Airborne, Venturi Aviation partner up on composite structures for all-electric aircraft
Cooperation objectives to develop automated manufacturing methods that are more flexible, dynamic and scalable for the Echelon 01’s 2028 launch.
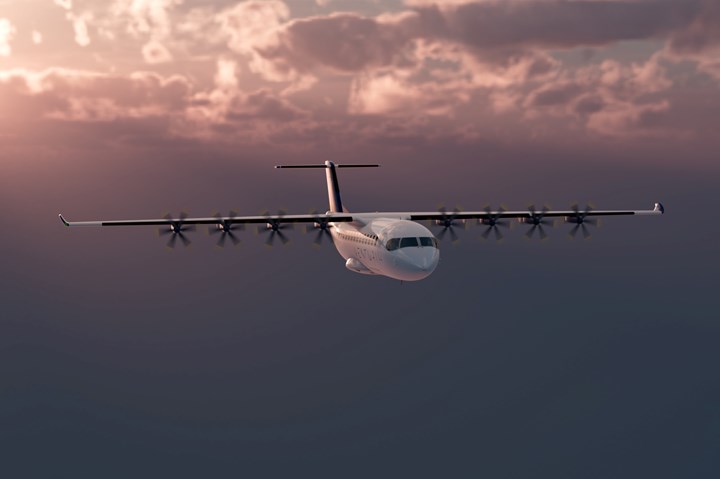
Photo Credit: Airborne, Venturi Aviation
Venturi Aviation (Delft, Netherlands), a Dutch company, developing all-electric aircraft, and Airborne (The Hague, Netherlands), a provider of automated and digital manufacturing solutions for advanced composites, have partnered up for the use of lightweight composite structures for Venturi’s Echelon 01.
The Echelon 01, an all-electric commuter aircraft with a 44-seat capacity and 500-kilometer range that is said to match the needs of regional airliners, is envisioned to be launched in 2028 and will be manufactured in volume production from 2029 onward. Venturi Aviation unveiled the concept’s design in January 2021.
To fully realize the Echelon 01, both companies recognize the crucial importance of lightweighting to enable sufficient range, as well as using manufacturing methods that are more efficient and scalable than traditional aerospace manufacturing processes can deliver.
Under the mutual collaboration, the objective to develop a digital and automated factory for composite lightweight structures that is more flexible, dynamic and based on on-demand manufacturing will be explored. New, low-CAPEX manufacturing processes will also be researched to avoid the investment in large and expensive infrastructure, but rather smaller, cheaper microfactories.
Airborne and Venturi both look forward to exploring the possibilities of this partnership and boosting sustainable aviation.
Related Content
-
Materials & Processes: Composites fibers and resins
Compared to legacy materials like steel, aluminum, iron and titanium, composites are still coming of age, and only just now are being better understood by design and manufacturing engineers. However, composites’ physical properties — combined with unbeatable light weight — make them undeniably attractive.
-
Plant tour: Spirit AeroSystems, Belfast, Northern Ireland, U.K.
Purpose-built facility employs resin transfer infusion (RTI) and assembly technology to manufacture today’s composite A220 wings, and prepares for future new programs and production ramp-ups.
-
Materials & Processes: Resin matrices for composites
The matrix binds the fiber reinforcement, gives the composite component its shape and determines its surface quality. A composite matrix may be a polymer, ceramic, metal or carbon. Here’s a guide to selection.