Innovating thermoplastic composite repair. Msquare GmbH began as a research project at the German Aerospace Center (DLR) in 2015, which aimed to develop a technology for applying composite repair patches at high enough temperatures for high-performance thermoplastic aerostructures. Today, the technology is called FlexIn Heat and has been used for thermoset and thermoplastic composite repair and manufacture. Photo Credit, all images: Msquare GmbH
One challenge to the adoption of thermoplastic composites for large commercial aerostructures is that composites can be difficult to repair in the event of structural damage. To apply a repair patch to a damaged section of a part, a hot bonder or similar equipment must be used to supply and control the correct heat, pressure and vacuum needed to cure the patch onto the laminate.
When high-performance thermoplastics are involved — such as PEEK (polyetheretherketone), PEKK (polyetherketoneketone) and PAEK (polyaryletherketone) — this is even more challenging, because these materials require temperatures up to several hundred degrees Celsius to cure, a capability that many repair systems do not yet have.
One company presenting a solution is msquare GmbH (Stuttgart, Germany), with an electromagnetic induction-based, flexible heater blanket system capable of curing parts at high temperatures.
The basis for msquare’s technology began as a research project in 2015 through the German Aerospace Center (DLR, Stuttgart) by Markus Kaden and Marvin Schneider. Sonja Geenen, sales at msquare, explains, “They were looking for heating solutions for complete repairs on high-performance materials, like PEEK and PEKK, but they couldn’t find a heating blanket or mobile solution on the market that could cover this high temperature.”
Kaden and Schneider developed and patented the idea to use electromagnetic induction — the generation of heat through electricity via electromagnetic fields — in a flexible heating blanket that can reach up to 400°C. To commercialize the technology, which is now called FlexIn Heat, Kaden and Schneider founded msquare GmbH in 2018.
FlexIn Heat: Flexible, induction-based composite part repair
The FlexIn Heat system consists of multiple components. Msquare’s Red300 is a mobile hot bonder and controller that can be connected with thermocouple sensors and logs data digitally. This is wired to a custom-designed, three-layer product: a silicone heating blanket with an induction coil inside, an insulative layer and conductive metallic sheets, also called susceptors. These are stitched together via tailored fiber placement (TFP), resulting in a product that is about two millimeters thick.
Geenen explains that the induction system does not generate heat directly; rather, it “generates an electromagnetic field. The heat is generated when the electrically conductive susceptor material enters the electromagnetic field. Eddy currents are formed within the susceptor, which results in very high temperatures [up to 400°C] almost instantaneously and also very evenly.”
The susceptor can be any metal, she says, regardless of magnetism, or even carbon fiber, though the latter isn’t as conductive as metal. “The heating also depends on what kind of carbon fiber composite you [are trying to heat]. For example, if the composite uses unidirectional [UD] fiber, the inductive heating effect is a little bit less than what you get with woven fabric, because you need a lot of fiber crossings in the material to have a really nice heating effect,” she says.
Geenen explains that msquare has conducted studies in its lab heating a range of materials, “so that we have experience on what works for different materials and what inductive heating effect we can expect.” Thickness, fiber orientation and many other parameters can all affect the way the part is heated. “This makes it very complex,” Geenen says. Interested companies are encouraged to send msquare samples of the material first, so that they can be tested in the company’s lab to find optimum parameters such as the heat rate effect and limitations.
The FlexIn Heat system. The Red300 hot bonder generates electricity that, when introduced to the induction blanket, creates an electromagnetic field that contacts a conductive susceptor material to produce heat. The heated blanket can then be used to apply a repair patch to a composite part, or cure a part during manufacture.
In addition to reaching the needed temperatures for thermoplastics, this solution provides precise, localized heating because the blanket itself is not heated, only the susceptors. “You can cut these [susceptors] to the shapes you need to heat only the repair areas,” Geenen says.
Traditional heating blankets also tend to have an issue with heat sinks — meaning on a complex-shaped part, the heat may flow into a deeper curve or pocket on the part, leaving some areas above or below the desired temperature. “Our induction heating technology avoids this by providing a very high thermal capacity in the susceptor, so that it always stays hot and brings enough temperature to the surface of the part,” Geenen explains. “So, even though you have heat going down into the structure, you can maintain your target temperature for the surface.”
Msquare also developed the hot bonder and control unit, as well as the software used with the system, Geenen says. “We had a lot of input from companies like Airbus and other customers who are in the industry and have been dealing with these kinds of equipment for many years. They told us which features were important for us to include, and we have implemented those functionalities in our software.”
These include programming to specific heat ramps, with multiple heating phases if needed, or a controlled cooldown — the heating blanket can be heated during the cooling process to achieve a more gradual temperature decrease, and/or a cooling tube can be applied to cool the induction coils. This level of control is especially important when working with thermoplastic composites; users can be certain they are only reforming the needed area, and are adequately controlling forming and resolidifying of the material.
Geenen adds, “You can do a lot of different control options, with up to 16 temperature sensors that you can control. You can use the average value of all these sensors to control, or you can use [data from] a specific sensor.” She notes that while thermocouples are the sensor type currently used, the entire product is customized per project, so alternative sensor options could be considered as needed.
The data outputs into a CSV file that can be imported into Excel. The user also receives a graph detailing the temperature profile during the process. It can connect to a smartphone, tablet or laptop, so the process can be controlled and monitored remotely if needed.
In addition to its induction hot bonder and blanket systems, msquare also provides systems that use resistance air heating. These can also be used to repair or cure thermoset or thermoplastic composites, but at lower temperatures — up to 180°C for resistance heating blankets and 200°C for hot air heating. Hot air is used if the shape to be treated is complex and when it is difficult to apply a heating blanket.
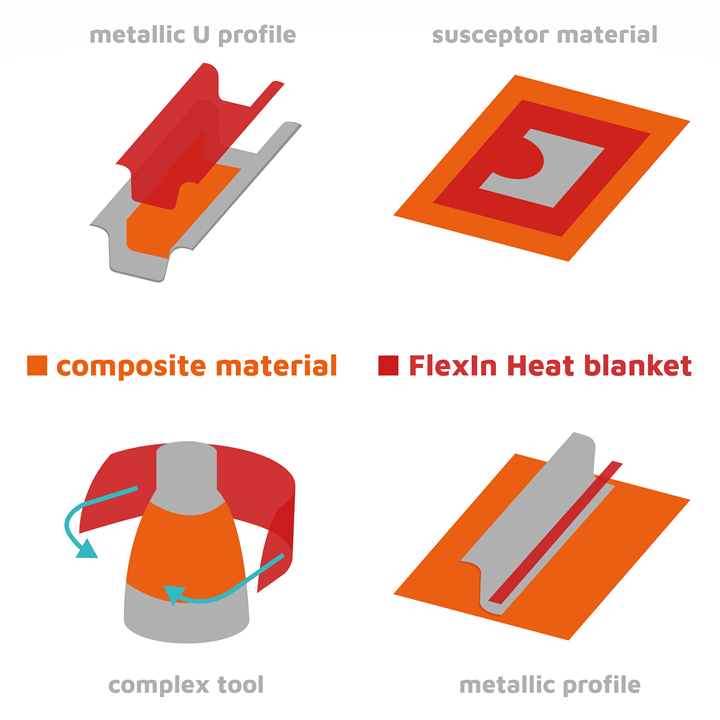
Flexible heating. Msquare’s technology can be custom-designed to fit a variety of needed shapes, such as the various configurations shown here.
Since launching commercially in 2018, FlexIn Heat has been used on several aerospace composite repair projects, Geenen says, including for Airbus (Toulouse, France). “We were selected for [Airbus’] BizLab accelerator for startup companies in 2019, where we spent a lot of time developing solutions for special Airbus use cases,” she says. For thermoset applications, the main benefit of FlexIn Heat was that the local heating enabled very precise heating to individual shapes. “You can also cover a lot of small repair locations with one blanket and one cure cycle.”
To date, even more interest has been shown in using FlexIn Heat for heated tooling for manufacture, Geenen notes. To cure a part during manufacture, the inductive heating susceptors are embedded into the press tool, instead of a silicone blanket. In this case, the susceptors can be heated and cooled rapidly in a controlled manner, which can help reduce cycle times.
As more thermoplastic composite aerostructures move out of R&D and take off, msquare anticipates the need for induction heating for repair as well as manufacture will continue to grow.
Continuing R&D: RETPAIR Clean Sky 2 project
Digital, data-driven repair. Msquare’s Red300 hot bonder can be connected to a smartphone or computer to store data from thermocouple sensors in the blanket.
The company is selling units commercially, while also engaging in ongoing R&D efforts to advance thermoplastic composite repair to meet current and future needs. One example is the Clean Sky project RETPAIR, which, in line with msquare’s goals, aims to help develop automated, flexible repair solutions for high-performance thermoplastics such as PEEK, PEKK and PAEK.
The project, spanning January 2021 to July 2023, is coordinated by research institute AIMEN Centro Tecnológico (Pontevedra, Spain) with partners msquare and CT Engineering Group (Madrid, Spain). The overall goal is to deliver repair solutions that can be adapted for an aircraft fuselage manufacturing line, airline or maintenance, repair and overhaul (MRO) facility.
Currently, RETPAIR is looking into induction welding of a flexible, pre-manufactured patch to the structure, or using additive manufacturing — such as fused filament fabrication (FFF) 3D printing, automated tape laying (ATL) or automated fiber placement (AFP) — for in-situ, layer-by-layer patch creation. For each method, the teams are emphasizing flexibility, control, digitalization and automation.
Related Content
UniSQ fire-retardant resins development bolster bushfire mitigation
The University of Southern Queensland has received funding to be used in the development of cost-effective composite resins to increase the resilience of wind turbine blades against bushfire exposure.
Read MoreCAMX 2022 exhibit preview: Renegade Materials Corp.
Renegade Materials is promoting its high-performance prepreg, RTM resin and adhesive products for use in demanding aerospace applications.
Read MoreMaterials & Processes: Resin matrices for composites
The matrix binds the fiber reinforcement, gives the composite component its shape and determines its surface quality. A composite matrix may be a polymer, ceramic, metal or carbon. Here’s a guide to selection.
Read MoreSuCoHS project: Advancing composite solutions for parts with high thermal and mechanical loads
New materials, structural concepts and manufacturing using sensors for composites that resist fire, temperature and loads while providing weight and cost savings versus metals.
Read MoreRead Next
Lifting arm concept and automated repair training to propel portable repair system
Looking to commercialize its Portable Scarfing/Composite Repair System concept, AGFM and partners offer specialized training, lifting and inspection systems.
Read MoreAlternate heat sources for hot-bonded composite repairs
Successfully using an alternate heat source for repairing composite structures requires an awareness of thermal dynamics and effective heat transfer management.
Read MoreComposites end markets: Energy (2024)
Composites are used widely in oil/gas, wind and other renewable energy applications. Despite market challenges, growth potential and innovation for composites continue.
Read More