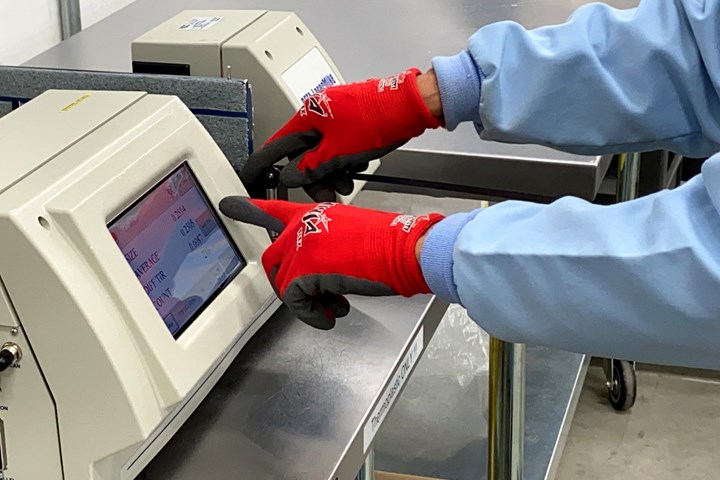
According to Web Industries, as commercial-scale thermoplastic composite production has matured, improvements in material consistency and uniformity have increased yields and reduced quality assurance testing burdens. Shown here is width testing for thermoplastic composite slit tapes. Photo Credit, all images: Web Industries
Aerostructures production has been heavily impacted by the COVID-19 pandemic, but aerospace efforts did not necessarily follow suit, at least for Web Industries (Marlborough, Mass., U.S.), a company that offers thermoplastic tape-slitting services for a variety of customer applications. According to Grand Hou, global director of research and technology, aerospace, research efforts in space, urban air mobility (UAM) and military have been going full-throttle to enable the next generation of aircraft — and composites, specifically thermoplastic tapes, have been key to many of these efforts.
Thermoplastic tapes aren’t new, of course (see CW Editor-in-Chief Jeff Sloan’s “I want to say two words to you: ‘Thermoplastic tapes’” for more of the backstory dating back to the 1960s), but the past few years have seen an increase in their interest, particularly for commercial aerospace and other high-performance applications (such as ribs for the Wing of Tomorrow program and the Multifunctional Fuselage Demonstrator program, among others). Compared to thermoset tapes, thermoplastics offer advantages such as higher toughness, easier recyclability, their ability to be processed out of autoclave (OOA) and the fact that they can be stored at room temperature.
Web Industries is at the front line of thermoplastic development and applications, most notably with its multiple formatting capabilities, which include slitting of thermoset and thermoplastic tapes from suppliers into different shapes and formats to meet specific customer requirements. With tape slitting production lines based in U.S. and European facilities, Web’s capabilities include formatting high-performance polyetheretherketone (PEEK), polyetherketoneketone (PEKK) and polyaryletherketone (PAEK) thermoplastic tapes, which are most commonly used in aerospace applications.
TP tapes for secondary aerostructures — and challenges in primary structures
Currently, Hou notes, most aerostructures activity in thermoplastic prepregs centers on secondary structures such as clips, access panels or substructures, while flight-critical primary structures like wings and fuselages are made with thermoset composites or metals.
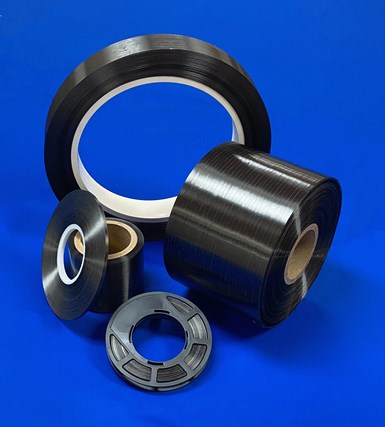
Thermoplastic prepregs can be formatted for a wide range of automated manufacturing technologies, including spooled slit tape for AFP, pad wound tapes for ATL and reeled filaments for additive manufacturing.
“A lot of the challenges are about managing risks,” he says, and part of the issue has historically been the growing pains of thermoplastic prepregs from suppliers. Thermoplastic materials are less mature than thermoset tapes. According to Hou, while thermoset tapes have had decades of large-volume production to scale and perfect, thermoplastic materials are in the infancy of usage in automated processes for large-volume production.
However, Web Industries works with a variety of composite materials suppliers, and Hou says that overall material consistency and scale has improved greatly over the past few years. Material width, length, thickness, fiber tension and resin uniformity are all much more consistent and of a higher quality today, he says.
Another prohibitive factor to making larger thermoplastic primary structures is that thermoplastic materials tend to be more expensive than thermosets. “It won’t be more widely adopted if there is not an overall cost advantage,” Hou admits, noting that collaboration and technical help are critical to help drive down process costs. “We can achieve better solutions when everyone works collaboratively from the early stages of the project to the end to achieve common goals.”
Process flexibility and material customization
Overall, Hou sees a lot of potential and increasing activity for thermoplastic tapes now and in the future, with flexibility being one of the main tipping points for customers.
Currently, thermoset tapes are confined primarily to automated fiber placement (AFP), with the limitations of autoclave cure and storage temperature requirements. Thermoplastics can enable a more flexible process approach as well as OOA processing, Hou says, including tape formats for automated tape laying (ATL), and filaments for additive manufacturing.
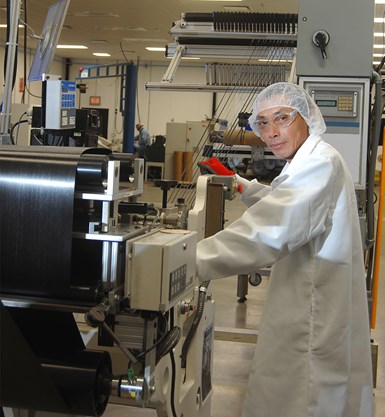
According to Web Industries, commercial-scale formatting and supply chain solutions will be critical in providing aerostructure fabricators the thermoplastic slit tapes required to support projected industry build rates.
Thermoplastic prepregs can also be tailored for specific applications. According to Hou, end users are looking to match materials to each application. Because thermoplastics are highly adaptable, a specific format can be developed for a specific part, he says, maximizing material usage and reducing the customer’s downstream costs. With UAM, space and the military being high areas of activity, Ashley Graeber, director sales and new business development, notes that activity is being tailored per project, rather than per aircraft program.
Formatting thermoplastic materials for specific applications also helps reduce waste, says Jason Surman, VP sales, aerospace. In the aerospace industry, the buy-to-fly ratio, which is the ratio of the raw material to the mass of the finished part, is a key concern. The goal is to have a buy-to-fly ratio as close to 1:1 as possible, meaning there is little waste material. The right material in the right format for the right application can drastically reduce waste, Surman notes. In the aerospace industry, 30% waste is “crazy common,” he says, and to get the waste below that level requires a collaborative effort on all sides.
“Marrying the material to the process is critical,” Surman adds, “and thermoplastic tapes are emerging as an enabling solution for aerostructures manufacturers.”
Related Content
Understanding vacuum bagging layers in production, repair
Recognizing the functions of each layer in a vacuum bag schedule can help users discover what vacuum bag schedules work best for their application.
Read MorePlant tour: Renegade Materials Corp., Miamisburg, Ohio, U.S.
Renegade Materials is known for high-performance prepregs for aerospace applications. Following its acquisition by Teijin in 2019, the company has expanded capacity and R&D efforts on a range of aerospace-targeted materials.
Read MoreComposite prepreg tack testing
A recently standardized prepreg tack test method has been developed for use in material selection, quality control and adjusting cure process parameters for automated layup processes.
Read MoreMeasuring ply-wise deformation during consolidation using embedded sensors
Strip-type shape sensor method claims real-time measurement of ply-wise deformation.
Read MoreRead Next
I want to say two words to you: “Thermoplastic tapes”
Thermoplastic tapes are not new to composites, but they soon will join the primary aerostructures material palette and could be their future.
Read MoreComposites end markets: Energy (2024)
Composites are used widely in oil/gas, wind and other renewable energy applications. Despite market challenges, growth potential and innovation for composites continue.
Read MoreFrom the CW Archives: The tale of the thermoplastic cryotank
In 2006, guest columnist Bob Hartunian related the story of his efforts two decades prior, while at McDonnell Douglas, to develop a thermoplastic composite crytank for hydrogen storage. He learned a lot of lessons.
Read More