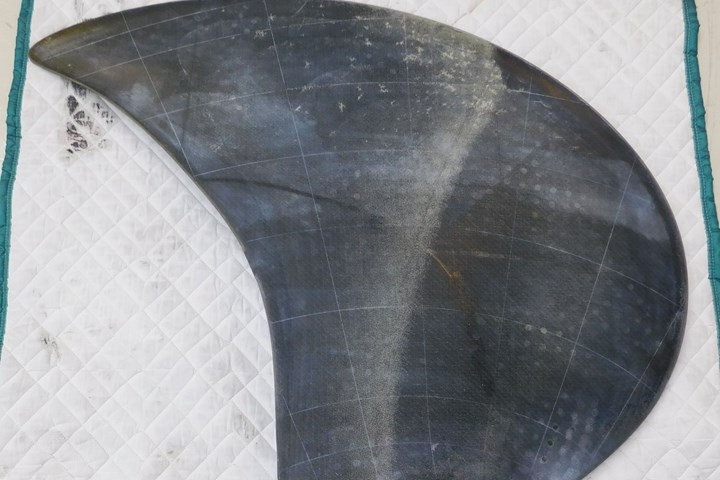
As part of a new partnership with Teijin Ltd., composite recycling consultancy Fuji Design Co. Ltd. has begun a number of R&D projects to prove out its controlled pyrolysis process for higher-performance fiber reclamation. Shown here is a glass fiber-reinforced propeller blade from partner Nakashima Propeller Co. Ltd. prior to pyrolysis (see image farther down for part after pyrolysis). Photo Credit: Nakashima Propeller Co. Ltd. and Teijin Ltd.
In the realm of composites recycling, pyrolysis is a method used to reclaim the original fibers from end-of-life (EOL) parts or scrap by separating resins, sizing, additives and any other substances via a high-temperature furnace. The advantage of pyrolysis is that furnaces can be built at large scale, meaning large amounts of waste can be processed. However, the resulting reclaimed fibers generally are reduced in size and mechanical properties compared to virgin fibers. Such fibers are typically chopped and best suited for applications like spray-up or as a reinforcement in thermoplastic resins used in injection molding or extrusion.
Fuji Design (Ono City, Japan) recently announced a partnership with carbon fiber producer Teijin Ltd. (Tokyo, Japan) to scale up its precision pyrolysis technology, which uses controlled heating and cooling to reportedly reclaim higher-performance fibers via pyrolysis, and potentially also resins.
Controlled pyrolysis for reclaiming higher-performing fibers
After a decades-long career in the steel industry, Fuji Design CEO Morihiko Sugino transitioned into research work on new materials, including carbon fiber-reinforced thermoplastic (CFRTP) composites. He soon recognized the challenges posed by high costs and supply instability of high-quality carbon fiber, leading him to begin investigating recycled carbon fiber (rCF).
The glass fiber composite propeller part after pyrolysis, showing intact fibers without surface oxidation damage.
Photo Credit: Nakashima Propeller Co. Ltd. and Teijin Ltd.
Sugino founded Fuji Design Co. Ltd. in 2011, and today the company operates an R&D facility/company headquarters and a compounding factory in Ono City, with an additional corporate office in Kobe. Over the past decade, Fuji Design has primarily worked in a consulting capacity, helping companies work with composites and rCF, while also working internally on fiber reclamation technology for mass production of high-quality rCF.
The key to the company’s precision pyrolysis technology is a specially designed furnace that ramps up and down in temperature according to controlled, preprogrammed settings based on the part’s resin matrix, fiber type and size.
The overall purpose is to effectively melt off the resin while preventing mechanical property-reducing surface oxidation damage to the fibers during pyrolysis. According to Fuji Design’s research, the maximum temperature and air pressure within the furnace that a part can be exposed to before the fibers start to oxidize is 500°C (932°F), and 18% oxygen pressure. Temperatures for other pyrolysis processes vary, but can reach up to 800°C (1472°F) or more. Fuji Design’s process, therefore, involves precise control of the heating temperature and pressure via programmed, timed cycles of heating, ramping up to a maximum temperature of 500°C (932°F) and cooling back down in short bursts. Oxygen pressure is controlled between 16-18%.
Specifically, Fuji Design’s process involves a ceramic fiber furnace with a fully automatic liquid propane gas (LPG) burner — less costly than a traditional furnace, the company claims, and operated at a lower cost. The current furnace size is 2 x 2.5 x 3 meters (6.5 x 8.2 x 9.8 feet) with a total inner volume of 15 cubic meters.
The process is a seven-hour cycle from room temperature to ramp up to cooling (below 300°C/572°F). The first heating cycle starts at 300°C (572°F), at which temperature the resin begins to decompose. Next, at 300-380°C (572-716°F), depending on the specific programming for a part, delamination occurs and the fibers and resin begin to separate evenly. Between 400-480°C (752-896°F), the separated resin is carbonized and gradually oxidized, leaving the fibers in their original shape. The result is separated fiber that is said to exhibit up to 93% of the strength of the original fibers, and can be processed similarly to virgin fiber.
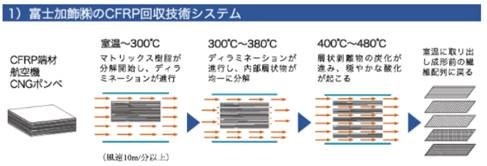
Fuji Design’s precision pyrolysis process. In the first step (second image), the matrix resin starts decomposing at 300°C (572°F). Second, delamination begins and the layers are decomposed evenly at 300-380°C. Third, the peeled members from the layers are carbonized and then gradually oxidized at 400-480°C. Last, the fiber structures are back to the shape before the molding process. Photo Credit: Teijin Ltd.
Current projects and moving toward commercialization
At its R&D facility, Fuji Design has demonstrated the furnace recycling a variety of EOL parts like aircraft components, hydrogen storage tanks, and wind turbine blades, processing carbon fiber and epoxy or vinyl ester resins. The precision pyrolysis process has resulted in recycled carbon fibers that Fuji Design can provide as is or process into nonwoven fabrics.
Future developments that the company is working on include reclaiming resin matrices, including thermoplastics. For thermoplastics, Fuji Design’s goal is to develop mass production of 50-100-millimeter fiber length and 40-60% long-fiber composites in-house within two years.
Beyond continuing R&D, the ultimate goal is to scale up and sell this process commercially. As part of this goal, Teijin Ltd. and Fuji Design began their partnership in December 2021, and since then several projects have already been launched, including R&D projects with resin companies and with automotive, sporting goods and industrial applications. As part of this partnership, Teijin will process recycled materials from Fuji Design into intermediate materials like rCF pellets and prepregs.
Related Content
Bioabsorbable and degradable glass fibers, compostable composite parts
ABM Composite offers sustainable options and up to a 60% reduction in carbon footprint for glass fiber-reinforced composites.
Read MoreTU Munich develops cuboidal conformable tanks using carbon fiber composites for increased hydrogen storage
Flat tank enabling standard platform for BEV and FCEV uses thermoplastic and thermoset composites, overwrapped skeleton design in pursuit of 25% more H2 storage.
Read MoreCryo-compressed hydrogen, the best solution for storage and refueling stations?
Cryomotive’s CRYOGAS solution claims the highest storage density, lowest refueling cost and widest operating range without H2 losses while using one-fifth the carbon fiber required in compressed gas tanks.
Read MoreDaher CARAC TP project advances thermoplastic composites certification approach
New tests, analysis enable databases, models, design guidelines and methodologies, combining materials science with production processes to predict and optimize part performance at temperatures above Tg (≈150-180°C) for wing and engine structures.
Read MoreRead Next
Recycling end-of-life composite parts: New methods, markets
From infrastructure solutions to consumer products, Polish recycler Anmet and Netherlands-based researchers are developing new methods for repurposing wind turbine blades and other composite parts.
Read MoreThe state of recycled carbon fiber
As the need for carbon fiber rises, can recycling fill the gap?
Read MorePressurized steam-based composites recycling for full fiber reclamation
Longworth’s DEECOM process for composites recycling claims to produce intact fiber and resin reclamation with near-virgin properties.
Read More