Outlook 2023,” electric car sales were up 55% in 2022 despite the fact that total car sales fell by 3% relative to 2021. In just five years, from 2017 to 2022, electric car sales grew from ≈1 million to >10 million. More than 2.3 million electric cars were sold in Q1 2023 and IEA projected an annual total of 14 million, a 35% increase over 2022. While the number of internal combustion engine (ICE) car models continues to decrease each year, the number of electric car models is increasing at a rate of 30% from 2016-2022.
In its “Electric Vehicle Outlook 2023,” Bloomberg NEF predicts that electric vehicle (EV) sales will rise from 10.5 million to 27 million between 2022 and 2026. The EV share of global new passenger vehicle sales will grow from 14% in 2022 to 30% in 2026.
Global passenger vehicle sales by drivetrain – Economic Transition Scenario (left) and “The Picture Today” (right). Source | Fig. 2, “Electric Vehicle Outlook 2023” by Bloomberg NEF and EVO Report 2023 summary page
Note, however, that batteries are also needed for the growing field of EVs in the air, referred to as electric vertical takeoff and landing (eVTOL) aircraft. In a March 2023 report, IBA Insight reported a total of 7,487 eVTOL orders with 4,050 on backlog. As explained in a 2022 article by Leeham News, the power for an eVTOL is supplied by its battery system, with modules that are highly complex and energy levels higher than a Tesla car. Protection is key as there is no quick exit to a sidewalk in the case of a fire or thermal runaway.
Battery pack modules from Electroflight, now EvoLito. Source | Leeham News and EvoLito
Another issue is that aircraft are even more weight-sensitive than cars. Thus, aircraft batteries need to be light and safe, says Gary Kendall, director of CDO2, in a 2023 article by Revolution.aero. CDO2 has developed new technology for imaging current flow in batteries. “If you’re going to put a lithium-ion battery in an airframe you need to put it into a fireproof box. The problem is that makes the battery heavy. What we have done is try to meet that regulation with as smaller weight overhead as possible by using composite boxes rather than metal, for example.”
The European Union Aviation Safety Agency (EASA) certified Pipistrel’s Velis Electro eVTOL in 2020 as a light sport aircraft (LSA) under SC-ELA.2015-01 (CRI F-101) and proposed the MOC-3 SC-VTOL battery regulations in 2023 (see Revolution.aero news). Meanwhile, the Federal Aviation Administration (FAA) is still trying to develop its battery regulations for eVTOLs.
Peel-and-stick thermal protection for aircraft batteries
Lilium will use Blueshift Materials’ AeroZero TPS films as thermal protection in its battery systems. Source | Blueshift Materials
Notably, eVTOL manufacturer Lilium (Munich, Germany) has selected Blueshift Materials (Spencer, Mass., U.S.) to supply thermal protection (TPS) for its initial series of eVTOL production aircraft. Blueshift’s AeroZero TPS will be used in Lilium’s carbon fiber composite battery design to help prevent burn through and mitigate the risk of thermal runaway propagation.
Based on polyimide aerogel, all of Blueshift Materials’ products are flame retardant, <1.5 millimeters thick and have a very low thermal conductivity/diffusivity. Able to operate up to 2400°C, AeroZero TPS products can be co-cured to a structure or made as a peel-and-stick film. “Blueshift’s thermal protection system is light, thin and easy to incorporate into our strict design requirements, while producing exceptional thermal results,” says Martin Schuebel, Lilium’s senior VP procurement.
New resins for lightweight fire and thermal protection
“The automotive industry sees a need for new material solutions for battery components with superior flame retardancy compared to conventional thermoset prepregs and aluminum,” says Stefano Montani, transportation marketing manager at Syensqo (Heanor, U.K.), previously Solvay Composites. This performance allows passengers sufficient time to escape time in the event of a thermal runaway, he explains. “Structural battery housing solutions must also ensure reliable EMI [electromagnetic] shielding performance and enable efficient processing of large volumes at high production rates,” he adds. In October 2023, Syensqo launched SolvaLite 716 FR, a fast-curing epoxy prepreg designed for a wide range of structural parts and reinforcements in battery electric vehicles (BEVs). The new prepreg offers a rapid press cure time of 8 minutes at 150°C, designed to help converters achieve more efficient production, such as when using Solvay’s proprietary double diaphragm forming (DDF) technology.
Another 2023 launch is AOC’s (Collierville, Tenn., U.S.) Firepel R003 Resin Series for EV battery enclosures. It provides advanced mechanical and thermal performance compared to traditional polyester resins while also meeting the requirements of UL2596 for EV battery enclosure materials. Firepel R003 resins are designed for use in liquid molding processes such as vacuum infusion, resin transfer molding (RTM) and wet molding for the manufacture of high-performance composite parts.
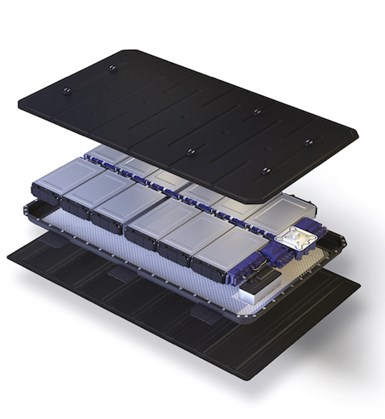
HPU battery. Source | Huntsman
In March 2024, Huntsman (Frankfurt, Germany) announced a portfolio of novel polyurethane- and epoxy-based resins for EV applications. These customizable, quick-cure, high-strength polyurethane resins include Vitrox and RimLine systems for underbody and upper cover battery protection applications up to 30% quicker than some existing technologies. The systems include products that can offer lower overall part weight and increased strength as well as improved structural performance. The RimLine RSM system is a glass fiber-reinforced polyurethane composite and is applied via reaction spray molding, which can be demolded quickly for an efficient production cycle. Huntsman also noted its range of intrinsic fire-retardant Araldite FST and unfilled mass production systems for WCM, RTM and HP-RTM processes that can enable short cycle times with low scrap rates.
Underbody panel using bio-inspired Helicoid technology
Automated high-pressure resin transfer molding (HP-RTM)/liquid composites molding (LCM) demonstration line. Source | TPI Composites, Helicoid Industries
Announced in May 2023, TPI Composites Inc. (Scottsdale, Ariz., U.S.) and Helicoid Industries (Indio, Calif., U.S.) collaborated to produce a bio-inspired underbody protection panel using Helicoid technology. The composite structure leverages digital engineering, unconventional layup scenarios, biomimicry, advanced multiaxial intelligent weaving and automated manufacturing to protect high-voltage battery packs from road debris compared to current aluminum designs. Developed in a manufacturing cell at TPI’s Automotive Technology Center in Warren, Rhode Island, using the latest in automated ply cutting and robotic pick-and-place technologies, the process is said to be a seamless and cost-effective implementation of Helicoid architectures. A multiaxial noncrimp fabric (NCF) technology is used to strategically compose the full Helicoid stack in subunits. The stack layers are then robotically dosed and automatically placed and retrieved from a 2,500-ton press, resulting in high-performance precision parts.
Thermoplastic composite materials for battery enclosures
Interest in using thermoplastic composites for battery components is growing as well. “From a materials perspective, the use of thermoplastic composites enables the structural components of batteries, when they reach the end of their service life, to have a higher recyclability percentage compared to conventional systems,” says Guillermo Ulldemolins, a researcher in sustainable and future mobility at Aimplas (Valencia, Spain). He notes this contributes to the circularity of the sector, making it more sustainable and environmentally conscious. In March 2024, Aimplas (Valecia, Spain) announced the launch of Lofith Composites, a new technology company focused on developing long fiber-reinforced thermoplastic (LFTP) composites. Aimplas is one partner in the multi-company MODALT project, which aims to generate knowledge to develop and manufacture more sustainable, lighter, safer and long-lasting batteries. “The storage module we are developing will contribute to unlocking high-performance electrified vehicle applications,” says program technical leader Danile Fons.
Even following exposure to particle bombardment and temperatures in tests as high as 1400°C, this Tepex test specimen did not undergo burn through. Source | Envalior
Envalior (Düsseldorf, Germany), a new company formed by DSM Engineering Materials (DEM) and Lanxess’ High Performance Materials (HPM) unit, is offering a new composite material under the Tepex brand that, even with low test specimen thicknesses, passes the standard thermal runaway tests for EV battery housings. Its high resistance to the extreme conditions of a battery cell fire can be attributed to its long and continuous non-flammable fibers that reinforce the material in a multilayer structure. “Above all, it’s thanks to the fibers that our structural material is capable of withstanding the extreme pressures, temperatures well in excess of 1000°C, and bombardment by abrasive hot particles that occur during the thermal runaway of battery cells,” says Dr. Dirk Bonefeld, head of Tepex product management. He notes the material is also ideal for components inside the battery such as the cell housing, holder and partitions.
In July 2023, SABIC (Riyadh, Saudi Arabia, and Houston, Texas, U.S.) launched its SABIC PP compound H1090 and Stamax 30YH611 resins. The 30% glass fiber-reinforced polypropylene resins are intumescent and flame-retardant (FR). Well-suited for compression and injection molding, they enable large, complex composite structural parts for EV battery pack components such as top covers, enclosures and module separators. Both grades offer optimized thermal barrier properties to help delay or contain thermal runaway propagation.
Solvay (Alpharetta, Ga., U.S.) also introduced a new family of long glass fiber (LGF) composites through its Xencor Xtreme LGF polyphthalamide (PPA) solutions for battery applications. Xencor XTreme PPA LGF materials are designed to offer resistance to direct flame exposure at 1000°C for more than 10 minutes and also to retain a high level of electrical insulation after exposure to flame, helping to mitigate thermal runaway. The materials also have a high glass transition temperature to maintain dimensional stability of parts under battery operating conditions.
Pentatonic thermoplastic composite-metal hybrid skid plate protector
In February 2023, Kautex Textron GmbH & Co. KG (Kautex, Bonn, Germany) announced a first order from an automotive OEM for a fiber-reinforced thermoplastic composite underbody battery protection skid plate. The skid plate is part of the company’s new Pentatonic battery system product line supporting battery electric vehicle (BEV) production. The new skid plate design will be produced for on-and-off-road applications, Kautex says. It is designed to meet impact requirements and features more than a 50% weight reduction versus its steel counterpart.
Composites inside the battery
Technology concept for the 3D continuous fiber printed, free-form, structure-supporting PRINTCAP supercaps. Source | RCCF at TU Dresden
The “Next Generation of 3D Printed Structural Supercapacitors” (PRINTCAP) research project (June 2022 to March 2025) aims to develop a new generation of supercapacitors (SC) for fast-charging, structural energy storage in automotive and aerospace EVs through the incorporation of 3D printing and multifunctional composites. Current energy storage systems are made of layers and stacking methods, which require shielding housings which often take up valuable installation space. Innovative structural supercapacitors (SSC), however, combine the energy storage function of SC with the high mechanical properties of lightweight composites — addressing weight reduction and opening up space. PRINTCAP aims to develop a near-neat shape SSC concept that combine weight- and space-optimized lightweight structures with the energy storage function. The developed concepts will also include initial solutions for recycling the materials used, as well as life cycle analysis (LCA) studies, in accordance with the cradle-to-cradle principle.
In January 2024, researchers at the Oak Ridge National Laboratory’s (ORNL, Oak Ridge, Tenn., U.S.) Department of Energy announced they developed a lighter, metal-free current collector made from carbon fiber-reinforced polymer (CFRP). A current collector is a component that often adds 10% to the weight of a battery cell without contributing energy. The aligned carbon fibers in ORNL’s new development work together with a thin film of carbon nanotubes (CNTs) to enhance directional and uniform current flow. Conventional current collectors include aluminum foil for cathode and copper foil for anode. Alternatively, development of current collectors made of assembled metal or carbon nanostructures such as metal, graphene, CNT or carbon fiber foams, and other similar structures, have shown potential, particularly carbon fiber and CNTs. “We are reducing 80% to 90% of the weight of the current collector,” says Jaswinder Sharma, ORNL researcher in this project. “This will help a lot in increasing the energy density of battery packs.” For more information, read the ORNL research paper, “A lightweight and metal-free current collector for battery anode applications.”
Graphene in batteries
This section is taken from the report “Graphene for Battery Applications” developed for CW by the Graphene Council (New Bern, N.C., U.S.).
A nanomaterial that is made from pure carbon, graphene is often described as a two-dimensional (2D) material because it is only a few atoms thick and thus, almost entirely surface area. Because it comes in many forms and types, graphene can be considered a “family” of materials including graphene oxide, reduced graphene oxide, graphene sheets, graphene flakes and other versions.
Graphene can be used as an additive for lead-acid batteries and in the anodes, cathodes and electrolytes for the following battery chemistries:
- Lithium-ion (Li-ion)
- Lithium-Sulfur (Li-S)
- Metal-air
- Sodium-ion (Na-ion)
- Aluminum-ion (Al-ion)
- Solid-state
Lead-acid batteries. Using graphene as an alternative to carbon black in lead-acid batteries has been very successful commercially to improve conductivity and reduce sulfation. By adding small amounts of reduced graphene oxide, lead-acid batteries have reached new performance levels:
- 60-70% improved cycling life
- 60-70% improved dynamic charge acceptance
- 50% reduced water loss
- 200-250% increased lifetime.
In collaboration with what is said to be the largest battery manufacturer in Sri Lanka, Ceylon Graphene (Homogama, Sri Lanka) introduced the world’s first graphene-enhanced lead-acid battery in 2022, which reportedly provides 15-25% increased capacity, 30-35% increased charge and 50% lower water loss, enhancing performance and lifecycle.
Li-ion batteries. Graphene improves the chemistries of both the cathodes and anodes of Li-ion batteries so that they hold more charge and do so over more cycles. For anodes, graphene can be used as an additive in graphite or as a surface coating. For Li-ion batteries, graphene-enabled nanostructured-silicon anodes have been developed that enable silicon to survive more cycles and store more energy.
While graphene-enabled silicon (Si) anodes cost more per kilogram than those coated with spherical graphite, the boost to capacity potentially lowers the cost per kilowatt-hour (kWh). Graphene-based anodes are reportedly capable of enabling Li-ion batteries to achieve $80 per kWh. It has long been suggested that lithium nickel manganese cobalt (NCM) cathodes paired with Si-dominant anodes will increase energy density by up to 50%, reducing $/kWh cost by 30-40%.
Graphene can also be used in cathodes. When high battery performance is required, the electrical conductivity of the most common Li-ion batteries is fairly low, so electron conducting additives are frequently added. Graphene has been used in the matrix of a cathode material to significantly improve cathode electrochemical performance, and thus transmission and diffusion of electrons and ions. Graphene as a composite hybrid containing metallic material can also be used in a cathode. Graphene has been used as a support material in electrodes to keep metal ions in the required order to improve efficiency. When used as a composite in electrodes, graphene facilitates fast charging as a result of its high conductivity and well-ordered structure.
Talga (West Perth, Australia) is now marketing a Si-carbon composite (30-50% Si) for use as an energy-boosting additive to existing commercial battery anodes. The drop-in design uses Talga’s proprietary graphene, Si and graphite technology to enable low swelling and commercial production calendaring pressures in a lower cost and highly scalable manufacturing process. Meanwhile, Nanotech Energy (Chico, Calif., U.S.) is marketing a non-flammable Li-ion battery using graphene, limiting flame or explosion risk for a safer battery solution.
Li-S batteries. These batteries are low cost, less toxic and possess an energy density more than five times that of Li-ion batteries. They have a realistic potential to replace Li-ion batteries in commercial applications, especially in standalone energy storage systems. Because of these factors, Li-S batteries have received a lot of interest from industry and research institutes. Graphene materials have been widely explored for applications in sulfur cathodes, interlayers and Li anodes.
Graphene has been used for Li−S batteries as a cathode complement because its high electrical conductivity compensates for the insulating nature of sulfur, while its hardness and compliance provide resistance to mechanical stress from sulfur expansion during the discharge process. Graphene is being used in a large scale and highly capitalized commercial effort to enable the following features for Li-S batteries:
- No nickel, cobalt, manganese or graphite required
- Lower bill of materials
- Twice as much energy density as other Li-S batteries
- Up to 60% weight reduction for a typical EV battery pack
- Resistance to overcharge and thermal runaway.
Lyten (San Jose, Calif., U.S.) is the pioneer of the Lyten 3D Graphene applications platform. The company’s decarbonization supermaterials are being tuned for a wide range of applications, including next-gen Li-S batteries for use in automotive, aerospace and defense market, among others.
Metal-air batteries. Metal–air batteries are based on the electrochemical coupling of a reactive anode to a cathode open to oxygen in the air as the cathode‐active material. In principle, this provides a battery with inexhaustible cathode reactant and, in some cases, a very high specific energy. Metal–air batteries show great potential to meet the growing energy demand for EVs and smart power grids. However, despite significant progress already achieved, challenges still remain in developing a practical metal–air battery with performance exceeding existing Li-ion batteries.
Graphene nanosheets (GNS) have been demonstrated as a desirable cathode material in Li–air batteries. Benefits include a high electrocatalytic activity superior to that of acetylene carbon black, ease of obtaining freestanding 2D or 3D films with high porosity for oxygen diffusion and very high surface area. Graphene Manufacturing Group (Richlands, Australia) has developed graphene aluminum-ion battery technology that has high energy densities and higher power densities versus current leading Li-ion battery technology, enabling up to three times longer battery life and up to 70 times faster charging.
OCSiAl scales graphene for battery applications
Graphene nanotubes manufacturer OCSiAl (Luxembourg) will begin production in its new facility near Belgrade, Serbia in 2024. The nanotube synthesis plant will have an initial capacity of 60 tonnes/year, increasing to 120 tonnes/year by 2026. In addition to synthesizing nanotubes, the facility will manufacture nanotube suspensions for lithium-ion battery manufacturers in Europe, the U.S. and Asia — enough to enhance the performance of more than one million electric cars with an average battery capacity of 75 kWh per car. According to the company, its nanotubes create improve key battery characteristics, including cycle life, lower DCR, C-rate performance and cohesion between active battery material particles, making the battery electrodes more durable. Graphene nanotubes unlock new battery technologies, including high-silicon content anodes, thick LFP cathodes, fast-charging graphite anodes and can be applied in solid-state batteries.
Fuel cells
Fuel cells use hydrogen (H2) as a fuel, combined with oxygen, to generate electricity through an electrochemical reaction, not combustion, producing only heat and water as outputs, and thus, are zero-emission power sources.
Components of a fuel cell and stack. Source |Slide 5, “Development of book of attributes for PEM fuel cell components” by Xiao-Zi (Riny) Yuan, workshop for NREL, May 5-6, 2021.
Fuel cells comprise a stack of cells sandwiched between end plates, which are typically metal. Within each cell are multiple components that can use carbon fiber, including bipolar plates, gas diffusion layers (GDL) and membrane electrode assemblies (MEA):
- Bipolar plates. Mass-produced applications typically use metal, but polymer-carbon composites can also be used, comprising thermoset or thermoplastic polymer binder mixed with one or more carbon-based fillers: graphite, carbon black, carbon fibers, graphene, carbon nanotubes (CNTs), etc.
- GDL are made from graphitized carbon fiber-based nonwovens called carbon sheets, plates or paper (CP).
- MEA are multilayer assemblies that contain GDL as well as a proton-conducting polymer electrolyte membrane and a catalyst layer — this catalyst-coated membrane (CCM) can use a carbon fiber support for the catalyst layer.
The number of unit cells in a fuel cell stack varies according to the power produced, application and technology used. For example, Nedstack (Arnhem, Netherlands) uses 48 cells to deliver 6.8 kilowatts of electrical power in its FCS 7-XXL PEM fuel cell, while Bosch SOFC (Stuttgart, Germany) uses 400 cells in its 120-kilowatt solid oxide fuel cell.
Fuel cell shipments by type 2018-2022 (1,000 units). Source | Fuel Cell Industry Review 2022 by ERM
There are multiple fuel cell types based on the six main electrolytes used: proton exchange membrane fuel cells (PEMFC), direct methanol fuel cells (DMFC), phosphoric acid fuel cells (PAFC), molten carbonate fuel cells (MCFC), solid oxide fuel cells (SOFC) and alkaline fuel cells (AFC). The two types that dominate both megawatts and units shipped are PEMFC, used mainly for transport applications, and SOFC used for portable and stationary applications.
Growing market
Fuel cell shipments (1,000 units) by application 2018-2022. Source | “Fuel Cell Industry Review 2022” by ERM
According to the “Fuel Cell Industry Review 2022” — the latest annual survey published by ERM (London, U.K.) in early 2024 — fuel cell shipments from 2021 to 2022 grew from 86,000 to 89,200 units and from ≈2.3 gigawatts (GW) to just under 2.5 GW, with a CAGR of around 25% since 2018.
Fuel cell shipments (MW) by application 2018-2022. Source | “Fuel Cell Industry Review 2022” by ERM
The most units were sold into stationary applications while 85% of megawatts (MW) were sold into transport, most of these for passenger cars (15,000 units) nearly all made by Hyundai and Toyota. China led in trucks and buses, shipping nearly 3,800 fuel cells, while fewer than 400 fuel cells for commercial vehicles went to Europe and North America combined. Shipments for fuel cell electric vehicles (FCEVs) are expected to continue in China as it pushes to meet its goal of 50,000 FCEVs in operation by 2025.
The 2.5 GW reported by the “Fuel Cell Industry Review” is only 17% of the 15 GW of global manufacturing capacity indicated by fuel cell OEMs as reported in the “Hydrogen Insights 2023” update (December 2023). That production capacity is housed mainly in South Korea, China and Japan. The “Fuel Cell Industry Review” reports that Asia is also the leading region for fuel cell adoption and use.
H2Motive range of compact, high-performance fuel cells for zero-emission H2 mobility. Source | Symbio
Symbio (Saint-Fons, France) is a zero-emission H2 mobility joint venture between Forvia, Michelin and Stellantis. In December 2023, the company inaugurated its SymphonHy gigafactory for fuel cells, ramping production from 16,000 to 50,000 units/year by 2026. Fuel cells supplied to Stellantis will extend its H2 FCEVs beyond already available mid-size vans in Europe to large-size vans, Ram pickups and heavy-duty trucks in North American. In February 2024, Symbio signed an MOU with Kawasaki Heavy Industries to apply fuel cell systems to construction equipment.
EKPO (Dettingen/Erms, Germany) is the joint venture between ElringKlinger and Plastic Omnium (now OPmobility) to produce fuel cells with an initial capacity of 10,000 units/year at its headquarters. The company has also formed a subsidiary in the city of Suzhou, west of Shanghai to supply the Chinese market. Announcements made in 2023 include supply to a European car OEM for a production vehicle, an NM12 Single PEMFC stack module with 359 cells for a single cruise ship operated by a global cruise line, a contract with H-TEC Systems for PEM electrolyzers and a contract with China FAW Group to deliver fuel cells for its premium brand Hongqi.
Accelera (Columbus, Ind., U.S.) is the zero-emission mobility business of engine manufacturer Cummins (Columbus, Ind., U.S.). In May 2023, it started electrolyzer production at its plant in Fridley, Minnesota, with annual production capacity of 500 MW scaling to 1 GW in the future. It also noted 300 MW of electrolyzer projects in North America including: 90 MW for Varennes Carbon Recycling in Quebec, 20 MW for Gevo/Zero6 Energy in North Dakota, 35 MW with Linde in New York, 20 MW with Atura Power in Ohio and a fleet of 1,000 electric school buses with Blue Bird in the U.S.
In January 2024, GM and Honda announced their joint venture Fuel Cell System Manufacturing LLC (FCSM) began production at the 70,000-square-foot facility in Brownstown, Mich., U.S. with plans to produce 2,000-3,000 fuel cells/year by 2025. Honda will reportedly take 2,000 modules — 25% of which will go into the Honda CR-V plug-in hybrid which replaces an internal-combustion engine with a fuel cell. Honda plans to generate demand for up to 60,000 fuel cell systems per year by 2030 for applications beyond cars.
Toray boosts carbon fiber production for fuel cells
Carbon fiber supplier Toray (Tokyo, Japan) announced that it is developing a range of materials for production, transport, storage and use of hydrogen (H2) as a fuel. These materials include CCM which traditionally has used a carbon fiber support for the catalyst layer due to its high strength and low weight. CCMs are also used in electrolyzers for green H2 production. The “Hydrogen Insights 2023” update reported electrolyzer manufacturing capacity has increased from 9 to 11 GW according to OEM statements.
Toray announced on March 17, 2023 that it would triple CCM production capacity at its subsidiary Greenerity (Alzenau, Bavaria, Germany), adding a third factory and expanding capacity at the second factory. Through Grennerity, Toray also produces MEA for fuel cells used in FCEVs including buses, trucks, commercial vehicles and passenger cars. At full capacity, Greenerity’s second plant will support annual production of more than 10,000 FCEVs. Toray says that it has positioned materials for H2 and fuel cell production and use as important for future growth and will extensively allocate resources to expand this business.
Glass fiber PCBs to reduce fuel cell cost
Bramble Energy (Crawley, U.K.) has developed technology to reduce cost by making its fuel cell stacks out of printed circuit boards (PCBs). As explained in a February 2024 The Engineer article and in Bramble’s white paper “System Architecture Advantages of the PCBFC,” this approach allows fuel cells to be made at any PCB factory worldwide, using the same materials and processes used for standard PCB manufacture — namely, machined FR4 glass fiber-reinforced epoxy resin laminate. The company’s model is to license its technology to PCB manufacturers who already supply most of the large automotive OEMs. By tapping into this huge, high-volume global manufacturing base, Bramble Energy believes its technology can cut cost to as little as $60/kW — more than 10 times cheaper than current technologies.
Related Content
On the radar: Cryogenic testing of composites for future hydrogen storage
Netherlands, U.K., France, Germany and the U.S. build up test capability, look at thermoset and thermoplastic composite materials.
Read MoreJEC World 2022, Part 1: Highlights in sustainable, digital, industrialized composites
JEC World 2022 offered numerous new developments in composites materials, processes and applications, according to CW senior editor, Ginger Gardiner, most targeting improved sustainability for wider applications.
Read MoreU.K. team successfully recycles reclaimed continuous carbon fibers from pressure tanks
The U.K.’s NCC with partners B&M Longworth and Cygnet Texkimp achieve continuous carbon fiber recovery in a significant first step to deliver sustainable composite pressure vessels for the hydrogen market.
Read MoreHexagon Purus Westminster: Experience, growth, new developments in hydrogen storage
Hexagon Purus scales production of Type 4 composite tanks, discusses growth, recyclability, sensors and carbon fiber supply and sustainability.
Read MoreRead Next
Composites end markets: Energy (2024)
Composites are used widely in oil/gas, wind and other renewable energy applications. Despite market challenges, growth potential and innovation for composites continue.
Read MoreCW’s 2024 Top Shops survey offers new approach to benchmarking
Respondents that complete the survey by April 30, 2024, have the chance to be recognized as an honoree.
Read MoreFrom the CW Archives: The tale of the thermoplastic cryotank
In 2006, guest columnist Bob Hartunian related the story of his efforts two decades prior, while at McDonnell Douglas, to develop a thermoplastic composite crytank for hydrogen storage. He learned a lot of lessons.
Read More