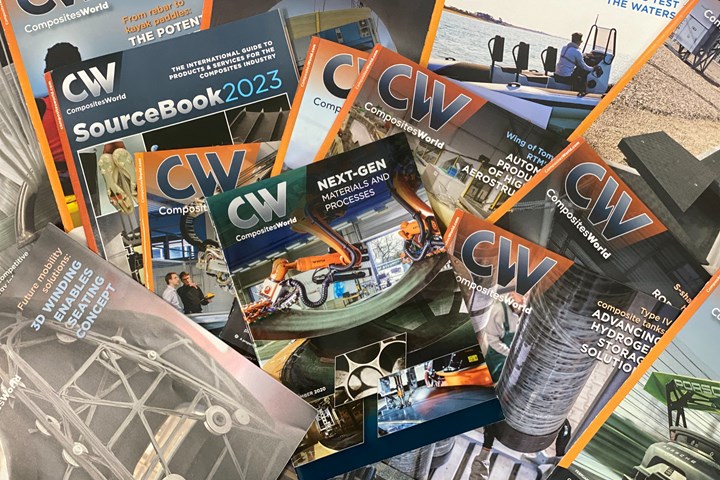
This year, CompositesWorld celebrates 30 years serving the composites industry. Photo Credit: CW
How long have you been reading CompositesWorld? This year, CW celebrates its 30th anniversary — three exciting decades of reporting on technologies, innovations, consumer trends and business conditions surrounding the composites industry. The CW brand, which originally encompassed two bimonthly magazines (High-Performance Composites and Composites Technology), originated in 1993. CW was acquired by Gardner Business Media (then Gardner Publications) in 2007 and the two magazines were combined into the CW magazine you know today. For 30 years, CW has brought its audience the latest industry news and product announcements, technical articles providing insights into technology and process innovations, as well as tours of composite manufacturing facilities and much more.
The number “30” has some additional significance for the composites community as it was during the 1930s that the modern composites industry as we know it got its start. During this time, research was underway that produced new synthetic polymers including unsaturated polyester resins (UPRs) that would come to be used widely in the composites industry, and glass companies were experimenting with weaving glass fibers into new kinds of textiles.
As CW celebrates 30 years, we thought it would be fun to reflect on the history of composites and some of the stories the magazine has told during this time. Our first installment of this two-part retrospective covers the beginnings and rapid rise of what is still a relatively young industry. Links have been provided beneath each decade, corresponding with original CW content on that subject matter, for a more in-depth look.
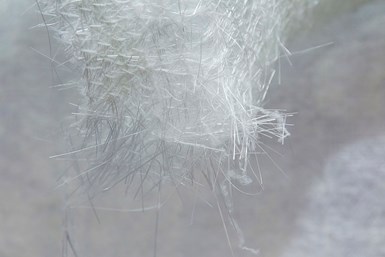
The use of glass fiber as a reinforcement set the stage for a new industry based on fiber-reinforced polymers. Photo Credit: Getty Images
1930s
During the 1930s, glass company Owens-Illinois joined forces with Corning Glass and combined its glass fiber with polyester resin to create a new, strong and lightweight material. In 1935, the companies merged and Owens-Corning launched Fiberglas. The name stuck and “fiberglass” came to be used generically to describe a class of materials also known as glass fiber-reinforced polymers (GFRP).
During the same time period, R&D of synthetic polymers was yielding several technologies that would find widespread use in the manufacture of composite materials. In 1932, DuPont launched the first polyamide thermoplastic polymer, nylon 6-6, and then in 1936 was awarded a patent for UPR. In 1938, the first patent for epoxy resins was awarded to P. Castan and S. Greenlee.
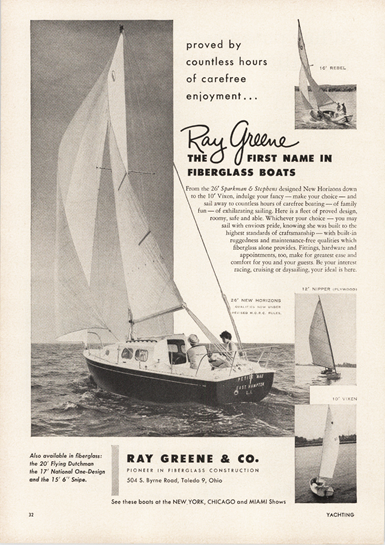
The first fiberglass sailboat was designed and built by Ray Greene in 1942. Photo Credit: Ray Greene & Co.
1940s
The marine industry was a quick adopter of GFRP products. Ray Green, an engineer who had worked for Owens-Illinois Glass Co., made the first fiberglass sailboat in 1942, sparking widespread use of the material in the marine industry that continues to this day.
During World War II, there was a significant need for lightweight and strong materials for military applications. This demand led to further R&D in composites, particularly in the aerospace industry. Scientists and engineers began exploring the use of glass fibers in combination with resin matrices to create composites with enhanced strength-to-weight ratios.
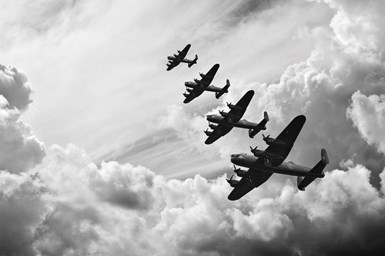
The pace of composites development accelerated during World War II. Photo Credit: Getty Images
During the mid-1940s, Wright-Patterson Air Force Base began conducting experiments building structural aircraft components using composite materials. The first plane featuring a GFRP fuselage was flown at the base in 1944.
The Society of Aircraft Material and Process Engineers was formed in 1944 to address the need for information exchange between engineers working in aerospace development. The society’s name evolved over time to include applications in other industries, eventually becoming the Society for the Advancement of Material and Process Engineering (SAMPE) as we know it today.
With the use of composite materials in military and marine applications growing at an exponential rate, other applications began to emerge. FRP pipe began to be used in industrial applications, and in 1948, the Glastic Corp. developed sheet molding compound (SMC) and bulk molding compound (BMC) materials for use in the automotive industry.
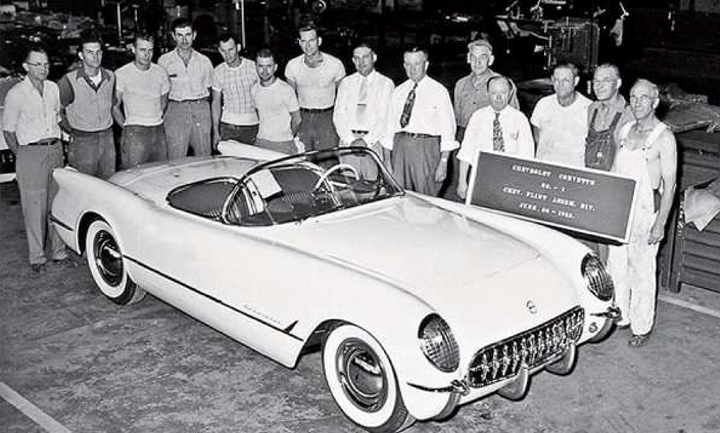
In 1953, Chevrolet produced a Corvette with a body completely constructed of fiberglass-reinforced plastic.
Photo Credit: General Motors
1950s
In the 1950s and 1960s, the composites industry experienced significant growth and technological advancements. The development of new materials, along with improvements in fiber production techniques, allowed for the creation of composites with superior properties.
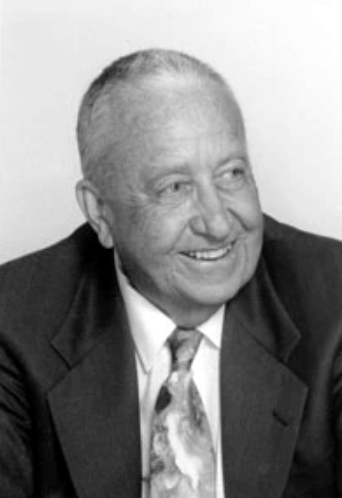
Goldsworthy. Photo Credit: Dawson Services
One of the key figures in the development of composites was American scientist Dr. W. Brandt Goldsworthy, who pioneered the use of cast phenolic resin combined with glass fiber to produce some of the first GFRP molds and tooling in the industry. In 1950, Goldsworthy invented the pultrusion process for composites manufacturing that pulls fibers through a resin bath and then through a heated die. Typical applications include beams and girders used in roof structures, bridges, ladders and frameworks.
In addition to pultrusion, other composite manufacturing processes including vacuum bag molding and large-scale filament winding saw advancement in the 1950s. Filament winding became the basis for rocket motors in missiles and space exploration. Several patents from the 1950s led to what would become resin transfer molding (RTM) — a process that infuses resin into a fiber preform, typically under pressure, in a closed mold to produce a part. RTM has evolved over time into high-pressure RTM (HP-RTM), which is capable of producing fully cured composite parts in just a few minutes.
In 1957, carbon fibers using cotton and rayon were invented, the first appearance of a material that would come to revolutionize the industry.
Polyacrylonitrile (PAN) becomes carbon fiber through a careful manipulation of temperature and tension. Photo Credit: Getty Images
1960s
In 1961, carbon fibers were first manufactured from polyacrylonitrile (PAN). With its exceptional strength and low weight, the material introduced new possibilities for high-performance applications such as aerospace components, Formula 1 cars and sporting equipment like tennis rackets and bicycles.
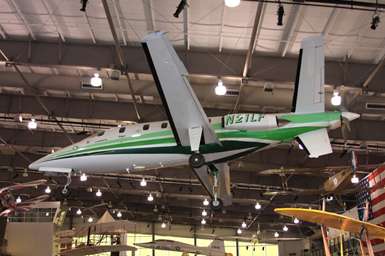
The LearAvia Lear Fan 2100 has been a source of inspiration for many composite airframe designs. Photo Credit: Frontiers of Flight Museum
1970s
During the late 60s and throughout the 70s, ongoing development of new materials and processes led to increased adoption of composites in a wide range of applications. Rigid foams and core materials found their way into building panels and sporting equipment. DuPont introduced Kevlar in the early 70s and such para-aramid fibers began to find use in advanced composites
Fiber-reinforced materials continued to be explored for structural use in aircraft and saw growing interest in experimental (homebuilt or kit) general aviation aircraft during the 70s.
In 1977, the first all-carbon fiber-reinforced epoxy airframe was designed for the Lear Fan, an aircraft that was never certified but paved the way for future composite-intensive airframe designs.
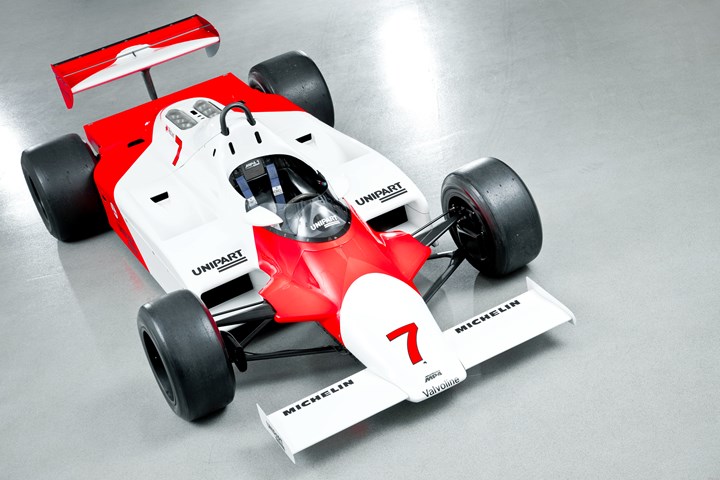
The McLaren MP4/1 featured the first carbon fiber monocoque chassis in Formula 1 racing. Photo Credit: McLaren
1980s
The 1980s saw significant growth in the use of composites for high-performance applications. In 1981, the first carbon fiber monocoque chassis was developed for a McLaren Formula 1 race car.
Composites began to see adoption into commercial airline programs. In 1982, five Boeing 737-200 airliners were placed into service with composite horizontal stabilizers. In 1985, the Airbus A310 featured a carbon fiber vertical stabilizer torque box, and in 1988 the Airbus A320 entered service with a fully composite vertical tail.
In addition, during the 1980s, composites saw increased use in a number of infrastructure developments including the world’s first highway bridge using composites reinforcing tendons and the first all-composites bridge deck.
(Next up) the modern era of composites
Over the years, the composites industry has continued to evolve and expand. Advances in manufacturing processes, including automated layup techniques and resin infusion methods, have improved the efficiency and scalability of composite production. New types of fibers, such as basalt and natural fibers, have also been developed, offering environmentally friendly alternatives to traditional synthetic fibers.
Today, the composites industry is a multi-billion-dollar global market, with applications ranging from aerospace and automotive to wind energy, construction and consumer goods. Ongoing R&D efforts are focused on further enhancing the performance, durability and sustainability of composite materials, opening up even more possibilities for their use in various industries.
In Part 2 of CW’s 30th anniversary retrospective, we’ll dig into our article archives and explore some of the composites industry milestones of the past three decades. Stay tuned.
Related Content
Pultrusion: The basics
A primer describing what pultrusion is, its advantages and disadvantages, and typical applications.
Read MoreThe state of recycled carbon fiber
As the need for carbon fiber rises, can recycling fill the gap?
Read MoreTop 10 Considerations When Buying a CNC Machine for Composites
For a CNC machine to continue to meet or exceed a company’s needs, it must be built and spec’d with these needs in mind.
Read MoreComposites end markets: Aerospace (2023)
With COVID in the past and passengers flying again, commercial aircraft production is ramping up. The aerocomposites supply chain is busy developing new M&P for an approaching next-generation aircraft program.
Read MoreRead Next
The (not exactly) new guy at CW
Former CW writer and editor Scott Francis rejoins the brand as editor-in-chief as Jeff Sloan assumes the role of publisher.
Read MoreUp, not out: The next chapter of CompositesWorld
I have been editor-in-chief of CompositesWorld for 17 years, which translates into a lot of editorials. This will be my last as I become publisher of CW. We welcome Scott Francis back to the brand to take my place.
Read MoreHow composites have become a necessity
Composites used to be one of many material options across industries and applications, but that's not the case anymore.
Read More