FLEXOP aeroelastic wings achieve first flight
As part of the European Union’s FLEXOP project, DLR and TUM researchers are working on new technologies to control flutter while allowing wings to be made lighter.
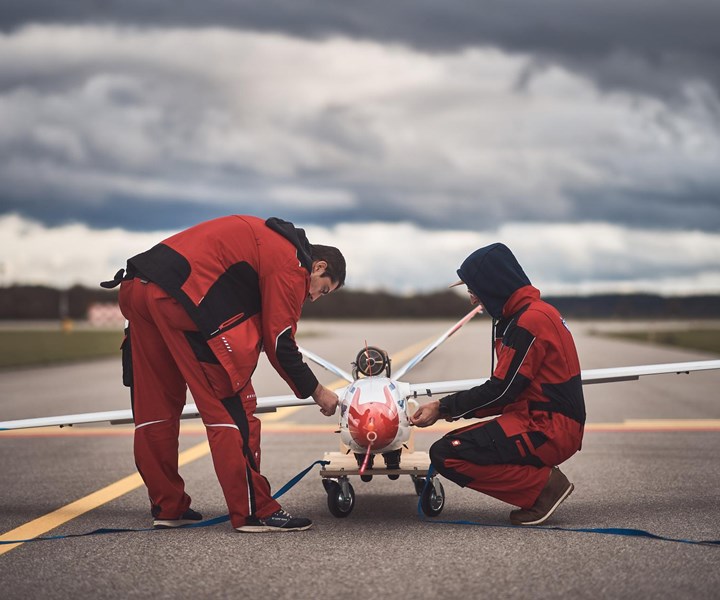
Source | DLR
In a collaboration between the German Aerospace Center (Deutsches Zentrum für Luft- und Raumfahrt; DLR, Göttingen, Germany) and the Technical University of Munich (TUM, Munich, Germany), researchers have succeeded in developing new technologies for lighter yet extremely stable wings. The aeroelastic wings made their first flight on November 19 at Oberpfaffenhofen airport (Weßling, Germany).
Wings with longer spans and lower weight generate less drag, and are therefore more energy efficient. The limiting factor for the construction of such wings is the aerodynamic phenomenon of flutter. Wing oscillations increase due to drag and wind gusts.
“Flutter causes material fatigue and can even lead to the failure of the wing attachment to the fuselage," explains Sebastian Köberle, a researcher at the TUM Institute of Aircraft Design.
Although any wing will begin to flutter at sufficiently high speed, shorter and thicker wings have greater structural stiffness, and hence greater stability. Building wings with longer spans that are just as stable and stiff would make them much heavier. In the European Flutter Free FLight Envelope eXpansion for ecOnomical Performance improvement (FLEXOP) project, researchers from six countries are working on new technologies to control flutter while allowing wings to be made lighter.
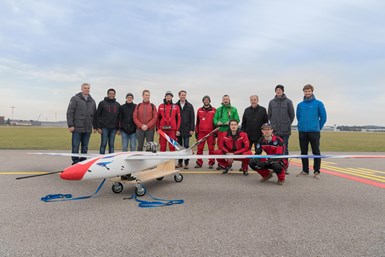
FLEXOP. Researchers from six countries are working on new technologies to control flutter while allowing wings to be made lighter. Source | DLR
The partners in the EU FLEXOP project are the Hungarian Academy of Sciences (MTA SZTAKI, Budapest, Hungary), Airbus Group Innovation (Ottobrunn, Germany), Airbus Group Ltd. (London, U.K.), FACC Operations GmbH (Ried im Innkreis, Austria), INtegrated Aerospace Sciences COrporation (INASCO, Athens, Greece), Delft University of Technology (Delft, Netherlands), the German Aerospace Center (DLR), the Technical University of Munich, the University of Bristol (Bristol, U.K.) and RWTH Aachen University (Aachen, Germany).
Two wing designs
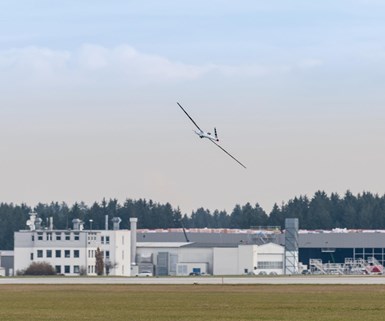
Aeroelastic wings. DLR’s aeroelastic wings made their first flight on November 19 at Oberpfaffenhofen airport (Weßling, Germany). Source | DLR
TUM researchers are responsible for the design and execution of the flight tests that demonstrate the behavior of the two novel wings developed by the project — the aeroelastic wing and the flutter wing. The TUM team first built the three-and-a-half-meter-long and seven-meter-wide flight demonstrator and integrated the various systems provided by the European partners.
A particularly light wing, which has now been flown for the first time, is an aeroelastically optimized wing constructed from carbon fiber-reinforced composites. It was developed by DLR, in collaboration with Delft University of Technology. The researchers were able to influence its bending and torsional behavior through a special alignment of the fibers during the construction of the wing.
“When the wing is bent by aerodynamic forces, it rotates simultaneously and thereby reduces airflow-induced loads,” says Wolf-Reiner Krüger of the DLR Institute of Aeroelasticity in Göttingen.
With the help of the reference wings, the TUM researchers worked in advance to have the flight demonstrator automatically fly predefined flight test patterns. They devised optimum settings and developed manuals and checklists for the flight tests.
“The flight demonstrator has to fly fast enough with the new wings that they would theoretically have to flutter,” explains Köberle. “We have to be sure that nothing goes wrong at such high speeds.”
Another super-efficient wing developed in the project is the flutter wing. This is a TUM design and is made of fiberglass. If fluttering occurs, the outermost flaps are extended and act like dampers.
“The active flap control developed at DLR considerably increases the possibilities for a much lighter design,” says Gertjan Looye of the DLR Institute of System Dynamics and Control in Oberpfaffenhofen, which manages DLR’s share of the project.
A second flight control system is being developed by the Computer and Automation Research Institute of the Hungarian Academy of Sciences (MTA SZTAKI).
Project Manager Bálint Vanek of MTA SZTAKI says, “Such a wing would make it possible to transport 20% more cargo or to reduce the required fuel by 7%.”
The technology is particularly complex, so tests on this wing will take place at a later date. Both variants of the super-efficient wing have already been evaluated during static vibration tests conducted at the DLR site in Göttingen.
The wings will not only be used on a flight demonstrator. In a further step, the results of the project will be transferred to configurations for transport and passenger aircraft.
Related Content
Cryo-compressed hydrogen, the best solution for storage and refueling stations?
Cryomotive’s CRYOGAS solution claims the highest storage density, lowest refueling cost and widest operating range without H2 losses while using one-fifth the carbon fiber required in compressed gas tanks.
Read MorePlant tour: Joby Aviation, Marina, Calif., U.S.
As the advanced air mobility market begins to take shape, market leader Joby Aviation works to industrialize composites manufacturing for its first-generation, composites-intensive, all-electric air taxi.
Read MoreThe state of recycled carbon fiber
As the need for carbon fiber rises, can recycling fill the gap?
Read MorePlant tour: Spirit AeroSystems, Belfast, Northern Ireland, U.K.
Purpose-built facility employs resin transfer infusion (RTI) and assembly technology to manufacture today’s composite A220 wings, and prepares for future new programs and production ramp-ups.
Read MoreRead Next
Airbus Albatross features flapping wings made from composites
Airbus demonstrates first in-flight, flapping wing-tips that could revolutionize aircraft wing and wing box design.
Read MoreDLR tests flexible and actively-controlled wing designs
Carbon and glass fiber aeroelastic and flutter wing concepts tested as part of multi-partner FLEXOP project.
Read MoreComposites end markets: Energy (2024)
Composites are used widely in oil/gas, wind and other renewable energy applications. Despite market challenges, growth potential and innovation for composites continue.
Read More