SHD Composites supports sustainability initiatives with launch of epoxy prepreg systems
SHD introduces its MTB350 component prepreg system and LTB310-1 low-temperature cure epoxy tooling prepreg with 30% bio-derived content.
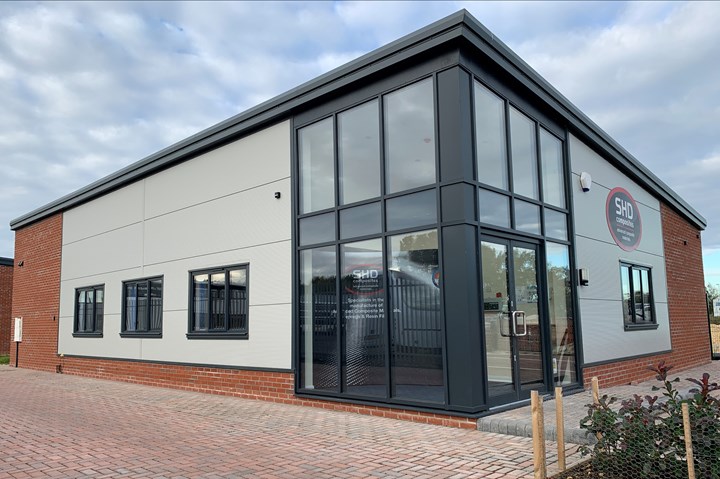
SHD Composites technical center, where its epoxy prepreg systems are developed. Photo Credit: SHD Group
SHD Group (Lincolnshire, U.K.), an industry supplier of high-quality structural and tooling prepreg materials, announces the launch of two new epoxy prepreg systems, both offering high bio-derived raw material content, as well as additive sustainability features. These novel materials have been specifically developed to assist SHD’s global customer base with its ever-increasing focus on sustainability and carbon reduction. Adding to established bio-based systems in SHD’s portfolio, these new products further underline SHD’s commitment to advance more environment friendly composite solutions.
MTB350 is a component prepreg system combining 30% bio-content derived from a renewable source, a range of advantegeous properties, potential for snap curing and a room temperature shelf life of at least 90 days. Bio content is certified to international standards and the extended room temperature life offered by MTB350 provides the potential to further reduce the total embodied energy in a final part and the costs (and risks) associated with storage and shipping of valuable prepreg materials.
LTB310-1 is a low-temperature cure epoxy tooling prepreg, also with 30% bio-derived content, with mechanical and processing performance reported to be on a par with other industry=-standard SHD tooling systems. Initial cures down to 45°C are possible with an ultimate Tg of over 200°C achievable after post cure.
To support the launch of MTB350 and LTB310-1, SHD has completed an extensive characterization and test marketing program, working across a range of reinforcement types. SHD has particularly focused on component applications with natural flax fibers and flax carbon hybrid (FCH) reinforcement types, seeking to further enhance the sustainability of finished composite components.
MTB350 and LTB310-1 will initially be available from SHD’s U.K. manufacturing site, with product rollouts from its European (Krsko, Slovenia) and U.S. (Mooresville, N.C.) manufacturing facilities in early 2022.
Related Content
-
Carbon fiber in pressure vessels for hydrogen
The emerging H2 economy drives tank development for aircraft, ships and gas transport.
-
One-piece, one-shot, 17-meter wing spar for high-rate aircraft manufacture
GKN Aerospace has spent the last five years developing materials strategies and resin transfer molding (RTM) for an aircraft trailing edge wing spar for the Airbus Wing of Tomorrow program.
-
Materials & Processes: Resin matrices for composites
The matrix binds the fiber reinforcement, gives the composite component its shape and determines its surface quality. A composite matrix may be a polymer, ceramic, metal or carbon. Here’s a guide to selection.