Composites end markets: Energy (2024)
Composites are used widely in oil/gas, wind and other renewable energy applications. Despite market challenges, growth potential and innovation for composites continue.
Though faced with supply chain issues, renewable energy continues to grow worldwide thanks to government initiatives and carbon emissions reduction goals. For composites, onshore and offshore wind remain at the forefront, with numerous business announcements, new developments and R&D initiatives related to manufacturing, maintenance, recycling and more revealed over the past year. Photo Credit: GE Renewable Energy
The energy sector is a large consumer of composite materials, both for fossil-fuel based energy generation — such as wellhead components and pipelines for onshore and offshore oil and gas drilling — and renewable energy applications — like wind turbine blades and nacelles, and hydroelectric and tidal turbine blades. Wind turbine blades in particular, generally manufactured from infused fiberglass composites and, increasingly, reinforced with pultruded carbon fiber composite spar caps, remain a huge consumer of composite materials.
Of course, the changing global energy landscape has an effect on the manufacturing of all of these components. The International Energy Agency’s (IEA, Paris, France) World Energy Outlook 2023 claims that “the energy world remains fragile” due to geopolitical tensions, an unsettled global economy and more, but that at the same time, “the emergence of a clean energy economy … provides hope for the way forward.”
Government-led carbon emissions reduction targets and renewable energy-focused initiatives like REPowerEU in Europe and the Inflation Reduction Act (IRA) in the U.S. also incentivize a move toward renewables from fossil fuels.
According to the report, investment in clean energy has risen 40% since 2020, and as of the outlook’s publication in October 2023, more than 500 gigawatts (GW) of renewables generation capacity was set to be added by the end of 2023 — a new record, the report says, and led by solar energy.
In the U.S., the American Clean Power Association (ACP, Washington, D.C., U.S.) reported in its most recent “Clean Power Quarterly Market Report” for Q3 2023 that clean power capacity currently stands at more than 243 GW, accounting for 16% of total electricity generation. Similar to the IEA, the ACP reports that solar energy is currently leading in both renewable energy installations and in projects under development. Looking at wind energy, 15% of the project pipeline is said to be focused on land-based wind, and 12% on offshore wind.
Wind energy: Growth, challenges, new announcements
In its 2023 Global Wind Report, the Global Wind Energy Council (GWEC, Brussels, Belgium) cites the projected growth in wind over the coming decades as well as the challenges the industry has been facing, including inflation and high energy costs, stretched post-COVID-19-era supply chains, shipping and logistics bottlenecks, and more. The GWEC notes a need for “immediate investment and global cooperation” to address production bottlenecks for wind turbine production.
Despite these challenges, the GWEC reports nearly 78 GW of wind power capacity installed globally in 2022, the third highest year on record. The GWEC’s more targeted 2023 Global Offshore Wind Report says that 2022 was the second highest year ever for new offshore wind installations, led by China, with 8.8 GW installed globally.
Many new announcements also came out in 2023 related to production of composite wind blades and nacelles. For example:
- GE Renewable Energy (Paris, France) extended its supply agreement with blade manufacturer TPI Composites (Scottsdale, Ariz., U.S.), and agreed to add four new blade production lines at TPI’s facility in Juarez, Mexico.
- Vestas (Aarhus, Denmark) announced new partnerships such as a memorandum of understanding (MOU) to build an additional 384 MW in Ukraine as part of DTEK’s (Kyiv, Ukraine) Tyligulska wind project — in addition to new repowering orders in the U.S.
- Siemens Gamesa Renewable Energy (Zamudio Spain) announced plans to build a new offshore nacelle manufacturing facility in New York.
MingYang’s latest MySE 18.X-28X model features 140-meter-long blades, surpassing the 118-meter-long wind blades previously launched on the MySE 16.0-242 platform in 2021. Photo Credit: Mingyang Smart Energy via LinkedIn
Several new blade designs were launched, including Siemens Gamesa’s SG 4.4-164 high-capacity factor turbine and MingYang Smart Energy’s (Guandong, China) 18-MW MySE 18.X-28X offshore wind blades featuring 140-meter-long blades.
In October 2023, the first GE13-MW Haliade-X offshore wind turbine, originally announced as a 12-MW prototype in 2018, began producing power at the Dogger Bank Wind Farm off the coast of the U.K., following 3 years of testing.
New strategies in offshore wind were also announced. In the U.S., for example, in April 2023, the Department of Energy (DOE) announced the release of its Offshore Wind Energy Strategy, a comprehensive summary of its efforts to meet the current U.S. administration’s goal to deploy 30 gigawatts (GW) of offshore wind energy by 2030 and set the nation on a pathway to 110 GW or more by 2050.
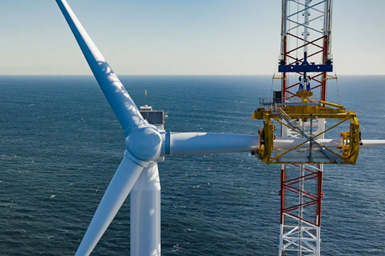
South Fork Wind turbine installation. Photo Credit: South Fork Wind
New offshore developments covered by CW include the start of building the 130-MW South Fork Wind offshore wind farm off the coast of New York, the approval of Ørsted (Fredericia, Denmark) and Eversource’s (Boston, Mass., U.S.) 704-MW Revolution Wind project off the coast of Rhode Island, the planned Åland Energy Island project aiming to integrate both offshore wind and hydrogen production in Europe, an announced 1.5-GW offshore project from Siemens Gamesa off the coast of Poland and more.
Automating wind blade maintenance
Repairing composite wind blades in the field is an important part of wind turbine maintenance, and is traditionally a manual process done by skilled field technicians. In response to a growing need for wind blade maintenance, blade manufacturer Aeris Energy (São Paulo, Brazil) established a new services division in the U.S.
There are also a number of new technologies available or on the horizon aiming to automate this process, ranging from using robotics to perform repairs to using drones or sensors to monitor wind blade health (see CW’s “On the Radar” collection of recent news in this field).
Growing wind blade production and wind energy development means a need for more optimized blade maintenance. A number of automated solutions have been launched or are in development. Photo Credit: Rope Robotics
Recycling and circularity of wind blades
Another challenge brought to light over the last few years is the need for more sustainable solutions for wind turbine blades at their end of life (EOL) or when decommissioned due to repowering projects.
There are many solutions in development by companies across the wind blade supply chain, as reported in CW’s 2022 feature “Moving toward next-generation wind blade recycling.” Generally, solutions involve mechanical or chemical recycling of the materials from wind blades at their EOL — or, in some cases, repurposing entire wind blades for other uses — and design efforts to make the wind blades themselves inherently more recyclable.
Siemens Gamesa was the first to bring its RecyclableBlade to market for offshore wind in 2021, with the first blades installed in Germany in July 2022. That sam year, the company also launched a new RecyclableBlade version for onshore wind projects. RecyclableBlades are made using epoxy with Aditya Birla’s (Mumbai, India) Recyclamine hardener, which enables the resin to be more easily separated from the fiber at the blade’s EOL. In February 2023, it was revealed that 132 total RecyclableBlades will be installed at RWE’s Sofia wind farm off the coast of the U.K.
These trends continue. In 2023, more OEMs and manufacturers have unveiled plans and made commitments toward more sustainable manufacturing and decommissioning of wind blades. For example, in February 2023, Vestas Wind Systems A/S (Aarhus, Denmark) announced it is working with the CETEC (Circular Economy for Thermoset Epoxy Composites) initiative and partners Stena Recycling (Frogner, Norway) and Olin (Clayton, Mo., U.S.) to use CETEC’s chemical-based process for reclaiming fibers and epoxy from blades. In June, Vestas also announced a sustainability partnership with Ørsted (Fredericia, Denmark), aiming for net-zero wind farms procured with recycled composite blade materials and recycled steel.
In an episode of the CW Talks podcast, CW editor-in-chief Scott Francis talks to Professor Alan Banks, innovation and industrial engagement supervisor at Ford Motor Co.’s Dunton Technical Center in the U.K., about Ford’s involvement in the EMPHASIZING project working toward wind blade recycling solutions. Photo Credit: CW
New collaborative research projects also continue to be launched. The REFRESH (Smart dismantling, sorting and Recycling of glass Fibre Reinforced composite from wind blade Sector through Holistic approach) consortium launched in February 2023 is a 48-month EU-funded collaborative program with the goal of developing a new circular approach to dismantling and recycling fiberglass composite wind blades. In addition, the EoLO-HUBs project, co-financed by the EU, is a new 48-month program that brings together 18 partners focused on dismantling blades, advancing pyrolysis and solvolysis techniques, and developing treatments for recovered fibers. Covered in a recent episode of the CW Talks podcast, the EMPHASIZING consortium, based in the U.K., aims to develop a recycled glass fiber that has higher mechanical properties even than virgin fiberglass.
In addition, more companies focused specifically on wind blade recycling continue to emerge. Newly announced companies include REGEN Fiber in Cedar Rapids, Iowa, U.S., which aims to reclaim wind blade materials for use in the concrete and mortar industries; and Continuum Composites Recycling in Denmark, which has developed a method for transforming reclaimed blade materials into panels for the interior construction market.
Research and innovation in wind energy
To address challenges as well as growth in all aspects of the wind energy market, the number of R&D initiatives and startups entering this field continues to grow as well, leading to new innovations.
For example, looking to speed deployment of offshore wind turbine generators (WTG), Tree Composites (Delft, Netherlands) has developed a fiberglass composite joint to connect steel tube members together in WTG foundation structures. The company claims this technology can replace resource-heavy welding, significantly reducing pre-operational emissions and increasing foundation structure manufacturing throughput by as much as 100%. (Read more in CW’s feature story on this technology).
Tree Composites’ TC-joint used in jacket foundations for wind turbine generators (WTGs) has the potential to increase foundation structure manufacturing throughput by 100% by eliminating welding, supporting efforts to reach climate goals. Photo Credit: Tree Composites
New announcements in 2023 have also included:
- A total of $30 million U.S. Department of Energy (DOE) funding for a variety of projects related to wind blade manufacturing projects, including a consortium led by Purdue University’s (West Lafayette, Ind., U.S.) Composites Manufacturing Simulation Center (CMSC), aiming to use large-format carbon fiber-reinforced thermoplastic 3D printing to automate wind blade tooling manufacture.
- The development of prototype carbon fiber composite, monocoque, fan-shaped wind blade designs from startup Xenecore (New York, N.Y., U.S.), using its thermoplastic microsphere technology.
- A collaborative project from the Center for Wind Energy Science, Technology and Research (WindSTAR, Alexandria, Va., U.S.) and wind blade manufacturer TPI Composites to use digital twins to optimize wind blade manufacturing.
- The OptiBlade project led by the Fraunhofer Institute for Manufacturing Technology and Advanced Materials IFAM in Germany that has developed a flexible and stretch-formable release film aimed at enabling faster, release agent-free wind blade manufacture.
- Beyond wind blades, a number of companies are developing or working on kite-based wind energy systems, some of which use composite materials. One example is HAWK (Hibernian Airborne Wind Energy Kites), a 2-year project launched in 2023 by Composites Testing Laboratory (CTL, Galway, Ireland) and partners.
- The 3-year ALMA project, including Siemens Gamesa, Airborne (The Hague, Netherlands) and university partners, launched with the goal of developing an automated preforming robotic system for layup of offshore composite wind blades.
Composites use in other renewable energy technologies
Wind turbine blades may be the largest users of composite materials in the renewable energy space, but these materials are also used in other renewable energy applications as well, such as hydroelectric and tidal turbine blades, and some solar panel components.
One example is the company Ocean Renewable Energy Co. (ORPC, Portland, Maine, U.S.), which builds hydrokinetic power generators for use in rivers, called RivGen Systems, enabled by fiberglass struts and carbon fiber composite foils manufactured by partner Hawthorn Composites (Miamisburg, Ohio, U.S.). The company has installed several commercial systems to provide clean power to remote areas, and continues to scale up its production while also developing even its next-generation tidal systems.
On the research side, announced in June 2023, the U.K. government’s Engineering and Physical Sciences Research Council (EPSRC) invested £7 million in a project called CoTide (Co-design to deliver Scalable Tidal Stream Energy). This project is bringing together researchers to develop tidal stream turbine systems, including use of composite materials, aiming to ultimately scale up cost-effective, reliable tidal energy generation.
Work is also being done to develop solar panels that benefit from the light weight of composite materials in some components. For example, at JEC World 2023, EconCore (Leuven, Netherlands) displayed a 65% lighter weight solar panel with partner Solarge (Weert, Netherlands), which replaces glass with a composite product made from recycled honeycomb and polymer.
Composites in oil/gas applications
While renewable energy applications are growing and top many of today’s headlines, traditional fossil fuels such as oil and natural gas are still leading energy production in much of the world.
Like in many other industrial applications, composites’ inherent corrosion resistance and light weight have led to adoption of composites over metals for a variety of wellhead protection components, frac plugs for hydraulic fracturing (fracking), offshore oil and gas pipes and more.
Thermoplastic composite pipes are used in offshore oil and gas drilling operations, as well as, increasingly, hydrogen production. Photo Credit: Element Materials Technology
For offshore oil and gas pipelines, in recent years, companies such as Strohm (formerly Airborne Oil & Gas, Ijmuiden, Netherlands) and Magma Global Ltd. (Portsmouth, U.K.) have led the way toward development and qualification of thermoplastic composite pipe (TCP) to replace metal in offshore pipelines. In 2023, announcements from Strohm have included multiple new contracts for its TCP jumpers used in offshore oil pipelines (including with ExxonMobil) and DNV qualification for its TCP pipes in use for flowlines or jumpers in deep waters. Magma Global continues to expand its reach for carbon fiber-reinforced polyetheretherketone (PEEK) m-pipes for subsea oil and gas drilling, including an extended partnership announced in November 2023 with Element Materials Technology (London, U.K.).
Beyond oil and gas, companies such as Strohm claim that TCP can be a key component to companies’ energy transition, with applications in transporting green hydrogen. For example, in 2023, Strohm announced its participation in the Dutch government-funded project OFFSET, which is developing an industrial-scale, floating green hydrogen and ammonia project and will use Strohm’s TCP for hydrogen transport.
In addition, composite solutions can also serve as efficient, corrosion-resistant solutions for repair of existing pipelines — similarly to how composites are used as a repair or strengthening solution for utility and civil infrastructure applications.
Related Content
Recycling end-of-life composite parts: New methods, markets
From infrastructure solutions to consumer products, Polish recycler Anmet and Netherlands-based researchers are developing new methods for repurposing wind turbine blades and other composite parts.
Read MoreJEC World 2022, Part 1: Highlights in sustainable, digital, industrialized composites
JEC World 2022 offered numerous new developments in composites materials, processes and applications, according to CW senior editor, Ginger Gardiner, most targeting improved sustainability for wider applications.
Read MoreJEC World 2022, Part 3: Emphasizing emerging markets, thermoplastics and carbon fiber
CW editor-in-chief Jeff Sloan identifies companies exhibiting at JEC World 2022 that are advancing both materials and technologies for the growing AAM, hydrogen, automotive and sustainability markets.
Read MoreMaterials & Processes: Fibers for composites
The structural properties of composite materials are derived primarily from the fiber reinforcement. Fiber types, their manufacture, their uses and the end-market applications in which they find most use are described.
Read MoreRead Next
AZL collaborative project to redefine hydrogen tank development
Kick-off meeting sparks comprehensive discussions on materials, manufacturing and design, setting the stage for composite-based hydrogen vessel solutions.
Read MoreComposites end markets: Sports and recreation (2024)
Light weight and high performance continue to make composites popular in the elite sporting good market. Sustainability in both materials and recycling solutions are a key innovation area.
Read MoreTop 10 CompositesWorld products of 2023
A variety of novel materials, processes targeting the composites industry’s light weight, sustainability and more rapid production efforts made CW’s top 10 most popular product pieces of 2023 based on Google Analytics.
Read More