Cross-sector collaboration. ASCEND aims to build the composites supply chain in the U.K. for both aerospace and automotive industries. Project partners include OEMs, fabricators, researchers and suppliers specializing in digital tools, materials, tooling design and more. Photo Credit: Axillium
Photo credit for image in line with title: McLaren Automotive
In the U.K. and globally, the aerospace composites supply chain is striving to provide potential solutions for aircraft OEMs to produce higher rate, more composites-intensive aircraft components — with new innovations including materials development, new process technologies, novel joining technologies and more.
About three years ago, Craig Carr, technology director for integrated composite structures at GKN Aerospace (Solihull, U.K.) and chair of U.K. industry board the Composites Leadership Forum (CLF), became aware of the highly automated technology that fellow CLF partner McLaren Automotive (Woking, U.K.) was developing to produce high-quality, composite automotive components at its Sheffield-based McLaren Composites Technology Centre (MCTC). The two companies quickly recognized that much could be gained from a cross-sector collaboration.
Joseph Elford, head of engineering at the MCTC, explains that McLaren opened the MCTC in 2018 to develop higher rate composites technologies for the company’s high-performance vehicles — “high-rate” in this case meaning a few thousand parts per year.
“[This] isn’t strictly high-rate in the automotive world, but is high-rate in the composites world, and we’ve always said that we’re probably closer to the aerospace industry than we are to mainstream automotive, in terms of rate and the way we use composites to build complex, integrated parts,” Elford notes.
GKN Aerospace and McLaren “started asking, how can we exploit those technologies between us?” Carr says. “Between the capability of automotive rates, and the requirements of aerospace quality, there should be an answer somewhere in the middle that we can both learn from.”
Springing from these initial conversations, in early 2021 the ASCEND (Aerospace and Automotive Supply Chain Enabled Development) consortium was launched. The £40 million, four-year program is led by GKN Aerospace’s Bristol, U.K.-based Global Technology Centre (GTC), and organized and managed by Axillium Research (Daventry, U.K.). The project is financially supported in part by the U.K. government via Innovate UK and the Aerospace Technology Institute (ATI).
“The main element of the program is developing not just demonstrator parts but a cross-sector and integrated supply chains solution for [the aerospace and automotive] industries, enabling manufacturing of products at higher rates going forward.”
In addition to GKN Aerospace, McLaren Automotive and Axillium, ASCEND includes 13 other U.K.-based project partners that span the supply chain: Assyst Bullmer, Cygnet Texkimp, Far-UK Ltd., Hexcel Composites, Hive Composites, LMAT Ltd., Loop Technology, the National Composites Centre (NCC), Rafinex, Sigmatex, Solvay Composite Materials, Airborne and Des Composites.
ASCEND’s leaders call it a cross-sector technology and supply chain development program, aimed at joining the aerospace and automotive industries. Carr explains that for commercial single-aisle aircraft, the target for ASCEND is to enable production of composites-intensive aircraft at a rate of 100 shipsets per month; for the urban air mobility (UAM) market, that rate could be much higher.
Will Searle, chairman of Axillium, adds, “The main element of the program is developing not just demonstrator parts but a cross-sector and integrated supply chain solution for [the aerospace and automotive] industries, enabling manufacturing of products at higher rates going forward. Our challenge is to double the speed of productivity by which we can produce these new components regardless of the sector. That’s the core.”
Five themes: From design to inspection
ASCEND’s high-level goals are broken down into five themes:
- Lightweight design tools
- Future material systems
- Rate-capable automation
- Electrification and multifunctional
- Integrated hybrid structures
These five themes are demonstrated in 17 work packages, which are further broken down into 42 individual projects or “touch points,” as Searle describes them. Between the program’s start in 2021 and end in 2024, the goal is to get as much of the work as possible to technology readiness level (TRL) 6, with key rate targets demonstrated at the prototype level for automotive and aerospace markets.
In addition to the technology itself, Searle emphasizes that another important part to building the supply chain capability is creating new roles and skills in the workforce. Over the course of the ASCEND program, approximately 2,000 skilled jobs will be created in the U.K.
What follows is a summary of some of the progress for each program theme so far.
While also demonstrating individual technologies, all of the above packages are also working toward several demonstrator projects aimed at aerospace and automotive applications. Further, several of these demonstrators work directly between both industries — initially, a bladed aircraft wingtip and an automotive rear floor.
Aerospace demonstrators: Proving out automotive processes, rates
The aerospace demonstrators will showcase several processes: a filament-wound hydrogen storage tank; an RTM’d wing box; thermoformed prepreg trailing edge, wing ribs and spars; a curved wingtip skin laid up from tapes; and a bladed wingtip made with RTM’d NCFs.
According to Carr, the bladed wingtip demonstrator marks the first part developed in collaboration between GKN Aerospace and McLaren Automotive. GKN Aerospace designed the wingtip, comprising skins, spars and ribs, based on similar customers’ single-aisle aircraft wing designs and using next-generation stochastic topology optimization software from the Theme 1 work packages. This digital model was supplied to the McLaren team, which is working to optimize the design and process for higher rates using automotive principles. One of the main goals, Carr says, is to produce the part using a process that could reduce the takt time from an hour to 30 minutes.
What does this mean, exactly? Preforms for the wing skins and spars will be manufactured via RTM using NCFs and a specialized preforming process — materials and process originally developed by McLaren Automotive for its production automotive parts at the MCTC.
Integrated workflow for aircraft wingtip. The bladed wingtip and other ASCEND demonstrators serve to showcase how all of the program work package technologies combine to produce high-quality, high-rate composite components. Photo Credit: GKN Aerospace
Specifically, McLaren’s Elford explains that the all-composite chassis on its newly launched Artura plug-in hybrid EV served as one of the inspirations for the ASCEND program collaboration, and was the first product to be delivered from the MCTC since its founding.
Called the McLaren Carbon Lightweight Architecture (MCLA), the chassis “is fully integrated — the full structure, floor, cavity for the battery, crash structures, mounting hardware — everything integrated into a single, RTM molded component,” Elford says. “The RTM process is something we’ve been developing for the last 15 years, and in the last five years, we’ve been doing it in-house and made a huge amount of improvements to our own RTM system, some of which would be really significant in the aerospace world.”
How does the system reduce cycle times and improve throughput? Elford explains, “High-rate RTM is really our pivotal technology, and we’ve developed the technology all the way through the material supply chain — the process, the resin chemistry, down to a new blade geometry for the ply cutters to be able to cut thousands of pieces of carbon fiber per hour.”
One major improvement to the process is development of sophisticated, proprietary tooling that does not require cleaning or maintenance in between parts. A part is formed, the part is lifted off by a robot and then the tool can immediately be reloaded. “That’s conventional in a lot of injection molding practices, but it’s been nearly unachievable in the composites industry,” Elford notes. Integrated sensors for process monitoring also enable high visibility into process operations.
First wingtip components. The full wingtip demonstrator will be completed between now and the project’s end in 2024. As of early 2023, thermoformed ribs such as this one are the first physical components to be produced, manufactured using fast-cure prepregs developed for ASCEND by Hexcel and Solvay. Photo Credit: GKN Aerospace
To reduce cycle times further, McLaren has also developed a proprietary preforming process, using a specially designed molding machine that delivers a preform in two and a half to three minutes each, with a carousel system to change out tools to deliver different shapes. These semi-consolidated preforms are then loaded into the RTM machine for infusion and molding on self-heated tools. All of this technology was developed for McLaren’s high-performance road cars — “but we can see that there are so many obvious parallels to the aerospace industry,” Elford points out.
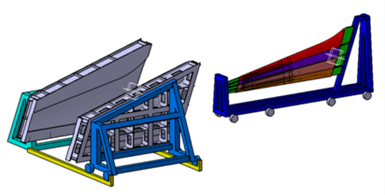
Tooling design. Part of the wingtip demonstrator project has been developing new RTM tooling for faster automated manufacture. Self-heated and shape memory polymer (SMP) tooling are among the technologies used. Photo Credit: GKN Aerospace
The ASCEND wingtip was chosen as the first part to demonstrate this technology in an aerospace component. The wingtip “also embodies some of our [automotive] design philosophies as well,” Elford notes. “The way we’re looking at the wingtip is, if it were a product on a car, how would we engineer it? How would we design it? How would we manufacture it, knowing that we can get into the realms of minutes per part in terms of takt time?”
For the wingtip project, self-heated shape memory polymer tools were developed to further reduce cost and improve processing time.
The final part will be completed by the project’s end next year; as of early 2023, the first physical components like thermoformed ribs are being manufactured (see image above).
Automotive demonstrators: Proving aerospace materials, quality
The two main automotive demonstrators for ASCEND are a rear floor and a door. “The rear floor is similar in some ways to many aerospace applications; it has a stressed skin, part of the rear frame provides stiffness to the rear of the car to support stability during cornering loads and braking forces and it’s a really critical aerodynamic surface,” Elford explains.
While the wingtip serves as an opportunity to demonstrate McLaren’s existing automotive technology for aerospace, the rear floor is an opportunity to develop the next generation of its automotive technology, he says.
“The next big challenge is eliminating the waste involved in the manufacturing process,” Elford says. “To do this, we’ve started developing our own tape deposition technology.”
This proprietary process, he explains, is an alternative to automated fiber placement (AFP) — “AFP is what you’d use to get the tape format with a near-net shape blank with zero waste, but it’s too slow for the rates we need.” So, the MCTC is developing a high-rate tape deposition process for layup of 2D blanks that can then be preformed and RTM’d.
McLaren Automotive has now manufactured its demonstrator rear floor prototype for the ASCEND project (see image below), and as of the end of 2022 was testing the floor on an Artura GT4 vehicle.
Automotive rear floor design. The rear floor component, shown here as a rendering attached to the rest of the vehicle chassis, demonstrates McLaren’s novel preforming and tape deposition process. As of the end of 2022, the first physical parts were completed and being tested on a vehicle. Photo Credit: McLaren Automotive
Benefits include high productivity, material cost savings due to reduction in waste material, slightly improved stiffness and significant weight savings over an aluminum part.
The tape material and process were developed by McLaren for ASCEND, with partner Sigmatex playing a key role.
After proving out the floor demonstrator, the next step within ASCEND will be to design and manufacture a vehicle door demonstrator. “It’s the next step up in terms of complexity,” Elford explains, including safety and quality requirements, load cases and the fact that it is a painted, RTM’d surface.
New challenges emerge when switching to tapes, Elford says, and the partnership and knowledge from GKN Aerospace are pivotal to the development process. He notes, “There are nuances to preforming with tape — gaps, overlap, spreading, the stability of tapes is fundamentally different than a stitched fabric [NCF]. There is a lot of development in preforming with tape, but it all happens with our existing technology. We have the ability to be able to change temperatures, pressures, speeds and so on to basically hone in on the best parameters that work with tape.”
The aerospace industry is “an expert in process validation of tape manufacturing in particular. They’ve been using tape for as long as we’ve been using RTM, so that’s really valuable — they have insight and knowledge on how a tape performs in a production infrastructure, and how to validate that through a process; it’s a really great opportunity for us to see how our approaches compare across industries and share our learning together. Aerospace is also on the cutting edge of inline process inspection, so that’s another opportunity.”
Next steps: Automated RTM cell, physical prototypes
As of the beginning of 2023, much of the work had been done for the first two themes — tooling, materials and part-level design, and the first physical parts were being produced. McLaren’s rear floor demonstrator was the first manufactured, along with several ribs and spars for the wingtip project.
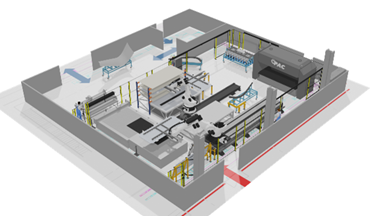
Automated work cell. ASCEND partner Airborne has developed a fully automated preforming and RTM cell to be installed at GKN’s Bristol-based Global Technology Centre in summer 2023, for producing several of the consortium’s aerospace demonstrator components. Photo Credit: Airborne
At GKN’s GTC, an automated preforming cell, designed by ASCEND partner Airborne, is set to be installed in August 2023 and will produce the final wingtip and wing box demonstrators. The teams are also working to increase the TRL of the SMP tooling and thermoformed rib demonstrators that have already been developed.
“We’re doing so much concurrently because we have a key focus on the products, and all the requirements that go into it. So we’re doing the design, the materials, the automation, the inspection — it’s all absolutely needed to be capable at the rates we need,” Carr notes.
Barlow adds, “There’s a lot of collaboration from the other partners as well, feeding into our work packages and us feeding into theirs. It does get quite complicated.”
What will it all come down to? High-TRL demonstrator parts, yes, but also materials and process know-how that can be transferred into other next-generation aerospace and automotive components. “It’s central to the success of ASCEND that we are not just focused on making parts in a factory,” Searle says. “We’re also establishing the capability to operate the factory at rate, with the best materials and a highly skilled workforce to accelerate the U.K. composites community.”
Related Content
Composite rebar for future infrastructure
GFRP eliminates risk of corrosion and increases durability fourfold for reinforced concrete that meets future demands as traffic, urbanization and extreme weather increase.
Read MoreThermoplastic composites welding advances for more sustainable airframes
Multiple demonstrators help various welding technologies approach TRL 6 in the quest for lighter weight, lower cost.
Read MoreCarbon fiber in pressure vessels for hydrogen
The emerging H2 economy drives tank development for aircraft, ships and gas transport.
Read MoreMaterials & Processes: Composites fibers and resins
Compared to legacy materials like steel, aluminum, iron and titanium, composites are still coming of age, and only just now are being better understood by design and manufacturing engineers. However, composites’ physical properties — combined with unbeatable light weight — make them undeniably attractive.
Read MoreRead Next
Using sensor data to improve composite parts and processes
nebumind software builds digital twins from manufacturing data to trace defects, compare manufactured parts, qualify processes, develop tolerance windows for process monitoring and more.
Read MoreAutomated aerocomposites production: Liquid molding or welded thermoplastic?
Two materials and process approaches are demonstrated for CFRP bulkhead production.
Read MoreComposites end markets: Energy (2024)
Composites are used widely in oil/gas, wind and other renewable energy applications. Despite market challenges, growth potential and innovation for composites continue.
Read More