Clean Sky 2 OUTCOME project demonstrates PEEK thermoplastic composite wingbox cover
Airbus Defense and Space, FIDAMC and Aernnova demonstrate out-of-autoclave, one-shot process for wingbox cover with integrated stringers for regional aircraft.
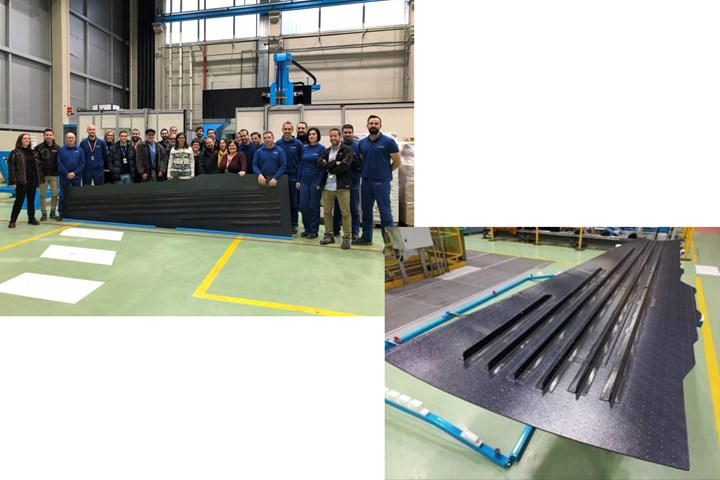
Photo Credit: Clean Sky 2 OUTCOME project
- OUTCOME has tested and validated the successful use of a PEEK thermoplastic composite in a wingbox cover for a regional aircraft.
- Using thermoplastic composites simplifies processing while delivering weight savings which lead to reduced fuel burn.
- The produced wingbox cover can be recycled at the end of its service life, saving valuable resources and enabling a circular economy.
Clean Sky 2’s OUTCOME project has devised a sustainable manufacturing process for producing a 4 × 1-meter stiffened thermoplastic composite (TPC) upper skin for the external wingbox of a regional/utility (Airbus C-295) aircraft. The project feeds into Clean Sky 2’s Airframe ITD D1-4/6 demonstrator for an advanced composite wingbox, which is the central structure of an aircraft that connects the wings with the main body/fuselage.
OUTCOME’s main objective was to replace autoclave-cured thermoset composite construction with TPCs using an energy-efficient out-of-autoclave (OOA), one-shot process. This production method comprises lamination of the wingbox cover skin and reinforcing stringers and then simultaneous consolidation of these into an integrated structure. This saves time and energy for improved sustainability while offering structures that are lighter in weight than their metal counterparts. For these reasons, the aeronautics sector is shifting to TPCs for future airframes.
Benefits of thermoplastic composites
FIDAMC (Madrid, Spain) is a center of excellence for research, development and innovation in composite material technologies and served as project coordinator for OUTCOME. Mar Zuazo Ruíz, R&D composites specialist at FIDAMC, notes that thermoplastic polymers improve the recyclability of composites and enable repeated thermoforming and reconsolidation. This also reduces the number of non-quality parts, notes Ruíz.
Airbus Defense and Space (ADS) served as the topic manager for OUTCOME and saw the potential for thermoplastic polymers to help meet increasingly stringent environmental regulations in the EU. “ADS has been involved in this technology since around 2010,” says Rubén Tejarina Hernanz, airframe R&T manager for integration at ADS, “when we saw that thermoplastics could be an alternative to thermosets for use on primary and secondary [aircraft] structures. We saw their sustainability potential in addressing not just recyclability of materials but to also help us meet EU REACH contamination regulations.”
In addition, FIDAMC also initiated projects using TPCs around 2007. These mutual interests converged through Clean Sky when Airbus, as Airframe ITD demo co-project leader, proposed launching a call for partners to explore the potential of TPC technologies. FIDAMC and aerostructures design and manufacturing specialists Aernnova (Madrid, Spain) responded and formed the OUTCOME consortium.
The partners decided to use a polyetheretherketone (PEEK) as the TPC matrix. PEEK matches the performance properties of thermosets, and even surpasses them in terms of ageing and damage tolerance, while bringing valuable weight savings. PEEK made it possible to reinforce the wingbox cover using stringers without the need for fasteners (bolts or rivets) which would have added weight and complexity.
Successful TPC wingbox cover
The OUTCOME consortium succeeded in reaching its objectives in a single trial, says Dr. Sonell Shroff, Clean Aviation project officer. She notes the team also confirmed predictions regarding spring-back, which is an unwanted condition where a composite part becomes distorted from its intended shape after it is released from the tool due to thermal stresses induced during cure.
Shroff says the consortium was successful in anticipating potential issues with the process of co-curing the TPC stringers to skin. “This could have been tricky, as when you attach the stringers you can have a lot of tension and difference in stresses in the two parts.” She emphasizes that the project represents a substantial achievement in terms of replacing thermoset composites with TPCs, which enable energy savings as well as minimum waste and scrap. “The consortium was spot on with their analysis and coupon tests — a lot of effort has been put into this whole process,” she adds.
The OUTCOME project results feed into Clean Sky 2’s Eco Transverse Activities (TA), working toward understanding the ecological benefits across the full lifecycle of aircraft components. “It’s uncommon to carry out R&T projects at full-scale component testing,” says Rubén, “but in OUTCOME, the component was designed and manufactured using the same approach as if it were to become a certified prototype. We performed the same tests that apply when submitting evidence to the airworthiness authorities and the resulting technology is applicable on horizontal or vertical tailplane structures. This could be beneficial for the future of European aviation.”
An EcoStatement study, documenting the assessment of the full wingbox is being compiled by the Clean Sky Airframe ITD and processed by ECO-TA, with results expected at the end of 2023. In the meantime, OUTCOME technology is already being applied in Clean Aviation’s HERWINGT and FASTER-H2 projects.
OUTCOME ran between January 2016 and December 2023, with the wingbox cover manufacturing completed between June 2022 and January 2023. The project budget of €600,000 was provided by the EU.
Related Content
Composite rebar for future infrastructure
GFRP eliminates risk of corrosion and increases durability fourfold for reinforced concrete that meets future demands as traffic, urbanization and extreme weather increase.
Read MoreRecycling end-of-life composite parts: New methods, markets
From infrastructure solutions to consumer products, Polish recycler Anmet and Netherlands-based researchers are developing new methods for repurposing wind turbine blades and other composite parts.
Read MoreThe making of carbon fiber
A look at the process by which precursor becomes carbon fiber through a careful (and mostly proprietary) manipulation of temperature and tension.
Read MoreThe state of recycled carbon fiber
As the need for carbon fiber rises, can recycling fill the gap?
Read MoreRead Next
One-piece, one-shot, 17-meter wing spar for high-rate aircraft manufacture
GKN Aerospace has spent the last five years developing materials strategies and resin transfer molding (RTM) for an aircraft trailing edge wing spar for the Airbus Wing of Tomorrow program.
Read MoreSTUNNING project completes lower half of MFFD
Clean Sky project has delivered the 8 × 4 meter welded aerostructure component, aided by advanced thermoplastic composite technologies and smart robotics.
Read MoreDaher CARAC TP project advances thermoplastic composites certification approach
New tests, analysis enable databases, models, design guidelines and methodologies, combining materials science with production processes to predict and optimize part performance at temperatures above Tg (≈150-180°C) for wing and engine structures.
Read More