Volkswagon launches new research collaboration with ORNL, University of Tennesse, Knoxville
Projects involve integration of advanced functional materials, novel recycling and wireless charging concepts to support electric mobility and sustainable transportation.
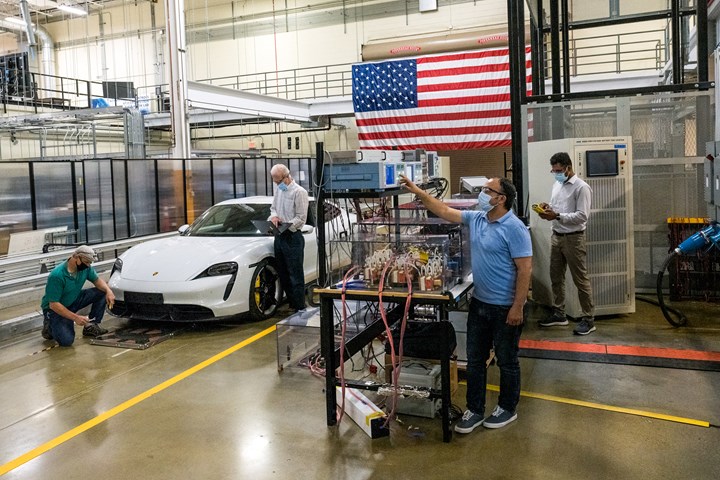
Oak Ridge National Laboratory (ORNL) researchers work in the Extreme Fast-Charging Lab in ORNL’s Grid Research Integration and Deployment Center. Photo Credit: Carlos Jones/ORNL, U.S. Dept. of Energy
Volkswagen Group of America’s (Herndon, Va., U.S.) Innovation Hub Knoxville (Tenn., U.S.), the company’s technology unit for applied materials science, has expanded its research collaboration with Oak Ridge National Laboratory (ORNL, Knoxville, Tenn., U.S.), reported to be the largest U.S. Department of Energy (DOE) science and energy laboratory, and the University of Tennessee, Knoxville (UT). The expanded collaboration aims to explore how to integrate breakthroughs in material science and recycling concepts — including fiber-reinforced composites — to support electric mobility and sustainable transportation. The first project involves testing ORNL’s new high-power wireless EV charging concepts with a Porsche Taycan.
“We aim to leverage the unique knowledge and innovative power the Tennessee Valley holds,” says Scott Keogh, president and CEO at Volkswagen Group of America Inc. “Volkswagen is focused to push electric mobility and new technologies for more sustainable transportation. Expanding our research collaboration with Oak Ridge National Laboratory and the University of Tennessee will help drive these efforts.” The expanded working relationship is just another example of Volkswagen’s growing engineering and technology footprint in the U.S., Keogh adds.
The interdisciplinary teams have started testing new wireless charging concepts for electric vehicles (EVs), with the goal to develop a higher power wireless charger through breakthrough designs that focus electromagnetic waves to eliminate interference, thus increasing efficiency. In the first trials, a prototype system has shown a high level of efficiency, with up to 98% of the energy used (coil-to-coil) reaching the vehicle battery.
“We are excited to work with Volkswagen to demonstrate ORNL’s high-powered, ultra-efficient wireless charging technology,” says Xin Sun, associate laboratory director for Energy Science and Technology at ORNL. “Our unique polyphase electromagnetic coil design and power electronics provide high power transfer levels in a compact system, with the potential to alleviate EV range anxiety and speed the decarbonization of the U.S. transportation sector.” The wireless charging project is supported by the DOE Office of Energy Efficiency & Renewable Energy’s Vehicle Technologies Office.
Using Volkswagen’s expertise in vehicle integration, the teams also have been able to build from a charging power level of 6.6 kilowatts up to 120 kilowatts, with a goal of 300 kilowatts, enough to provide an 80% recharge of the Porsche Taycan in about 10 minutes. The research project aims to generate new insights into the technological and physical hurdles of high-power wireless charging for automobiles.
Other research projects at Volkswagen’s Innovation Hub Knoxville focus on advanced functional materials, including composite car body parts and plant-based materials for future interior designs. The team is also working on new recycling concepts for materials conventionally deemed non-recyclable, such as fiber-reinforced composites.
“Our work with Volkswagen fits with our vision to create a more just, prosperous, and sustainable future through our research,” says Deb Crawford, UT Knoxville vice chancellor for research and innovation. “Volkswagen is a model innovation partner, and understands the value that co-location with a world-class research university creates. Together, we are identifying technological solutions that could lead to a more sustainable future for our planet.”
Volkswagen is a member of the Institute for Advanced Composites Manufacturing Innovation (IACMI, Knoxville, Tenn., U.S.), a research and innovation consortium funded at UT by the DOE. Volkswagen also works closely with UT Chattanooga, an MBA program that lets its employees earn the degree by taking classes at the Chattanooga assembly plant or on campus.
Volkswagen Group of America opened its Innovation Hub Knoxville in early 2020, in partnership with UT. Since then, the unit has established working relationships with universities and key researchers in the region. The Innovation Hub Knoxville joins the global Volkswagen Group’s larger innovation ecosystem, including innovation centers in Belmont, California; Wolfsburg, Germany; and Beijing, China, along with hubs in Barcelona, Spain; Tel Aviv, Israel; and Tokyo, Japan.
“The global Volkswagen Group aims to build a more sustainable vision of future mobility worldwide, and we connect the best researchers in the world to make that a reality,” concludes Nikolai Ardey, executive director group research at Volkswagen Group. “Co-innovating with partners like Oakridge National Laboratory and the University of Tennessee helps to multiply the power of Volkswagen’s international innovation team.”
Related Content
Plant tour: Middle River Aerostructure Systems, Baltimore, Md., U.S.
The historic Martin Aircraft factory is advancing digitized automation for more sustainable production of composite aerostructures.
Read MoreWhy aren't composites synonymous with infrastructure?
The U.S. seems poised to invest heavily in infrastructure. Can the composites industry rise to the occasion?
Read MoreMaterials & Processes: Composites fibers and resins
Compared to legacy materials like steel, aluminum, iron and titanium, composites are still coming of age, and only just now are being better understood by design and manufacturing engineers. However, composites’ physical properties — combined with unbeatable light weight — make them undeniably attractive.
Read MorePlant tour: Dowty Propellers, Gloucester, U.K.
Transforming decades of design and RTM production reliability into more sustainable, next-generation composite propellers.
Read MoreRead Next
CW’s 2024 Top Shops survey offers new approach to benchmarking
Respondents that complete the survey by April 30, 2024, have the chance to be recognized as an honoree.
Read MoreComposites end markets: Energy (2024)
Composites are used widely in oil/gas, wind and other renewable energy applications. Despite market challenges, growth potential and innovation for composites continue.
Read MoreFrom the CW Archives: The tale of the thermoplastic cryotank
In 2006, guest columnist Bob Hartunian related the story of his efforts two decades prior, while at McDonnell Douglas, to develop a thermoplastic composite crytank for hydrogen storage. He learned a lot of lessons.
Read More