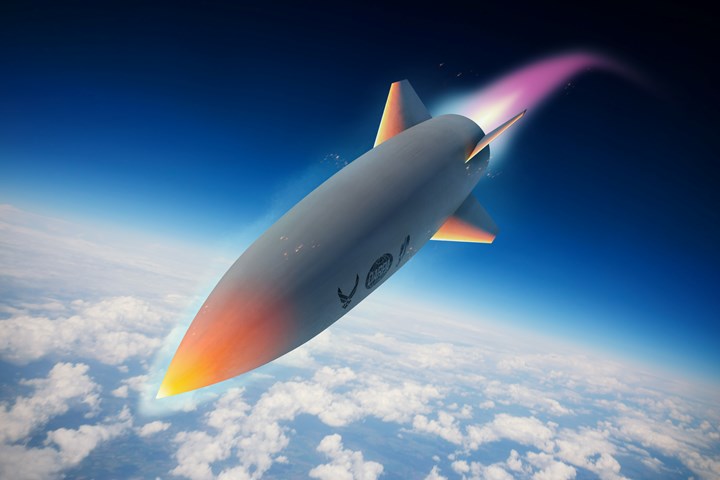
Photo Credit, all images: Lockheed Martin Skunk Works
Research and production of ultra-high temperature (UHT) ceramic matrix composites (CMC), with melting points of 2,500°C (4,532°F) or higher, has ebbed and flowed over the years, following rising and falling demand for applications like hypersonic defense systems and space launch vehicles.
The past few years, Lockheed Martin Skunk Works (Palmdale, Calif., U.S.) has emphasized investment and development of UHT materials, aiming to support current and future demand for CMC by the U.S. Department of Defense (DOD) and other aeronautics and space applications. In line with this goal, in Dec. 2020, Lockheed Martin acquired UHT materials company Allcomp Inc. (Rosamond, Calif., U.S.). In June 2022, a groundbreaking ceremony was held for an 8,000-square-foot expansion to Allcomp’s existing Rosamond, Calif., facility, bringing total square footage to 35,000 square feet.
“The big ‘why’ is hypersonics,” explains Brad Hanson, Lockheed Martin Skunk Works senior program manager for Allcomp. “Lockheed Martin is very involved in the hypersonics market, and not just the development of them but getting them into production.”
The market for hypersonics has followed the needs of the military, he explains; in the 1990s with the end of the Cold War, for example, U.S. DOD weapons systems decreased, reducing the need for a supply chain to produce UHT materials like CMC. As demand has risen more recently, Lockheed Martin decided to expand its role in the supply chain for these materials. “We needed to produce carbon-carbon [C-C] composites in-house at the production rates needed for the DOD,” he says.
This led in 2020 to the acquisition of Allcomp, a small R&D-focused CMC materials company that had previously been a supplier to Lockheed Martin. In addition to the relationship the companies already had, Hanson says Allcomp was attractive because “they had a diversity within their capabilities. They have multiple technologies under one roof with significant IP to address multiple high-temperature needs and solutions.”
Allcomp was started in 1999 by founder, Wei Shih, who has served as chief engineer since the acquisition in 2020. The company ran three facilities in California, starting with C-C composites and expanding over time to include carbon fiber-reinforced silicon carbide composites (C/Sic), UHT coatings and high-conductivity carbon foam.
Steve Jones, Allcomp engineering manager, adds, “The goal of legacy Allcomp was to try to bring as many processes in-house as we could in terms of fabrication of these materials. And we were able to expand each one of the different areas — preforming, densification, coatings — and build multiple methodologies of fabrication for each. I think that was one of the main strengths, was that we had multiple types of preforms, multiple types of densification processes and different types of coating systems that really allow us to tailor the material towards the application rather than trying to force a singular material into an application.”
Today, Allcomp is considered to be a department with Lockheed Martin Skunk Works. The original company headquarters in City of Industry, Calif., was closed this year. The expanding Rosamond facility is Allcomp’s new headquarters and production site, along with an R&D center at the Air Force Research Lab (AFRL) at Edwards Air Force Base in California.
Investing in the future of UHT CMCs
Since the acquisition, Lockheed Martin Skunk Works has worked to map out current and future needs for UHT materials not only of Lockheed’s other divisions — Aeronautics, Rotory and Mission Systems, Space Systems, Missiles and Fire Control — but of Allcomp’s legacy third-party customers as well, which the company continues to serve. This mapping has led to planning for future capital equipment acquisitions, personnel and facility expansion. “We’re setting up to establish production of C-C and C/Sic materials not just for Lockheed’s programs, but for the nation and the DOD,” Hanson emphasizes.
The current facility expansion in Rosamond, expected to be completed in Nov. 2022, will include new equipment and expanded capabilities such as five-axis machining and large heat-treat furnaces. “This is Allcomp’s first classified facility, so along with the ability to now do classified work, the goal is vertically integrated capabilities, all the way from material development and preforming to fabrication, machining, NDI [nondestructive inspection] and final coatings,” Hanson says. He adds that in addition to investing in the facility expansion and new equipment, Lockheed Martin is also investing in training and new personnel to grow the Allcomp division.
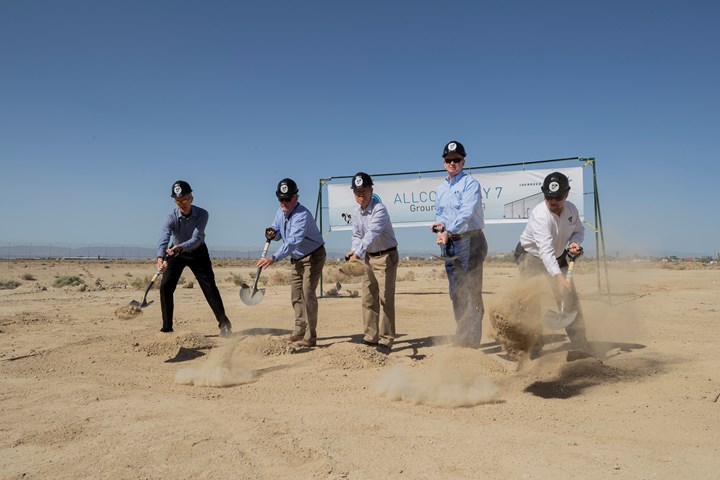
Lockheed Martin Skunk Works’ Allcomp team held a groundbreaking for its 8,000-square-foot expansion in June 2022. The facility is expected to be completed by November.
One of the main focuses is leading edges for hypersonic weapons, but Hanson notes that UHT materials are used to produce a variety of high-performance aerospace components as well, including C-C aircraft stators and rotors, C-C components for rocket motors, C/Sic rocket engine components and C-C bearing cages for aircraft turbine engines. “In general, the defense [aerospace] market is getting hotter, from hypersonics to aircraft, and thermal management is an issue. We’re scaling for everything,” Hanson says.
Fabrication capabilities include densification, preforming, autoclaves and ovens, as well as machining and NDI equipment. The new facility will not only include more equipment, Hanson emphasizes, but larger equipment: “We’re scaling up production capacity, but also part size capability,” he says.
Furthermore, while the acquisition by Lockheed Martin Skunk Works moved Allcomp’s focus mostly R&D to mostly production, Hanson emphasizes that R&D is still a large part of Allcomp’s operations.
“There are three prongs to our R&D focus right now,” Jones explains. “One is efficiency and reliability of the process. We’re really looking at getting the composites to that production level point that it’s just completely repeatable. Another area is in trying to get the [materials and process] costs down to make it affordable in these applications. Then you have the area of materials development.”
The first two areas are aided, Jones says, by Lockheed Martin Skunk Works’ emphasis on the “digital factory.” The original facility, he explains, was highly manual. “We want to eliminate a lot of those touch points with digitized or automated equipment, with real-time data collection. That goes toward our goal of more efficient processes. It becomes more reliable when you start using automated processes that mean the material is going to be the same every time, eliminating variability in composites fabrication.”
On the materials development side, R&D projects include developing higher-temperature or higher strength feedstocks or preform materials, as well as processes for making these materials, and new coatings targeting temperatures up to 2,760°C (5,000°F).
“It’s really quite the challenge to take a small R&D shop and scale it up to full production, but that’s what we’re doing, and the future is growing for Allcomp,” Hanson concludes.
Related Content
US Air Force selects Integris Composites ballistic body armor
Cratus Wave armor is thin, lightweight and reduces heat stress, providing buoyant personal protection for the 582nd Helicopter Group.
Read More2022 Farnborough International Air Show highlights
Farnborough, as usual, provided a platform for a variety of announcements in the aerospace, defense and advanced air mobility spaces from companies like GKN Aerospace, Joby, Airbus, Rolls-Royce, Boom Supersonic and others.
Read MoreToray Composite Materials America to double Torayca T1100 production capacity
The upgrade to the company’s Decatur, Alabama, carbon fiber plant is set to begin April 2023 in order to support rising demand in defense applications.
Read MoreFrom the CW Archives: Airbus A400M cargo door
The inaugural CW From the Archives revisits Sara Black’s 2007 story on out-of-autoclave infusion used to fabricate the massive composite upper cargo door for the Airbus A400M military airlifter.
Read MoreRead Next
Quiet supersonic demonstrator X-59 begins ground testing in Texas
Critical testing ensure the composite aircraft can withstand the loads and stresses that typically occur during supersonic flight.
Read MoreCW’s 2024 Top Shops survey offers new approach to benchmarking
Respondents that complete the survey by April 30, 2024, have the chance to be recognized as an honoree.
Read MoreComposites end markets: Energy (2024)
Composites are used widely in oil/gas, wind and other renewable energy applications. Despite market challenges, growth potential and innovation for composites continue.
Read More