Anisoprint signs MOU for space-based continuous fiber 3D printing
Continuous fiber co-extrusion (CFC) technology capacities in orbit and for the deployment of additive manufacturing have been demonstrated and validated.
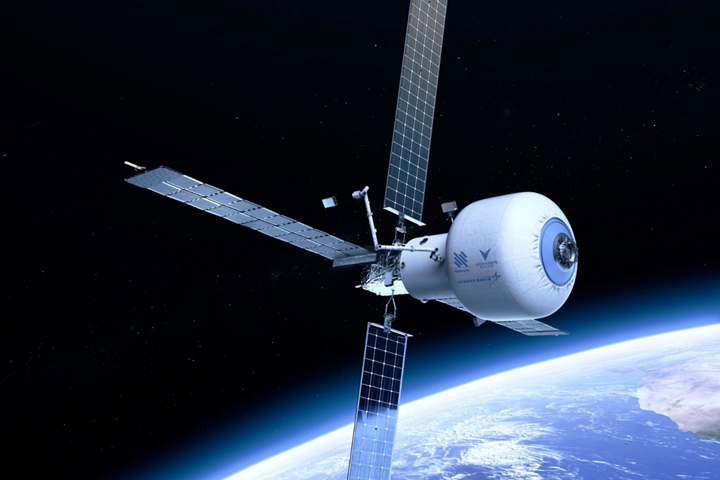
Starlab, the planned LEO space station designed by Nanoracks for commercial space activities. Photo Credit: Nanoracks Space Outpost Europe
Anisoprint (Esch-sur-Alzette, Luxembourg), a continuous fiber 3D printing solution provider, has signed a memorandum of understanding (MOU) with Nanoracks Space Outpost Europe (Houston, Texas, U.S.), a private in-space services company involved in the commercial utilization of the International Space Station (ISS), to strengthen its position as a space technology developer and become a part of the low-Earth orbit (LEO) and lunar economy.
Since Anisoprint was selected for pre-incubation in ESRIC’s Startup Support Program to adjust continuous fiber 3D printing technology for microgravity conditions, the team says it has made great strides toward expanding the resources network. The MOU is said to further secure demonstration and validation of continuous fiber co-extrusion (CFC) technology capacities in orbit and for the deployment of 3D printing manufacturing.
“We are excited to join forces with such an experienced and well-respected in source industry partner. Adjusting CFC technology for microgravity is the first step, the next is to deploy the technology in orbit together with Nanoracks Space Outpost Europe,” Dmitrii Prokopiuk, Anisoprint head of space development, notes. In his presentation at Space Resources Week 2022, Prokopiuk discussed the role of CFC 3D printing for space resources use.
Anisoprint says in space, there is a large demand for on-site production of parts and components. On-site manufacturing minimizes delivery cost and shape limitations, and also reduces the number of delivery missions. Therefore, the company feels its patented CFC technology — which creates zero waste, thus minimizing the amount of space debris and is fully automated manufacturing — is ideal for these kinds of applications.
“With our plans to develop orbit stations and other space facilities to serve the market needs at the best, the role of these innovative in-orbit manufacturing machines are getting more and more crucial,” Veronica La Regina, director business development at Nanoracks Europe, adds. “We are looking forward to experiencing the CFC 3D printing capabilities in our portfolio.”
Related Content
-
Materials & Processes: Fibers for composites
The structural properties of composite materials are derived primarily from the fiber reinforcement. Fiber types, their manufacture, their uses and the end-market applications in which they find most use are described.
-
Materials & Processes: Composites fibers and resins
Compared to legacy materials like steel, aluminum, iron and titanium, composites are still coming of age, and only just now are being better understood by design and manufacturing engineers. However, composites’ physical properties — combined with unbeatable light weight — make them undeniably attractive.
-
One-piece, one-shot, 17-meter wing spar for high-rate aircraft manufacture
GKN Aerospace has spent the last five years developing materials strategies and resin transfer molding (RTM) for an aircraft trailing edge wing spar for the Airbus Wing of Tomorrow program.