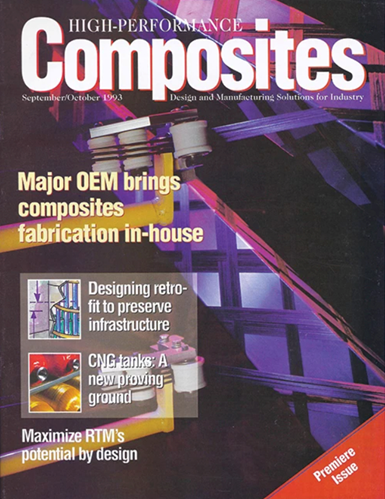
The first issue of High-Performance Composites — one of two magazines that would later merge to become CompositesWorld — was published in September 1993. Photo Credit: CW
This year, CompositesWorld is celebrating its 30th anniversary. The CW brand debuted in 1993, encompassing two bimonthly magazines that served the composites industry (High-Performance Composites and Composites Technology). In 2007, Gardner Business Media acquired the CW brand, and in 2015 the two magazines were combined into the monthly CW magazine you know today. Since its inception, CW has made it its mission to bring readers the latest industry news and product announcements, insightful technical articles, composites manufacturing facility tours and much more.
As part of our 30th anniversary celebration, we continue our look back at some of the composites industry milestones of the last three decades, and highlight some of the relevant stories that CW reported during that time as additional references in the QR Codes provided. Part 1 of our two-part retrospective can be viewed here.
1990s
The 1990s were a time of significant growth and development for composite materials in various applications. R&D efforts were yielding material options with improved durability and higher strength-to-weight ratios, as well as fatigue and corrosion resistance. Increased interest in using composites for lightweighting led automakers to begin exploring composites for applications such as body panels and interior parts.
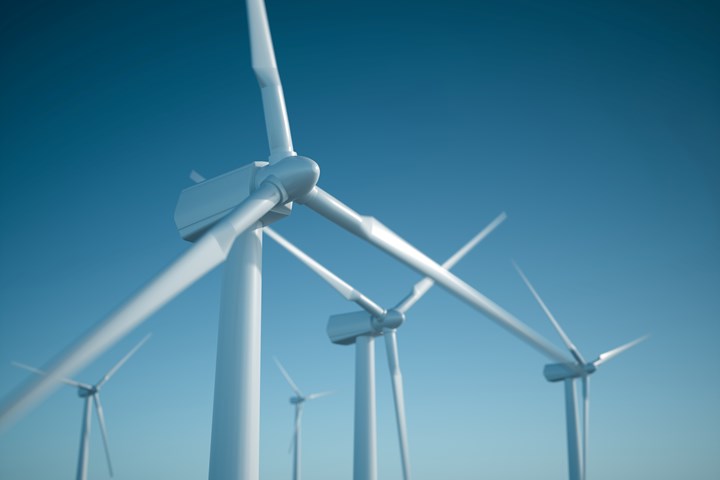
Composite materials have enabled wind blade designs to increase in size. Photo Credit: Thinkstock
During the ‘90s, composites also continued to grow in popularity in sporting goods applications and the marine industry. The wind energy market adopted composites for use in wind turbine blade designs, which were growing in length and required increasingly lighter and stronger materials. Because of their high strength and corrosion resistance, composites also found their way into civil engineering projects such as bridge components, architectural elements and more.
Another big story of this decade was the incredible strides that were taking place regarding composites use in the aerospace sector. In 1995, the Boeing 777 entered service, featuring a significant amount of composite components — the complete tail assembly, including horizontal and vertical stabilizers, elevators and rudder, were all constructed of composite materials.
The 1990s also saw a great deal of innovation in composites manufacturing techniques. This included improvements in automated layup processes, leading to increased production efficiency and lower costs. It was also a time of continued research into new composite materials, including nanocomposites and hybrid materials.
2000s
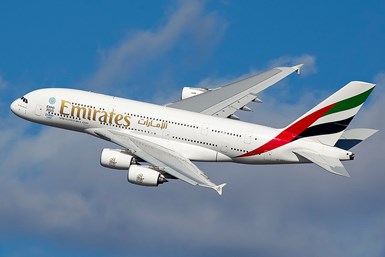
About 22% of the Airbus A380 is made up of composite materials. Photo Credit: Airbus
During the 2000s, the use of composites in commercial aerospace continued to grow. In 2002, the Airbus A340 entered service as the first aircraft to feature thermoplastic composite wing components. Designs for the Airbus A380, the world’s largest passenger plane, were finalized during the early 2000s.
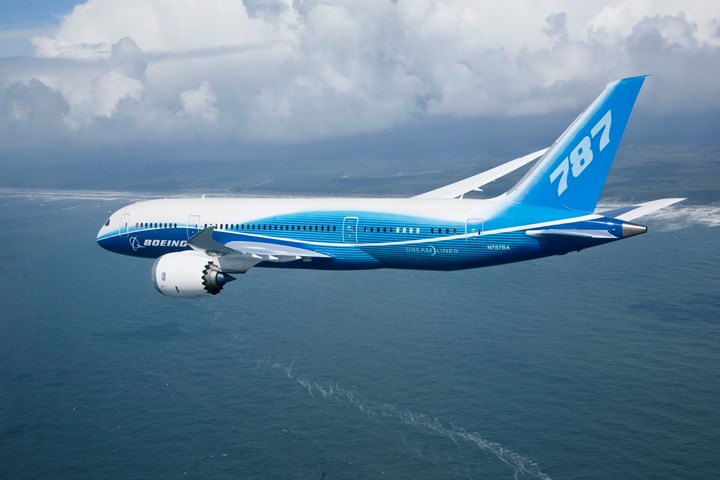
The Boeing 787 Dreamliner is the first airliner to feature an airframe constructed primarily of composite materials. Photo Credit: Boeing
In 2007, Boeing introduced the 787 Dreamliner, an airplane that marked a major milestone for the widespread adoption of composites in commercial aerospace. Composite materials comprised more than 50% of the aircraft’s structural weight.
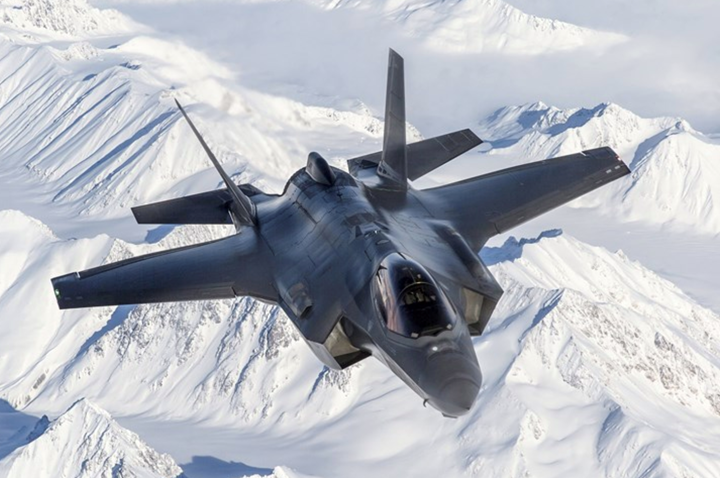
Lockheed Martin’s F-35 Lightning II features an all-composite skin. Photo Credit: Lockheed Martin
Of course, during this time, in addition to commercial airliners, composite materials were finding increasing use in a variety of aircraft programs from business class jets to general aviation to defense.
Meanwhile, the automotive industry continued to explore composites for lightweighting. They found their way into body panel components in various luxury cars and larger production programs such as the Chevrolet Corvette.
2010s
The 2010s saw composites use ramping up in infrastructure due to their durability and corrosion-resistant properties. Composites materials also continued to play a role in renewable energy applications, as originally seen in the 1990s, particularly for lightweighting wind turbine blades made larger for offshore wind farms and more efficient repowering of early onshore farms.
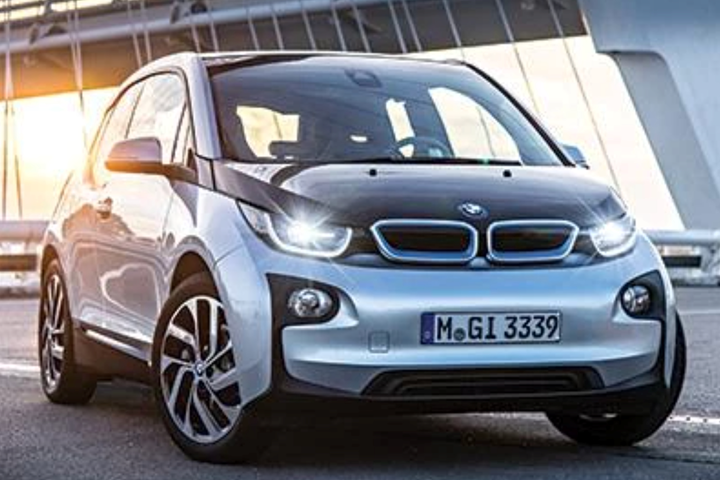
The BMW i3 marked a shift in the use of composites in vehicles, putting more focus on lightweighting for practical purposes. Photo Credit: BMW
As the automotive industry looked to lightweighting as a way to meet stringent fuel efficiency standards, composites found increasing use in mainstream vehicles as opposed to being relegated to luxury and high-performance models.
At the same time, concerns about sustainability and environmental responsibility within all areas of manufacturing were on the rise. Research increased to find new methods for composites recycling and reuse and to recover valuable carbon fibers from composite waste.
By the end of the decade, three of the most most advanced airliners in the world — the Boeing 777X and 787 and the Airbus A350 — were all in production, each using composite materials in unprecedented quantities. The time was ripe for the development of a New Midsize Airplane (NMA), which was expected to use an even larger percentage of advanced materials.
And then in late 2018, the Boeing 737 MAX suffered the first of two fatal crashes that would ground the entire fleet. Ramifications of the 737 MAX disaster rippled through the entire aerospace industry. The disruption was soon amplified by the appearance of a new coronavirus variant.
2020 and beyond
In early 2020, the COVID-19 pandemic quickly spread, and by spring of that year the entire world was in the midst of a medical crisis that touched every aspect of society. Reduced demand for air travel had a ripple effect on the entire aerospace supply chain, disrupting production programs. The pandemic sparked workforce shortages and supply chain breakdowns that plagued all areas of manufacturing. In the face of these challenges, many composites manufacturers and suppliers turned their efforts toward R&D, exploring new advancements in materials, processes, automation and digitalization.
As the global economy continues to recover, the whole of manufacturing will continue to evolve with an increasing focus on sustainable, environmentally conscious materials and processes. We are already seeing this as industry leaders ramp up the introduction of bio-based polymers and fibers and performing lifecycle analysis (LCA) for their products and processes to the development and implementation of equipment to reduce their carbon footprint.
In the last few years, CW has seen trends in other applications as well. These include hydrogen storage, increased adoption of thermoplastics over thermosets — both of which have ties with sustainability initiatives — an enhanced focus on New Space exploration and a rapidly growing subset of aerospace: advanced air mobility. Where these trends will take us still remains to be seen, but it is clear that composites, no matter their application, will continue to be explored not only as replacements for traditional materials, but as material solutions that make emerging technologies possible. CW — and the composites industry as a whole — are already looking ahead to the next 30 years.
Related Content
Mass, cost, durability improvements: EV battery enclosures, Part 2
As interest grows in composite battery covers and trays, composite materials suppliers work to meet current and future needs of automakers, battery module producers.
Read MorePrice, performance, protection: EV battery enclosures, Part 1
Composite technologies are growing in use as suppliers continue efforts to meet more demanding requirements for EV battery enclosures.
Read MoreComposites manufacturing for general aviation aircraft
General aviation, certified and experimental, has increasingly embraced composites over the decades, a path further driven by leveraged innovation in materials and processes and the evolving AAM market.
Read MoreComposites end markets: Aerospace (2023)
With COVID in the past and passengers flying again, commercial aircraft production is ramping up. The aerocomposites supply chain is busy developing new M&P for an approaching next-generation aircraft program.
Read MoreRead Next
Up, not out: The next chapter of CompositesWorld
I have been editor-in-chief of CompositesWorld for 17 years, which translates into a lot of editorials. This will be my last as I become publisher of CW. We welcome Scott Francis back to the brand to take my place.
Read MoreThe (not exactly) new guy at CW
Former CW writer and editor Scott Francis rejoins the brand as editor-in-chief as Jeff Sloan assumes the role of publisher.
Read MoreCelebrating 30 years of CompositesWorld, Part 1
CW explores key composite developments that have shaped how we see and think about the industry today.
Read More