Instron introduces 3400 and 6800 Series universal testing systems
New high-force floor models range up to 300-kilonewton force capacity, with a host of new features covering user safety, comfort, repeatability and long-lasting service life.
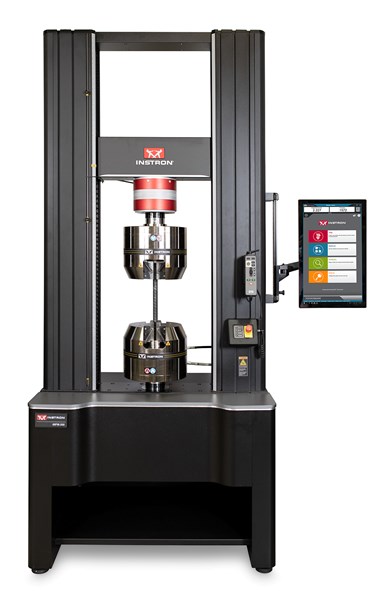
Instron 6800 Series floor model. Photo Credit, all images: Instron
Instron (Norwood, Mass., U.S.) announces the capacity expansion of the 3400 and 6800 Series high-force universal testing systems, successors to Instron’s 3300 and 5900 Series systems. Now available in force capacities ranging up to 300 kN, the 3400 and 6800 Series host new features focused on durability, ergonomics and simplifying mechanical testing of composites.
The universal testing systems provide a new dimension of performance and durability, Instron contends. Reduction in debris ingress has been achieved through gasketing and a patent-pending airflow design. The frames have been fortified against shock and vibration, ensuring continuous testing at the maximum rated frame capacity. Additional design steps were also taken to locate internal electrical and mechanical hardware safely away from the test area, while an abrasion-resistant coating is applied to the 12mm metal work surface for durability.
Both series are equipped with maintenance-free, brushless AC servomotors supporting continuous cyclic, creep and relaxation testing for up to 10 days. The 3400 Series provides a data acquisition rate up to 1,000 Hz and the 6800 Series increases the data acquisition rate up to 5,000 Hz. According to the company, the culmination of these enhancements are meant to secure long-lasting service life.
To reduce the rate of accident reoccurrence during test setup, Instron has built in its patent-pending Operator Protect system architecture along with Safety Coaching, which are designed to limit the machine’s movement during test setup while providing visual machine status reminders to the operator and bystanders. Additional features are also present in setup mode to aid this goal: Crosshead movement speed is restricted, the Smart-Close Air Kit restricts gripping pressure on low force grips to a pre-defined safe level and Safety Coaching uses system lighting and a color-coded border around the software to visually indicate that the machine is in safe setup mode. Once the operator is ready to begin testing, a virtual interlock button allows the enablement of the system’s full crosshead speed, full grip pressure capabilities and triggers visual cues that signify that the safety limits have been removed for testing. System movement on the 3400 Series is controlled from a redesigned Operator Panel, while the 6800 Series introduces a novel ergonomic handset so the system may be operated from a distance.
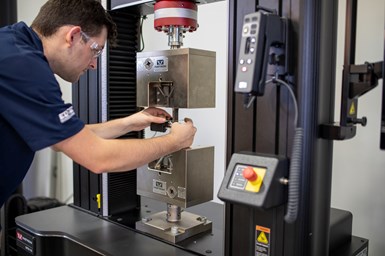
Operator installing clip-on extensometer.
To improve operator comfort, the 3400 and 6800 Series systems are available with a tall base option. The tall base is said to move the testing platform to an ergonomically comfortable height and adds a shelf for storage. The testing systems also have a new contoured base design for improved access to the test space for fixture assembly and a comfortable reach to the control panel on the 3400 Series or the handset on the 6800 Series.
All 6800 Series systems are equipped with an Auto Positioning feature which remembers a pre-assigned fixture separation and the starting location for the assigned test method. When using a test method configured with Auto Positioning, an operator is shown a picture of the assigned fixtures, reminded to set travel limits and notified when and where the crosshead will move for test commencement. The goal of Auto Positioning is to improve data repeatability and reduce testing errors.
Last, the 3400 and 6800 Series systems are equipped with a Collision Mitigation feature to help reduce accidental equipment and specimen damage. Collision Mitigation enables the systems to continually monitor force during jog and return, and will automatically stop the crosshead movement if an unexpected force is detected. Mishaps happen, Instron says, and the goal of Collision Mitigation is to reduce the negative financial and downtime impacts associated with such occurrences.
Related Content
The basics of composite drawing interpretation
Knowing the fundamentals for reading drawings — including master ply tables, ply definition diagrams and more — lays a foundation for proper composite design evaluation.
Read More3D-printed CFRP tools for serial production of composite landing flaps
GKN Aerospace Munich and CEAD develop printed tooling with short and continuous fiber that reduces cost and increases sustainability for composites production.
Read MoreCFRTP enables better, greener smartphones
Carbon Mobile’s “monocoque” design eliminates separate case, cover and frame, better protects electronics and simplifies disassembly.
Read MoreComposite prepreg tack testing
A recently standardized prepreg tack test method has been developed for use in material selection, quality control and adjusting cure process parameters for automated layup processes.
Read MoreRead Next
Composite testing challenges, Part 1: Introduction to mechanical testing of composites
A range of standardized mechanical tests for complex composites are available and still under development for materials development, design and quality control requirements.
Read MoreCW’s 2024 Top Shops survey offers new approach to benchmarking
Respondents that complete the survey by April 30, 2024, have the chance to be recognized as an honoree.
Read MoreComposites end markets: Energy (2024)
Composites are used widely in oil/gas, wind and other renewable energy applications. Despite market challenges, growth potential and innovation for composites continue.
Read More