Aimplas SPARTA project focuses on recycling composite material methods
The SPARTA project will aim to find more efficient methods of recycling and reprocessing composite thermoplastic materials that reduce the aerospace industry’s overall waste.
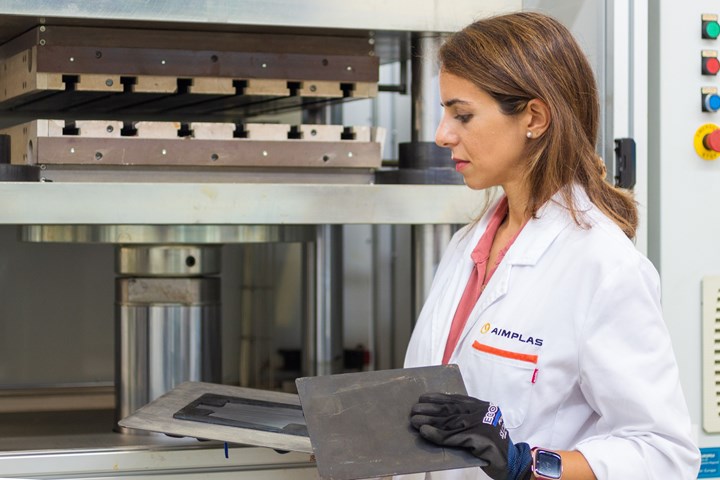
Photo Credit: Aimplas
In response to the challenge the aerospace industry faces in recycling its composite parts and materials, Aimplas (Valencia, Spain) and its partner Tekniker (Eibar, Spain) are coordinating the SPARTA project. Both centers plan to develop a new recycling method for key waste processing and reprocessing procedures with a goal to reduce the amount of waste generated by the aerospace industry, and design more eco-efficient manufacturing methods.
More specifically, it is said that Tekniker will contribute its knowledge and experience in mechanical cutting to the development and optimization of an innovative mechanical scrapping process, through simulation and experimentation, while Aimplas focuses on improving material reprocessing through automatic deposition and compression molding. According to Aimplas, this method will make it possible to use up to 80% of current aerospace waste compared to other mechanical recycling methods, cut processing times as much as 50% by reducing the number of steps in waste recovery, use more efficient automatic reprocessing methods, reduce CO2 emissions up to 30% through the use of waste and curb production demand for virgin material.
Aimplas says the result will be new, high-quality composite thermoplastic products manufactured with recycled materials at a production cost 15-20% lower than current mechanical recycling and scrap reprocessing procedures as a result of the reduction in the number of operations and automation of manufacturing processes. Aimplas notes that it will also be charged with analyzing the properties of the final product, as well as preparing a guide with eco-design recommendations for industrial scale-up of the process.
The project began in September 2020 and will end in October 2022. It has received funding from the EU Research and Innovation programme Horizon 2020 within the framework of the Clean Sky Joint Technology Initiative under grant agreement number 887073. This project is in line with SDG 12 on responsible consumption and production, SDG 13 on climate action and SDG 9 on industry, innovation and infrastructure.
Related Content
-
Materials & Processes: Composites fibers and resins
Compared to legacy materials like steel, aluminum, iron and titanium, composites are still coming of age, and only just now are being better understood by design and manufacturing engineers. However, composites’ physical properties — combined with unbeatable light weight — make them undeniably attractive.
-
Materials & Processes: Fibers for composites
The structural properties of composite materials are derived primarily from the fiber reinforcement. Fiber types, their manufacture, their uses and the end-market applications in which they find most use are described.
-
PEEK vs. PEKK vs. PAEK and continuous compression molding
Suppliers of thermoplastics and carbon fiber chime in regarding PEEK vs. PEKK, and now PAEK, as well as in-situ consolidation — the supply chain for thermoplastic tape composites continues to evolve.