UMaine’s novel polymer 3D printer surpasses former Guinness World Record
Four times larger than its 2019 predecessor, Factory of the Future 1.0 offers new opportunities in composite materials, including development of recycled and bio-based materials, opening up new research frontiers.
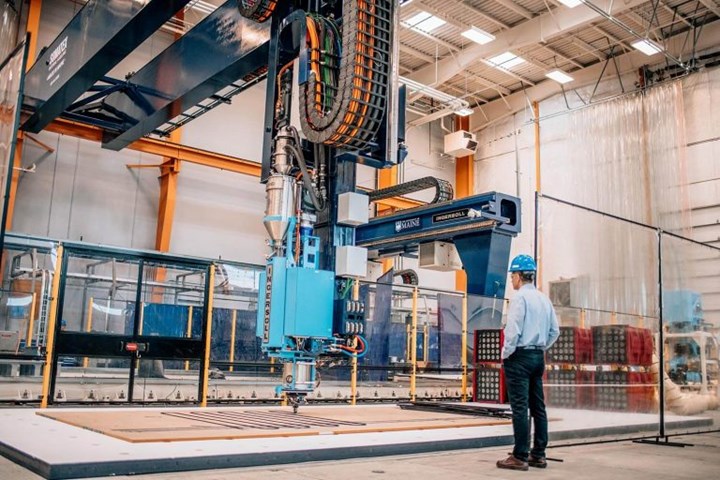
Factory of the Future 1.0. Source | UMaine
Surpassing its own 2019 Guinness World Record for the largest polymer 3D printer, the University of Maine (UMaine, Orono, U.S.) announces the development of a next-generation printer that is four times larger than its predecessor to catalyze the future of sustainable manufacturing in a number of industries.
The new printer, dubbed Factory of the Future 1.0 (FoF 1.0), was unveiled at UMaine’s Advanced Structures and Composites Center (ASCC) on April 23 to an audience that included representatives from the U.S. Department of Defense (DOE), U.S. Department of Energy (DOE), the Maine State Housing Authority, industry partners and other stakeholders who plan to use this technology. The thermoplastic polymer printer is designed to print objects as large as 96 feet long × 32 feet wide × 18 feet high, and can print up to 500 pounds per hour. It offers new opportunities for eco-friendly and cost-effective manufacturing for numerous industries, including national security, affordable housing, bridge construction, ocean and wind energy technologies, and maritime vessel fabrication. The design and fabrication of this printer and hybrid manufacturing system was made possible with support from the Office of the Secretary of Defense through the U.S. Army Corps of Engineers.
The printer will advance various initiatives, including the development of bio-based feedstocks from wood residuals abundant in Maine.
According to UMaine, FoF 1.0 isn’t merely a large-scale printer; it dynamically switches between various processes such as large-scale additive manufacturing (LSAM), subtractive manufacturing, continuous tape layup and robotic arm operations. Access to it and MasterPrint, the ASCC’s first world-record breaking 3D printer, will streamline manufacturing innovation research at the center. The two large printers can collaborate by sharing the same end-effectors or by working on the same part.
“UMaine and the ASCC possess the innovation, capacity and workforce to support the future needs of the DOD in advanced manufacturing,” says U.S. Senator Susan Collins. Since fiscal year 2022, Senator Collins, vice chair of the Senate Appropriations Committee and Subcommittee on Defense, has secured more than $93 million in support of this initiative and other defense projects at the ASCC.
ASCC executive director Habib Dagher adds that FoF 1.0 opens up “new research frontiers to integrate these collaborative robotics operations at a very large scale with new sensors, high-performance computing and artificial intelligence to create born-certified systems that meet high-quality standards.”
The printer will advance various initiatives, including the development of bio-based feedstocks from wood residuals abundant in Maine. This technology will advance commercialization efforts such as BioHome3D and the creation of sustainable, affordable housing, while also propelling technological advancements for national security, particularly in lightweight, rapidly deployable structures and vessel technologies. These capabilities will help reaffirm “our standing as leaders in composite materials research and advanced manufacturing,” UMaine President Joan Ferrini-Mundy adds.
The FoF 1.0 unveiling comes ahead of this summer’s planned groundbreaking of a new 47,000-square-foot research laboratory called the Green Engineering and Materials (GEM) Factory of the Future. Scheduled for August 2024, the facility is positioned to enhance manufacturing innovation across multiple sectors. Its primary aim is to facilitate and scale up more sustainable manufacturing practices by introducing next-generation solutions and biomaterials, addressing challenges such as a diminishing workforce and strained supply chains with local solutions.
It will also explore novel material systems by prioritizing recycled and bio-based materials. Maine, claimed to be the most forested state in the nation, annually produces more than one million tons of wood residuals in its sawmills, which can be used as feedstock for 3D printing. In addition, UMaine, with the GEM initiative, has prioritized manufacturing workforce development by offering experiential learning and entrepreneurial training programs aimed at nurturing the next generation of leaders.
In tandem with R&D, the GEM Factory of the Future aligns with the formation of the Maine College of Engineering and Computing (MCEC), a statewide initiative funded by the Harold Alfond Foundation as part of UMS TRANSFORMS that prioritizes developing a workforce prepared for the increasingly interconnected and digital global economy.
Related Content
Price, performance, protection: EV battery enclosures, Part 1
Composite technologies are growing in use as suppliers continue efforts to meet more demanding requirements for EV battery enclosures.
Read MoreLarge-format 3D printing enables toolless, rapid production for AUVs
Dive Technologies started by 3D printing prototypes of its composite autonomous underwater vehicles, but AM became the solution for customizable, toolless production.
Read MorePlant tour: Albany Engineered Composites, Rochester, N.H., U.S.
Efficient, high-quality, well-controlled composites manufacturing at volume is the mantra for this 3D weaving specialist.
Read MoreNovel dry tape for liquid molded composites
MTorres seeks to enable next-gen aircraft and open new markets for composites with low-cost, high-permeability tapes and versatile, high-speed production lines.
Read MoreRead Next
UMaine researchers aim to recycle wind turbine blades as 3D printing material
With a DOE grant in hand, UMaine’s ASCC seeks to develop an approach to recycle shredded wind turbine blade material as a cost-effective reinforcement and filler for large-scale 3D printing.
Read MoreAnisoprint moves to China, scales up continuous fiber 3D printer production
With new headquarters in Shanghai, and a shift in management roles, Anisoprint is looking forward to rapid growth in Chinese, European and U.S. markets, further aided by funding rounds.
Read MoreAl Seer Marine, Abu Dhabi Maritime unveil world’s largest 3D-printed boat
Holding the new Guinness World Record at 11.98 meters, the 3D-printed composite water taxi used a CEAD Flexbot to print two hulls in less than 12 days.
Read More