
MAMBO is a 6.5-meter demonstrator boat developed by Moi Composites to show the capabilities of the company’s Continuous Fiber Manufacturing (CFM) additive manufacturing process for large marine structures. Photo credit, all images: Moi Composites
Since patenting its continuous fiber manufacturing (CFM) process in 2015, Moi Composites (Milan, Italy) has explored a range of applications for its deposition-based, continuous fiber 3D printing CFM technology, including propeller blades and prosthetics. Key features of CFM include Moi Composites’ custom design software, ultraviolet (UV) cure, the use of robotic arms and “hybrid” manufacturing — more traditional composites lamination on top of a 3D-printed structural core (see “Continuous Fiber Manufacturing (CFM) with moi composites” for more on CFM).
Recently, the company demonstrated its CFM technology as a solution for faster, more cost-effective and innovative marine structures’ design and manufacturing, through a demonstrator motor boat called MAMBO that officially debuted at the Genoa Boat Show in October 2020.

To achieve the complex, organic shapes Moi Composites and its partners envisioned for MAMBO, Autodesk software was used to design the 50 individual, 3D-printed pieces that would be manufactured and assembled.

According to Gabriele Natale, co-founder of Moi Composites, he and fellow co-founder Michele Tonizzo came up with the idea for MAMBO at the 2017 Genoa Boat Show in Italy. Natale, who is also a fishing enthusiast, says that he and Tonizzo realized that many increasingly creative and innovative boat designs never end up being built or prototyped because the tooling costs for building large, complex fiberglass composite boat hulls can be too expensive, and the manufacturing logistics too complicated. Natale and Tonizzo recognized that their moldless, continuous fiber 3D printing technology could be an enabling solution. “From there, we started to develop a plan, and began to meet with partners within the marine industry,” Natale says.
MAMBO is 6.5 meters long by 2.5 meters wide, with a dry weight of approximately 800 kilograms. It is equipped with a navigation system, cork flooring, white leather seats and 115-horsepower (hp) engine. Moi Composites worked with marine design engineering studio MICAD (Lecce, Italy) on the structural design concept for the boat, which combines organic shapes into its structural elements inspired by the famous Arcidiavolo catamaran by Sonny Levi. Autodesk (San Rafael, Calif., U.S.) Fusion 360 CAD software and NETFABB additive manufacturing software were used in the design and fluid dynamic analysis of the components.
According to Dominique Müller, research manager on the additive manufacturing team at Autodesk, MAMBO is one of several case studies that Moi Composites and Autodesk have partnered on over the past four years. “The CFM printing process is so complex in terms of process control. We’ve been working with Moi for many years to help them calculate their toolpaths, control their robots, and making sure their process is well-equipped from a process-driven perspective,” she says. “With MAMBO, we wanted to scale all of that up.”
Printing and assembly
The hull and deck of the boat were printed with unidirectional (UD) continuous glass fiber supplied by Owens Corning (Toledo, Ohio, U.S.) and vinyl ester resin. “Our product is fully adapted to innovative manufacturing processes and offers significantly improved performance in mechanical properties,” notes Dr. Anne Berthereau, science and technology VP for composites at Owens Corning.

Using Moi Composites’ deposition-based, UV-cure CFM technology, robotic arms and digital design software, printing of the components was split between Moi’s Milan facility and partner Autodesk’s Advanced Manufacturing Facility in the U.K.
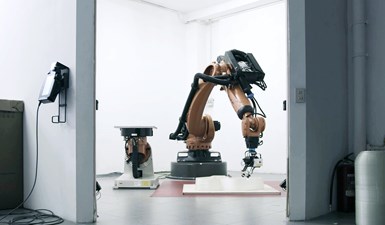
The boat was designed for manufacture in 50 individual printed sections, half of which were printed at Moi Composites’ Milan facility, with the other half printed at partner Autodesk’s Advanced Manufacturing Facility (ACF) in Birmingham, U.K. Moi Composites’ deposition-based CFM 3D printing technology, which incorporates a UV light alongside the printhead for in-situ cure, and dual KUKA robots were used at both facilities. “We split the sections on a cloud-based shared file platform to keep track of the section production. In this way, we were able to print the entire boat quickly,” Natale explains. Total print time for all components was approximately two months.
According to Autodesk’s Müller, the installation of a CFM system at Autodesk’s technology center not only helped Moi Composites speed the MAMBO printing process on a bigger system than what they had at their facility, but also enabled her team to better get to know the technology Moi was driving using Autodesk software. Autodesk also had the opportunity to demonstrate how smoothly its process control software can be used remotely, since the Moi Composites team was operating the U.K.-based CFM system from Italy.
The printed parts were shipped to Catmarine’s shipyard in Miggiano, Italy, for assembly. Each of the parts were pieced together — “like Lego blocks,” notes Merry Le, business strategy lead at Moi Composites — and adhesively bonded. The entire hull was then laminated via hand layup with an additional fiberglass/polyester layer cored with PVC. This was done, Natale says, to “give the final boat structural continuity.” He adds, “Someday, maybe we will have a machine that can 3D print an entire 6.5-meter boat in one shot. Today, it is a hybrid process between additive manufacturing and traditional manufacturing.” After the hull and deck were fully assembled, sanded and gel-coated, Moi Composites’ partners outfitted the structure with propulsion, navigation and other systems to complete the boat.
assembly and finishing
Next steps for MAMBO and beyond
Initial sea trials and stability tests were performed in fall 2020, with MAMBO reaching speeds of up to 26 knots. Pandemic-related travel issues have delayed additional testing, but Moi Composites plans to continue sea trials in summer 2021, working toward certification of the boat.
“We hope to be able to showcase MAMBO along with our partners such as Autodesk at future tradeshows to demonstrate the potential of CFM technology,” Le says.
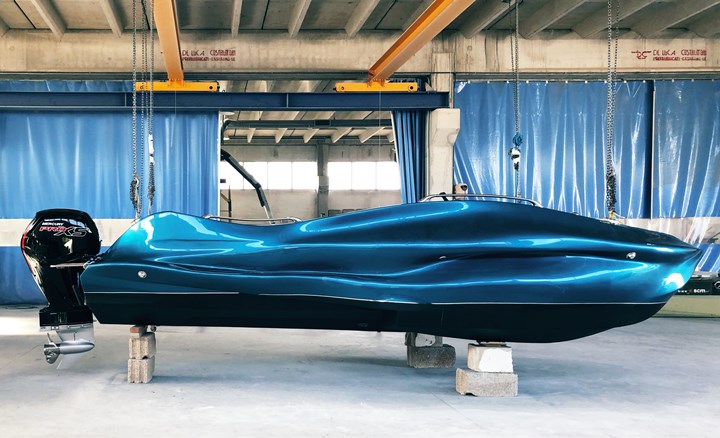
Further trials and testing in 2021 aim toward certification of the boat.
On the materials side, Owens Cornings’ Berthereau hopes this project serves as an example of new ways that glass fiber can be used within composites applications. She says, “This technology merges the advantages of thermosetting composite material with the potentialities of additive manufacturing, enabling total freedom of shape without molds and production of small-series and customized parts. This partnership with Moi is an example of Owens Corning collaborating with startups and other companies to reinvent the way we apply glass fiber technology to deliver customer solutions.”
Müller says one important aspect of the project for Autodesk was the ability to demonstrate how various composites manufacturing products that Autodesk supplies — design software, robotic control systems, additive manufacturing software — can all be connected together into one workflow to simplify design innovation and a complicated manufacturing process. Jason Love, technology communications manager at Autodesk, adds, “This project was a great model of coming together with an organization and really providing the capabilities that the company needed to drive their technology forward. We enable teams to collaborate and plan in a smarter way about a design and manufacturing process, using the cloud, data sets and software to move from tool to tool in a very streamlined fashion so that designers, engineers and others can all look at the current iteration in real time, and can do so remotely.”
Beyond MAMBO, Moi Composites hopes to extend the speed, versatility and flexibility benefits of its technology to other boat and marine projects. Natale notes, “[The combination of] additive manufacturing, digitalization and automation can speed up the creation of new concepts and futuristic projects, because for each boat you want to design, you don’t need to create a new mold. Using this technology, you can easily modify your 3D model and print it again. This is perfect especially for short-run or one-off boats.”
Related Content
JEC World 2022, Part 1: Highlights in sustainable, digital, industrialized composites
JEC World 2022 offered numerous new developments in composites materials, processes and applications, according to CW senior editor, Ginger Gardiner, most targeting improved sustainability for wider applications.
Read MoreCarbon fiber composite hydrofoils to enable “world’s fastest” electric ferry
The Candela P-12 Shuttle, set to launch in Stockholm, Sweden, in 2023, will incorporate lightweight composites and automated manufacturing to combine speed, passenger comfort and energy efficiency.
Read MoreAdvanced Fiberglass Industries: Composites enable innovation
With decades of composites design and fabrication experience, Dubai-based AFI turns problems into solutions.
Read MoreLarge-format 3D printing enables toolless, rapid production for AUVs
Dive Technologies started by 3D printing prototypes of its composite autonomous underwater vehicles, but AM became the solution for customizable, toolless production.
Read MoreRead Next
Large-format 3D printing enables toolless, rapid production for AUVs
Dive Technologies started by 3D printing prototypes of its composite autonomous underwater vehicles, but AM became the solution for customizable, toolless production.
Read MoreCW’s 2024 Top Shops survey offers new approach to benchmarking
Respondents that complete the survey by April 30, 2024, have the chance to be recognized as an honoree.
Read MoreComposites end markets: Energy (2024)
Composites are used widely in oil/gas, wind and other renewable energy applications. Despite market challenges, growth potential and innovation for composites continue.
Read More