Dolphitech capability study benchmarks dolphicam2 NDT platform
A CFRP panel was manufactured to the specification of an FAA NDI Proficiency specimen 2A, representative of composite laminates found on commercial aircraft.
Figure 1. a) Photograph of the bottom face of the panel showing the ply build ups/sound dampers. Photo Credit, all images: Dolphitech
Dolphitech (Gjøvik, Norway) performed a recent capability study to provide insight into how effective the dolphicam2 ultrasonic platform is — a system supporting ultrasonic nondestructive testing (NDT) — when inspecting composites on aircraft. To perform this study, the company used a carbon fiber-reinforced plastic (CFRP) panel representative of the solid laminate composites on commercial aircraft, such as on a Boeing 787 or on an Airbus A350.
The inspection panel used to assess the performance of the NDT equipment was made to the specification of a Federal Aviation Administration (FAA) NDI Proficiency specimen 2A and featured various manufacturing flaws typical of aerospace composites. Specifically, the panel was a 24 ply co-cured substructure (16 ply skin with eight ply stiffeners and built-up pads). The sample was designed to include a wide range of common flaws in this relatively compact inspection sample.
According to Dolphitech, the dolphicam2, used with a TRM-CI-5MHz transducer (TRM), was able to successfully inspect the FAA NDI Proficiency Specimen 2A. All of the manufactured flaws were clearly resolved and characterized. The flaws present included missing sealant, pillow inserts, Dremel cut, flat bottom holes, prepreg backing and grease.
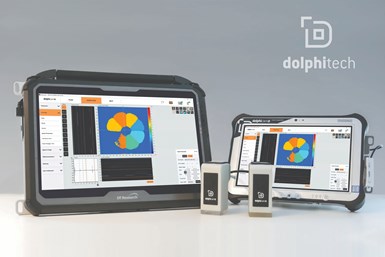
In conclusion, Dolphitech notes that the time and cost savings enabled by the dolphicam2 are demonstrated by its ability to characterize such a wide range of flaw types with a single setup. Similarly, the TRM-CI-5MHz transducer is said to be versatile and well-suited for many aerospace applications featuring thin to moderate thicknesses of both composites and metals.
Contact sales@dolphitech.com to request the full study or it can be accessed online here.
Related Content
-
Infrared NDT well-suited to demanding in-service, manufacturing and research applications
CAMX 2023: High-precision, cost-effective thermographic NDT technologies offered by Thermal Wave Imaging addresses real-world inspection challenges.
-
NCMS report demonstrates thermography innovations for enhanced NDI capabilities
Technology brief highlights how thermographic signal reconstruction (TSR) has enhanced the readiness of aircraft in less time and at lower cost, with potential for use inspecting composites and metals.
-
Loop Technology develops robotic arm for wing box inspection
Part of an R&D project with Spirit AeroSystems, the seven-axis Bravura robotic arm automates inspection and sealing within small spaces like aircraft wing boxes.