Auburn University make strides in advancing bio-based polymers and fibers for 3D-printed home construction
Interdisciplinary project utilizes biomaterial waste for sustainable composites development to produce resilient buildings with a low carbon footprint.
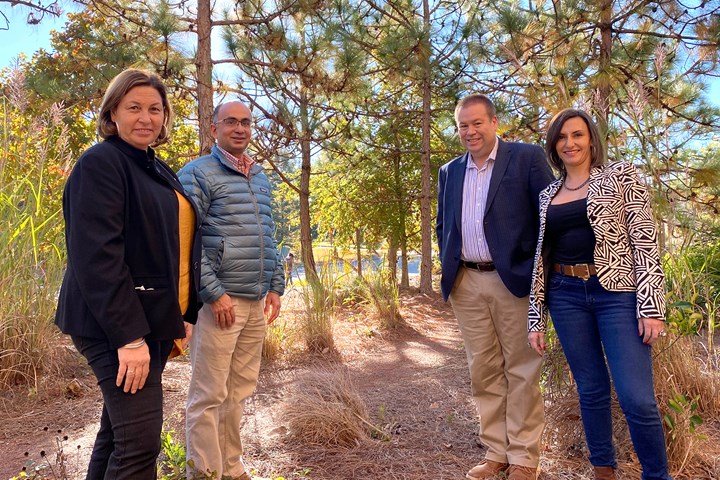
Auburn University faculty are part of an interdisciplinary research team that received a multimillion-dollar grant from the National Science Foundation’s Research Infrastructure Improvement Program to develop composite materials from waste resources for additive manufacturing to create more affordable and environmentally friendly housing or building components. Pictured, left to right, are Auburn’s lead scientists, Maria Auad of the Samuel Ginn College of Engineering, Sushil Adhikari of the College of Agriculture and Brian Via and Maria Soledad Peresin of the School of Forestry and Wildlife Sciences. Photo Credit: Auburn University
An interdisciplinary project connecting several Auburn University (Ala., U.S.) faculty and fellow scientists seeks to make strides in future advanced manufacturing, including developing affordable homes constructed via 3D printing. The study, which spans the disciplines of engineering, chemistry, forest resources and architecture, also draws strongly upon the expertise of scientists at its partner institution, the University of Idaho (Moscow), with Michael Maughan, an assistant professor of mechanical engineering, at the helm.
The Auburn-led portion will focus on bio-resin development as a feedstock for 3D printing, which will be done at Idaho. This process will include conversion of biomass into chemicals and nanomaterials to help improve the sustainability of the resin. The project will also investigate the environmental impact of conventional concrete and steel used in the construction of traditional buildings, in comparison with tall timber buildings, which emit only one-third to one-half of the greenhouse gases traditional materials emit.
“Recently, the U.S. is trending toward mass timber buildings as a first-generation material to reduce our carbon footprint,” says Brian Via, the Regions Bank Professor in Auburn’s School of Forestry of Wildlife Sciences and director of the school’s Forest Products Development Center. “However, advanced manufacturing can help to utilize more biomaterial waste from forest resources that can then be 3D printed into housing or building components.”
The proposed interdisciplinary project, “Developing a Circular Bio-Based Framework For Architecture, Engineering and Construction Through Additive Manufacturing,” targets what is called the Advanced Manufacturing Industry of the Future.
“The project offers a unique opportunity to both undergraduate and graduate students to be involved in cutting-edge technologies and sustainable development.”
“We will manufacture 3D-printed wall panels that can be used in housing and building construction,” Via says. “This will allow for precise construction in a manufacturing environment using sustainable materials that can be shipped to the construction site. Through bio-based polymers and fibers, we can 3D print building components that allow for end-of-life [EOL] recycling.”
Research team member Maria Auad, the W. Allen and Martha Reed Professor in Auburn’s Samuel Ginn College of Engineering and director of the Center Polymer and Advance Composites at Auburn, say the project relies in large part on developing sustainable adhesives derived from renewable forest biomass and other waste resources, typically disposed of in landfills.
“The thematic basis of our proposal is to develop innovative materials that will be environment-friendly, less dependent on depleting petroleum resources and will use natural sources or waste products with the realization of the impact on the environment that the current generation of composite materials have at the end of their life,” Auad notes.
Team member Sushil Adhikari, professor in the College of Agriculture and director of Auburn’s Bioenergy and Bioproducts Center, adds that it is crucial to find ways to use forest biomass and other agricultural residues to produce resilient buildings with a low carbon footprint.
“In this project, we are developing resins and adhesive from waste materials while minimizing the energy input,” Adhikari says. His role is to find ways to produce chemicals using a fast process of pyrolysis — the thermal degradation of plastic waste at high temperatures in the absence of oxygen —for resin synthesis. He will also train graduate students and postdoctoral students who will contribute to circular-based bioeconomy research.
In addition, in this research, Maria Soledad Peresin, associate professor of forest biomaterials in the School of Forestry and Wildlife Sciences, is focused on nanocellulose production, characterization and chemical modification to be included in bio-resin formulations to improve the mechanical performance of the composites for 3D printing of housing and building components. As with Adhikari, she is enthusiastic about this venture’s effect on the next generation of scientists.
“The project offers a unique opportunity to both undergraduate and graduate students to be involved in cutting-edge technologies and sustainable development,” Peresin says.
Tthe educational impact is a also key component, as one endeavor of the research is to train a new STEM-based workforce and scientists for this industry’s future. “This team comprised of researchers from diverse specialties throughout the Auburn campus is creating a template for the future of sustainable manufacturing, including workable approaches to the lack of affordable housing and so much more,” says Janaki Alavalapati, dean of the School of Forestry and Wildlife Sciences. “Their inclusion of undergraduate and graduate students, as well as those in postdoctoral study, ensures that these innovations continue and build upon one another.”
Related Content
Materials & Processes: Resin matrices for composites
The matrix binds the fiber reinforcement, gives the composite component its shape and determines its surface quality. A composite matrix may be a polymer, ceramic, metal or carbon. Here’s a guide to selection.
Read MorePlant tour: Middle River Aerostructure Systems, Baltimore, Md., U.S.
The historic Martin Aircraft factory is advancing digitized automation for more sustainable production of composite aerostructures.
Read MoreThe state of recycled carbon fiber
As the need for carbon fiber rises, can recycling fill the gap?
Read MoreThe making of carbon fiber
A look at the process by which precursor becomes carbon fiber through a careful (and mostly proprietary) manipulation of temperature and tension.
Read MoreRead Next
Mighty Buildings raises $100 million to make carbon-neutral, 3D-printed construction a reality
Funding accelerates carbon neutrality roadmap which includes research and development of new composite materials produced from recycled or bio-based feedstock for net-zero construction by 2028.
Read MoreFrom the CW Archives: The tale of the thermoplastic cryotank
In 2006, guest columnist Bob Hartunian related the story of his efforts two decades prior, while at McDonnell Douglas, to develop a thermoplastic composite crytank for hydrogen storage. He learned a lot of lessons.
Read MoreCW’s 2024 Top Shops survey offers new approach to benchmarking
Respondents that complete the survey by April 30, 2024, have the chance to be recognized as an honoree.
Read More